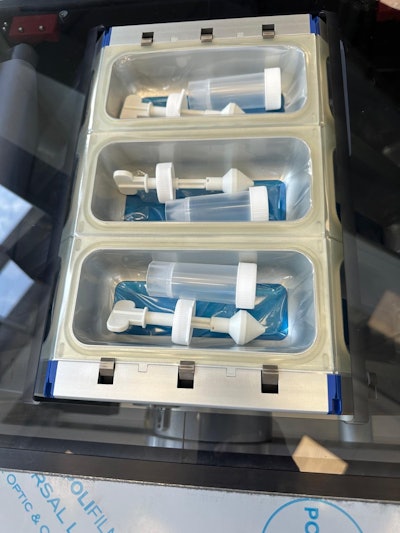
This content was written and submitted by the supplier. It has only been modified to comply with this publication’s space and style.
Key Takeaways:
· BMP’s packaging method was inefficient in terms of material usage and labor requirements.
· Shawpak’s compact 32-20 rotary thermoforming machine offered the flexibility and efficiency required for BMP’s production process.
· The collaborative approach resulted in a package that was significantly smaller, reducing material consumption by over 60%.
The Challenge
BMP Medical is a world leading manufacturer and supplier of tissue grinders. The company’s packaging method for the grinders, utilizing pre-made pouches (72sq/in size,) was inefficient in terms of material usage and labor requirements.
“Lead times from the supplier of these pre-printed bags posed the issue of backorders,” says Rawleen J. White, general manager at BMP Medical.
This spurred the company to find a more efficient and cost-effective packaging solution for their products that would also require less labor and materials.
The Solution
BMP Medical first met Shawpak at MD&M West Pack 2024 while seeking a small footprint thermoforming packaging machine. Shawpak’s compact 32-20 rotary thermoforming machine proved to be the ideal fit for BMP’s needs, offering the flexibility and efficiency required for their production process.
‘’A lot of the processes at BMP are automated with heavy investment in recent years in robotic cells. The packaging of our tissue grinder product range has always been an area where we knew we could improve the efficiency by automating the packaging process. Over the years we have looked at various thermoform machines, but all were very large in footprint which prevented us from making the change,” says Michael T. Faulkner, chief executive officer & president, BMP Medical.
Shawpak's application engineers worked closely with the engineers at BMP Medical to design a unique thermoformed package to best suit the product while minimizing material usage, and of course in a compact footprint. The new package to replace the pre-made bags are thermoformed blister packs that are smaller in size. This collaborative approach resulted in a package that was significantly smaller (28sq/in vs. the previous 72sq/in pre-made pouches), reducing material consumption by over 60%. This means more packs per case, reducing the cost in sterilization and shipping, plus, as White explained, the end user will need less space to store the product.
“While visiting the 2024 MD&M tradeshow in Anaheim, CA we came across Shawpak and saw firsthand their unique Rotary Thermoform Machine; it was ideal for what we needed. Working with the Shawpak application engineers we quickly made prototype packages, which looked great and gave us the confidence to move ahead with the machine purchase – four months later the machine and tool were complete and heading to our facility in Massachusetts,” says Faulkner.
The implementation of Shawpak’s medical thermoforming packaging solution has provided substantial benefits for BMP Medical:
- Reduced Material Consumption: The smaller thermoformed package leads to a significant reduction in material usage, resulting in cost savings and a smaller environmental footprint.
- Increased Efficiency: The new packaging process will streamline operations and reduce staff from 4 per week to 2 over 1.5 shifts, providing a significant cost savings. This will allow BMP Medical to increase production without additional labor.
- Improved Cost-Effectiveness: The combined reduction in material and labor costs significantly improves BMP Medical's overall cost-efficiency.
“We are currently evaluating/considering four to five other products for this new system,” says White.