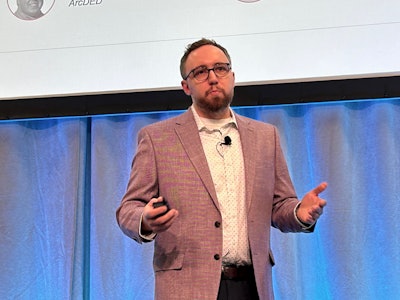
At the Collaborate 2025 event hosted by Universal Robots in February, Daniel Vrana, automation team lead at EWI’s Buffalo Manufacturing Works, demystified automation implementation with a nine-step process. EWI’s Buffalo Manufacturing Works is an advanced manufacturing center that supports small to mid-sized manufacturers—particularly in Western New York—on their journey toward automation and innovation.
In his session, “Approaching Automation Implementations: Strategies for Success and Sustainability,” Vrana didn’t just speak to the what of automation—he dove deep into the how, offering both strategic wisdom and real-world stories from the manufacturing floor.
“Automation isn’t a one-size-fits-all solution,” Vrana advised the audience. “You have to treat it like a living, breathing project that evolves.”
For companies curious about dipping their toes—or taking a confident leap—into automation, here’s Vrana’s roadmap:
- Identify Key Stakeholders “Leadership, engineers, operators—they all wear different hats, and sometimes the same person wears all of them,” Vrana said. Whether your team is 10 people or two, clearly defining roles is crucial to making sure the project has direction and ownership. A project without a champion is one that’s likely to stall.
![]() | Read this related article, “The Future of Automation Sees Greater Human and Machine Collaboration” |
- Acknowledge Existing Hurdles Don’t sweep past your challenges—lean into them. From outdated equipment to cultural resistance, it’s important to identify these head-on. “The second you pretend past failures didn’t happen, you set yourself up to repeat them,” Vrana warned. Instead, ask your team: What didn’t work last time, and why?
- Understand Your Manual Processes Before you automate, map the manual process in detail. And then, dig deeper. “You think the process is: load, press a button, unload,” said Vrana, “but then you find out there’s a flip, an inspection, a decision tree—suddenly, it’s a completely different problem.” Engage operators early—they often hold the tribal knowledge that process flowcharts miss.
- Define and Assess Value This is where ROI gets personal. Maybe your biggest challenge is labor, or maybe it’s throughput. “One company told us, ‘It’s not about the money. I just need to know if automation is the future of my business,’” Vrana recalled. Know what matters most to your operation before you start measuring success.
- Involve External Resources Even the scrappiest teams can benefit from outside expertise. Whether it’s site assessments or feasibility studies, leaning on integrators and technology experts can prevent costly missteps. “Not every integrator is right for every job,” Vrana cautioned. “Find someone who knows your process.”
- Conceptualize and Compare Options Avoid starting with the hardest application. Begin with something that’s already been automated elsewhere. “Start with a win before aiming for lights-out manufacturing,” Vrana advised, urging companies to avoid biting off more than they can chew.
- De-risk with Proof of Concept Run a test, and make it specific. Generic demos don’t build confidence like seeing your parts on your machine. “The second you see your part move, the gears start turning,” said Vrana. It also aligns expectations across your team, especially when different stakeholders envision very different outcomes.
- Form an Implementation Plan Take all that groundwork—your goals, tech comparisons, timelines, and team structure—and build it into a formal plan. Include incremental milestones and don’t forget about lead times. “You can have everything ready and still be waiting on a single component,” Vrana pointed out.
- Prepare the Workforce Upskill, reskill, and support your team. Training needs to go beyond pushing buttons. “The biggest gap isn’t moving the robot—it’s applying that to your real-world task,” said Vrana.
Lessons from the Floor
Two case studies showcased how this framework plays out in real life. One involved the Northland Workforce Training Center in Buffalo, where students run machine tending cells as part of their curriculum. The project helped them run thousands of parts—and offered hands-on exposure that’s already shaping careers.
Then there was Cook Metal Spinning. Faced with a cramped floor and skeptical workers, owner Eric Cook saw value in just trying automation. “I need to see if this is the future of my business,” he said in a video shared by Vrana. Today, that pilot project has evolved into a flexible system that gives operators time back and opens up new possibilities.
Final Thoughts
If there’s one takeaway from Vrana’s talk, it’s this: automation is not about chasing a trend—it’s about solving your problems, on your terms.
“Small wins lead to big wins,” Vrana said. “Start small, prove it out, and grow from there.” PW