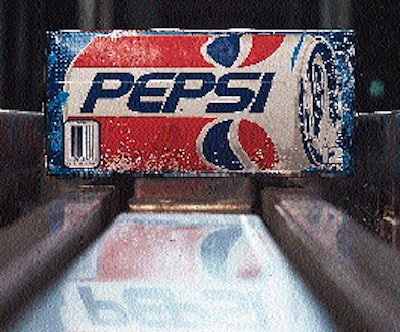
When it came time to select 900' of conveyor to carry 12-pack beverage cartons, National Brands Beverage Ltd. plant manager Gordon Hall knew what he didn't want. He didn't want a system that would mar the litho-printed graphics on 12-pack cartons of Pepsi and Diet Pepsi. The Pepsi bottler sought the conveyor to move the packs from packaging to a distant palletizing area. "I saw the problems at other beverage plants," he says. "You could see the lithographic ink come off the cases onto the conveyor. They were constantly cleaning the line. I didn't want to be tied to that kind of maintenance scheduling." He also wanted to eliminate the "cookie cutter" effect--where the cartons become "embossed" with the can pattern inside due to the bouncing impact of roller conveyors. To avoid both problems, the Pennsauken, NJ-based bottler purchased a Lite-Touch(TM) conveyor from Ambec (Owings Mills, MD) that's unique in two respects. Instead of rollers, it uses DuPont's Teflon®-impregnated plastic chain to gently convey cases, providing a smooth and consistent ride. Another unique feature, pop-up accumulation bars, lift the cases off the moving conveyor in the event of a palletizer stoppage, eliminating ink rub-off. The pop-up accumulation bars are 10'-long segments that run the entire length of the conveyor. The moving plastic chain is on either side of the bars, so that during normal use, the paperboard packs travel right over the pop-up accumulation bars, which are recessed. When sensors located at each segment detect carton accumulation, the bar pops up, lifting cases above the surface of the chain. When the back-up ends and sensors detect movement of cases, the bars retract, gently depositing the cases back on the moving conveyor. Cases are lifted off the conveyor a 10' section at a time. The conveyor operates at speeds to 120'/min. A final benefit is that spare parts need not be maintained for belts or rollers, since the conveyor uses neither. The result is that cases are free of scuffs or cookie cutter imprints, according to Hall. And after more than a year of operation, all 900' of conveyor has worked perfectly, without servicing, says Hall.