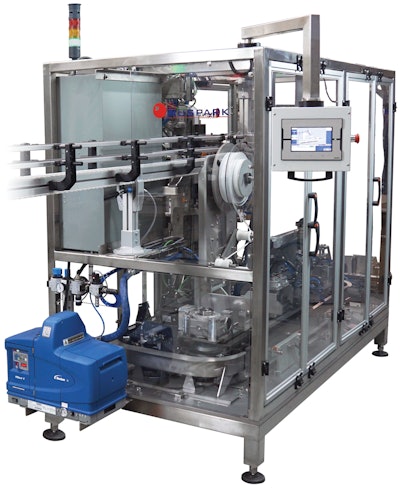
Afirst-of-its-kind, custom-built applicator for tin-ties—those familiar reclosure features on bags of coffee, both whole-bean and ground—recently went into production at Barrie House Coffee & Tea Co. in Elmsford, NY. Director of Sales and Marketing Shay Zohar, who helped drive packaging machinery manufacturer Nuspark to develop the unique system in the first place, is so pleased with the advantages it brings that he’s ordered a second to be delivered as soon as possible.
To understand Zohar’s enthusiasm for the Nuspark NTT-35, it helps to understand how tin-ties were applied at Barrie House in the past. Sometimes it was done manually, an approach with obvious drawbacks from a cost and efficiency standpoint. Other times it was done on an automated packaging system from ICA that combined vertical form/fill/seal functionality with in-line tin-tie application. Though this automated approach certainly minimized labor costs, it’s a fairly complex and multi-component piece of equipment. So changing over from one bag size to another took more than a day.
Zohar could have invested in another one of these automated vf/f/s + tin-tie application systems. But they cost anywhere from $750K to $1.3 million. The other downside to this approach is that once you invest in such an integrated system, you’re hamstrung in your ability to jump on new developments should they emerge in either vf/f/s or tin-tie application technologies. After all, it’s not like you can divorce the vf/f/s half of such an integrated system from its tin-tie application half. The two functionalities are tightly and irrevocably integrated.
“The great thing about having the tin-tie application equipment located immediately downstream from the bagging equipment is that if we decide to upgrade or replace a bagger for $200,000 or so, the tin-tie applicator stays right where it is and we integrate it with the new bagger,” says Zohar.
Since the Nuspark NTT-35 was installed, application of tin-ties by hand has been greatly reduced. It will be practically eliminated once a second Nuspark system is in place. “By the time the second NuSpark tin-tie unit is installed and running,” says Zohar, “we’ll save something like $25,000 dollars a month in manual labor.”
Another spin-off benefit gained once the first NTT-35 was installed is that the ICA machine can now be dedicated to one bag size. Consequently, changeover-related downtime on that machine has been eliminated.
Hand-off at floor level
The Nuspark NTT-35 is an intermittent-motion machine. It applies tin ties to both 12-oz and 2.5-lb fin-seal flat-bottom bags at 25 to 35 bags/min. Changing from one size to the other takes about 20 min and is guided by visual step-by-step instructions at the HMI.
A key design requirement behind it was that it needed to receive bags at the level where a typical vertical form/fill/seal bagger discharges them, which is to say floor level. So the Nuspark machine’s oval-shaped race track whose buckets receive freshly made bags and take them through tin-tie application sits about one foot off the floor. Here is the sequence of actions.
If we view the oval-shaped race track as a clock, a bag enters a bucket at 6 o’clock. But first it passes over a load cell that checks its weight. If it’s outside of predetermined parameters, it gets rejected. If it’s within target weights, it moves clockwise along the oval-shaped track to the 9 o’clock position, where the following operations occur in quick succession:
• application of hot melt adhesive by a Nordson unit
• application of a tin tie that the machine cuts to the desired length from a roll
• folding of the left and right ends of the tin tie
With tin tie applied and folded, the bag continues past 12 o’clock and at about 3 o’clock it pauses in a station that folds the top flap. The bag then is pushed immediately into an elevator that takes it up through a Nita Labeling Equipment pressure-sensitive label applicator that applies a clear tape. In the hands of the consumer, this becomes a second reclosure feature, making it possible to close a bag by way of tin-tie or tape or both.
The tape is applied in one of two ways. For 12-oz bags the tape pins the top flap tightly against the back panel of the package, thus giving the package a brick-like appearance. The larger 2.5-lb bags, however, aren’t given this look. Instead, the tape is applied to the back panel in such a way that it does not pull the top flap down. The tape is still there for the consumer to use as a reclosure feature, but the finished bag retains a “cathedral-top” appearance as opposed to the brick-like appearance of the smaller bag. Zohar explains why.
“Different coffees have different densities. So if they are in the same package format, 2.5 lb of French Roast rises nearly 10 inches in that package while 2.5 lb of decaf rises only six inches high. But in the retailer’s racking unit, where there might be 10 different coffees on display, all the bags must be of a uniform height. If not, it would look odd, and consumers would be confused why 2.5 lb of one coffee looks so different than 2.5 lb of another. By keeping the cathedral-top format, every 2.5-lb bag, regardless of how much of the internal volume of the bag is occupied, has the identical height, which makes for a much nicer in-store appearance.”
By the time the bags have been elevated past the Nita tape applicator, they’re at about chest level. They’re picked from the elevator by vacuum cups mounted on a reciprocating arm and placed on a discharge conveyor leading to a station where operators place them in corrugated cases by hand.
One clever design detail worth noting is on the elevator shaft up which the bags move. A series of four small spring-loaded arms make sure the top flap remains folded over and pressed against the bag’s front panel. Without these, the top flap would not retain the folded position required by the Nita tape applicator.
