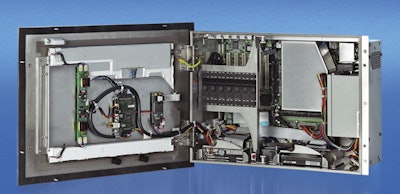
When a major cereal maker looked for a way to reinvent bag-in-box packaging, they turned to the Aagard Group for a servo-centric solution. Aagard responded with a 36-axis side-seam gluer/cartoner/case packer/palletizer that, says Aagard’s Brent Smith, occupies about a sixth of the floor space and costs about half of what might have been required for a more traditional solution. Fed by two baggers, the new system cranks out 120 cartons/min.
“Counting the smart-belt infeed, it’s five unit operations in one frame,” says Smith. “We can ship the complete unit—cartoner, case packer, palletizer—in a sea container that has an 8’ x 8’ opening. And because it’s all on one frame, we can install this system and get it into production in about a tenth of the time it might take with more conventional approaches.”
The traditional bag-in-box system opens a knocked-down carton that has a pre-sealed manufacturer’s joint, puts the blank in a flighted conveyor, and then pushes a bag of cereal into the carton. But the patent-applied-for Aagard system uses flat carton blanks that have an unsealed manufacturer’s joint. Cereal bags are fed into a bucket, the carton is formed around the bucket, and the bucket is then pulled out.