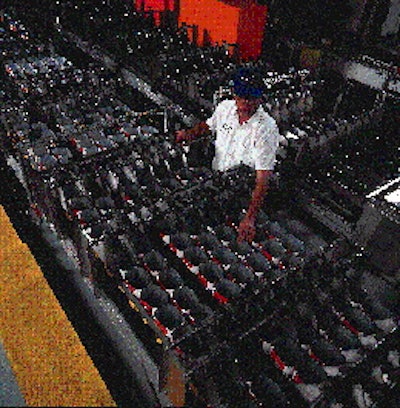
A new linear forming system and a new base heat-sealing process have opened up canister production to a wide range of shapes and sizes at Sonoco. At its Hartsville, SC, headquarters, Sonoco's Package Development Center is now operating a "pilot line" that is producing the new rectangular paperboard container for Englewood, NJ-based Thomas J. Lipton's restaging of its sugared iced tea products (see p. 30).
The Lipton introduction culminates a three-year program. Both vendor and customer created inter-organizational teams to implement the conversion. "We could not have completed this program without a one-hundred-percent team effort from day one between Sonoco and Lipton," stresses Bruce Belowich, Lipton's director of packaging development.
The new line uses technology first used in Europe for drink cups and other forming of paperboard. Unlike spiral-wound or convolute round cans, the new process is not restricted by shapes. The design for Lipton is what Sonoco calls a "swell" shape because both main panels of the rectangular container are rounded or convex. Sonoco currently uses two sets of tooling to produce the Lipton canisters in two cross-sections or footprints; with different heights, the two cross-sections now yield five different sizes for Lipton.
The process does require a bodystock that's somewhat stiffer and more rigid so the container will maintain its shape from forming to bottom sealing and eventual filling and closing. For Lipton's containers, the paperboard structure is considered a high-performance material. Although Sonoco elects not to divulge all the specifics, Lipton's container bodystock includes two plies of 15-pt Duroboard, a 100%-recycled paper that includes 90% post-consumer recycled content. This is adhesively mounted on the inside to an unspecified layer of aluminum foil with Surlyn® from DuPont (Wilmington, DE) used as the sealant layer. On the outside is a paper label printed by gravure.
The paper label is converted by American Packaging Corp. (Rochester, NY). It employs a special 40# paper imported from France for its high-gloss characteristics, says Mike DuRoche of American Packaging. The stock is printed by gravure in seven or eight colors, and is finished with a catalyzed two-part lacquer that offers excellent gloss and superior scuff resistance. Printed in wide-web format, American's Columbus, WI, plant ships the label material to Sonoco in rolls from 13" to 17" wide, depending on container size.
"This board stock has different properties from what we used with the round canister because we need it to hold shape better," says Craig Autry, Sonoco's market manager for nonround containers. "It has to be stiffer and more rigid, and it's easier to form into a shape and to seal the paper bottom."
If there is real "magic" in the container, it's probably in the proprietary prelaminated paper/foil/Surlyn structure used for the base. Currently, the new line heat-seals the base to the sidewall stock, although other seal technologies are being explored. These might include combinations of heat and hot melt adhesives, Autry says, along with other types of seals.
Broadening the options
For the container manufacturer, the new technology promises to remove many restrictions on typical paperboard packaging. Not only does the process permit different shapes and sizes, it allows the use of a paper bottom and it provides a totally predecorated container. In the past, Lipton labeled its spiral-wound canisters on its packaging line.
In Sonoco's view, the breakthrough Lipton package is the first salvo in an attack on consumer attitudes about paper packaging. "We're trying to change the image of traditional paper-bottom packages," Autry says. "We want the consumer to view a paper-bottom container as one that can have high barriers and high performance. That hasn't been the case with conventional paper-bottom canisters for oats or grits."
Sonoco also recognizes that the materials and even the process will offer more options in the future. For applications less demanding than Lipton, the foil could be replaced by metallized materials, Autry notes. For more demanding products, the company believes it will be able to produce hermetic seals for the bottom and for the membrane at the top. That would permit use by oxygen-sensitive products like nuts and snacks.
How process works
While Sonoco admits the pilot line is based on European technology, it declines to identify how the company acquired the rights. Autry did say the Europeans didn't typically use it to produce high-performance containers there. "We're adapting the technologies to use them here for medium- to high-barrier packaging," he says.
The material for the line is produced in web widths wider than is typical for spiral-wound cans. In the forming process, the material is brought down and around the forming mandrel in a linear fashion. This is why the body stock must be stiffer, according to Autry. Once formed and vertically sealed into a tube, the tube is cut into individual containers.
From forming and cutting, the containers are conveyed to the machine that forms and heat-seals the separate paper laminate bottom to the sidewalls. Beading of the top edge is also done before the canisters are released for palletizing into tiers for shipping to Lipton.
"Beading the edge of a nonround shape is also new to us," Autry notes. Similarly, Sonoco had to develop special material handling equipment. The conveyors that carry the formed containers from cutting to bottom application had to be specially engineered so there would be no line back pressure on the containers. Avoiding pressure on the containers helps them maintain both shape and orientation. Currently, the process offers first-in/first-out handling of the containers.
"One of the features of this line is that we can maintain orientation of the container label so that all front panels will be facing the same direction when we build our pallet loads," Autry claims. "Thus, a customer may choose to maintain the orientation in his line from depalletizing through case packing." Palletizing and maintaining effective patterns is quite different with nonround containers, he adds.
Complete source
For Lipton, Sonoco not only makes and ships the containers, it also provides the foil/Surlyn inner seal material and the overcap.
"We're the 'one-stop-shop' for Lipton," says Steve Gendreau, Sonoco account representative. "Our relationship with Lipton gives us complete involvement in a customer's packaging operation. Because we supply the total package, we create time and resource efficiencies for them."
For now, Sonoco inventories containers at its Suffolk, VA, plant, near Lipton's packaging plant in the same city. At some point in the future, the pilot line at Hartsville is expected to be installed at Sonoco's Suffolk plant so sourcing and shipping will be even more convenient. For the foreseeable future, Sonoco can use spare production time on the line to test other materials and processes.