Labeler a good fit
According to Nuspark General Manager Boris Motskin, the Nita pressure-sensitive labeler was a great fit for this particular application considering the space constraints that exist. Also suitable is the method of label application. The peel plate is not in line with the bag’s direction of travel. Rather, it’s perpendicular to the bag’s direction of travel. When a label is peeled from its release liner, it’s advanced to a spring-loaded vacuum pad. A small quarter-inch portion of the label protrudes from the end of this pad. As a bag is elevated up from the racetrack oval at floor level, it catches this protruding portion of the label. As the bag continues in its upward motion it pulls the label from the vacuum pad, so the label secures the top flap firmly to the rear panel of the bag. As soon as the label is affixed, the spring-loaded vacuum pad returns to its home position and waits for the next label to arrive.
“The method in which the Nita labeler operates was certainly a key to this application,” says Motskin. “Also lending a hand and working with our design engineers on this spring-loaded applicator was Packaging Machinery Concepts, the Nita distributor out of Toronto.”
Noticeable throughout the NTT-35 are a number of pneumatic components supplied by Festo. As for the PLC controller, it’s supplied by Omron, as are the four servo motors controlled by the PLC.
Also worth pointing out, says Zohar, are adjustments that had to be made to the flexible film construction from which the flat-bottom, fin-seal bags are made. “The biggest problem, which is inherent in any flexible film package, is that no two packages are exactly the same,” says Zohar. “And with a product like coffee, all kinds of conditions are in place to magnify this challenge. The grounds might settle differently from one pack to the next, and ground coffee settles differently than whole bean. Or the backflushed nitrogen might cause a slight bulge in one package that is not in the one that preceded it. These variations naturally get in the way when you are trying to automate something, in this case tin-tie application, that was previously done manually. We quickly realized that many of these issues could be resolved if we went to a heavier packaging material construction.”
Still supplied by Tadbik-CLP, the flexible film lamination now used has four layers rather than three. Aluminum foil still serves as the oxygen barrier layer, but it’s about four times thicker than before. This brings an element of rigidity that helps enormously. “It has more memory,” says Zohar. “When we crease it, it’s going to stay creased.”
Going to a more robust material also required modifications in sealant layers. “When you make these kinds of adjustments, you get a different way of conducting heat and transferring it to the different layers,” says Zohar. “CLP stuck with it in their R&D efforts, and, after about six revisions, they provided just what we needed. Naturally, the cost is slightly higher, but not significantly in view of the better handling properties we gained.” The construction arrived at, from the outside in, is an adhesive lamination of lacquer-coated polyester/foil/polyester/polyethylene heat seal.
Making important contributions upstream from the Nuspark tin-tie applicator are a number of machines, including the All-Fill Inc. auger filler that measures out coffee and drops it into a Matrix Packaging Machinery vertical form/fill/seal system. Rollstock fed into the Matrix machine passes through a Videojet thermal-transfer printer for imprint of lot and date code information, and an EPI pressure-sensitive labeler applies a label. Also integrated into the Matrix machine is a valve applicator from Plitek. The one-way valve on each package allows venting of natural CO2 build-up from the coffee while sealing out oxygen, moisture, and contaminants.
Now that tin-tie application has been automated, says Zohar, the firm plans to automate case packing and palletizing. Judging by how successful the firm was in automating its single-serve coffee capsule operations, (see pwgo.to/3242), we should expect this secondary packaging upgrade to be quite impressive.
Capsule development
Prior to bringing automation to the tin-tie application part of its business, Barrie House automated its single-serve coffee capsule operations. As that story went to press, details on the capsule itself were not available, but now that they are, we present them here because the capsule represents a notable accomplishment driven by Barrie House’s Shay Zohar and by supplier Berry Global.
While many such coffee capsules available today are either injection molded or compression molded from a polystyrene-based structure, this one is thermoformed by Berry Global from a five-layer coextrusion of polypropylene/tie/EVOH/tie/PP. Polypropylene replaces polystyrene in this composition because a key goal behind the capsule’s development was to facilitate recycling to the extent possible, and polystyrene is rarely if ever recycled. To further facilitate recycling, a pull tab on the foil lid, which is supplied by Tadbik-CLP, lets consumers easily remove lid from cup so that the foil can go into the aluminum recycle stream while the PP goes into its own recycle stream. Moreover, cartons into which Barrie House puts the capsules carry copy and a diagram instructing consumers to let the capsule cool after use, peel back the tab to separate lid from capsule, and recycle it “wherever these recyclables are accepted.”
Berry Global’s Brian Hunt, VP Sales & Marketing, says a proprietary blend of PP resins is used in the coextrusion from which the capsules are thermoformed so that the capsules will be fully capable of puncturing properly in the single-serve coffee brewing systems they go into.
“One of the reasons polystyrene has been used so much in these capsules in the past is because it is a bit more brittle than polypropylene, and thus it punctures readily,” says Hunt. “Polyproplene has a higher rubber content, so if you don’t have the right polypropylene it’s not easy to produce coffee capsules that puncture predictably and reliably. Our blend of polypropylene brings just the right puncture characteristics.”
According to Zohar, the coffee capsule now in use at Barrie House replaces one that was injection molded from a monolayer polypropylene whose pellets included an oxygen scavenger to prolong shelf life. The new capsule can be thermoformed more efficiently and at higher throughput than its injection molded predecessor. Also, it weighs 3 g instead of 6.8, and the EVOH barrier layer keeps the coffee fresher than the oxygen absorber used in the previous capsule. Shelf life is two years.