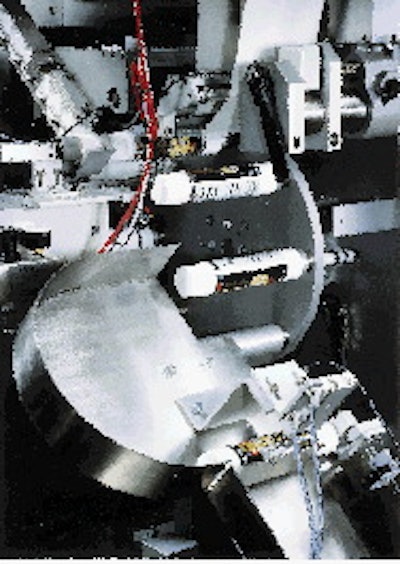
When Henkel Home Improvements & Adhesive Products added a new product to its line, the company decided it was time to update its labeling and capping process. To do this, the Winsford, England-based company partnered with Harland Labelling Systems (Manchester, England) to develop the Harland Orion tube labeling/capping system. It allows Henkel to buy undecorated low-density polyethylene tubes rather than preprinted tubes for its 30-plus products.
"The change was made to increase flexibility in terms of raw materials," says Gordon Hill, total productive maintenance facilitator at Henkel. "We went into partnership with Harland because of the history we have with them. Their engineers communicate very well with our engineers, and together they worked on the project to develop the Harland labeler from scratch."
The engineering team of Henkel and Harland was asked to develop a pressure-sensitive labeling machine that would not only convey empty tubes from a hopper to a labeling station and apply a label, but also feed and apply a cap and then transfer the capped and labeled tube to an in-line filling and sealing machine.
Previously, Henkel bought preprinted, capped tubes. Each time the company wanted to fill another product or have a different decoration on the tube, it had to strip everything off of the filling machine. The preprinted tubes went back to storage and new tubes were brought out and loaded into the filling machine. Hill says changeover took around 20 minutes. "Now the same changeover takes less than two minutes because all we need to do is change the label," he says. "It literally takes one or two minutes now." Hill says because of the quick changeover, production has increased by 50%. Having quick-release handles and not having to use tools, makes changeover that much easier.
Because of new management directives at Henkel, the engineering and production teams had to adhere to just-in-time principles. They also had to implement something called "Total Productive Maintenance." TPM focuses on increasing individual operator skills and equipment effectiveness. This means that during every stage of development, the Harland and Henkel labeler development team had to test and verify every action to minimize operator movement and involvement. Because of this directive, the team was able to develop a machine that worked best for the company.
The new system, which was installed about a year ago, provides simultaneous capping and labeling of the tubes, which are then fed into the filling and sealing line. This combination of capping and labeling has freed up space around the machine. Hill says the Harland Orion frees up 8 sq m (26.24 sq') because the various preprinted tubes no longer have to be stored near the filling machine.
The Orion is fully servo-driven. It applies a wraparound film label to tubes at speeds to 50/min. The tubes, sup-plied by Cebal (Northampton, England), are separated by the infeed product handling system. It feeds each tube onto one of eight mandrels attached to a round disk. Holding the tubes horizontally on the mandrels, the disk ro-tates the tubes through the labeling and capping station. The mandrel spins the tube while the label and threaded cap, also supplied by Cebal, are applied in one movement. As the disk finishes a rotation, the tube is sent toward the filling system. A pneumatic orientation unit then flips the tube 180 degrees so it is in the proper orientation to be fed into the filling system. The tubes are bottom filled and then heat sealed.
Not only did Henkel realize a reduction in changeover time, the company also benefited from the superior graphics that can be achieved on a label compared to the printing done on a tube. Supplied by Burall Carwood (Liverpool, England), the labels are offset printed in four colors.
"We couldn't achieve the same standards by printing on a tube," says Hill. "We also use the labels to differentiate among different products. For products that are at the lower end of the price range, we don't use such a high-definition label. The 'No More Nails' product is quite expensive, so we used a very high-impact label." Henkel's products range from £1.50 (U.S.$2.41) to £3.00 (U.S.$4.83) for a product like No More Nails, and come in sizes ranging from 40-ml (1.35-oz) to 260-ml (8.79-oz).
All of these benefits add up to a quick payback on Henkel's investment. Hill projects the Harland Orion machines will be repaid in less than two-and-a-half years. "We found a solution to a flexibility problem that, as far as I'm aware, our competition hasn't," says Hill. "We have a competitive edge over our competition, and this has translated into increased sales."