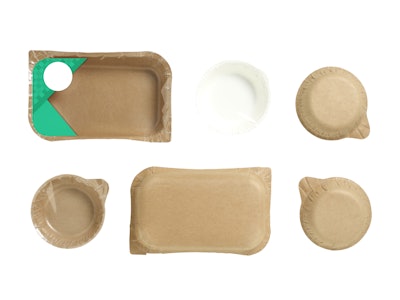
This content was written and submitted by the supplier. It has only been modified to comply with this publication’s space and style.
Syntegon is working on this project with the Fraunhofer Institute for Process Engineering and Packaging in Dresden, Colruyt Group, Strauss Group, and the University of Reading.
EIT Food is supported by the European Institute of Innovation and Technology (EIT), a body of the European Union.
The aim of the project is to pack even sensitive products with high barrier properties in more sustainable materials. Syntegon uses a special paper, which is particularly stretchable and tear-proof thanks to long cellulose fibers, thus enabling the production of sealed trays and cups with a depth of up to 30 millimeters.
A recycable barrier layer made of 95% mono-materials provides optimal product protection. The paper and the barrier layer, as well as the cover film can be easily separated, ensuring full utilization of its recyclability.
This sustainability advantage, however, also poses challenges for packaging manufacturers. On the one hand, consumers should be able to separate all components for waste sorting. On the other hand, paper and film must not be detached from each other unintenionally. To prevent this from happening, Syntegon’s TPU paper forming, filling, and sealing machine forms paper and barrier layer in a common process by thermoforming and pressing. “With the paper-based trays from the PACK4SENSE project, we have further developed our previous paper packaging solutions like the shaped paper pods – structured paper trays for the packaging of cosmetics and confectionery,” explains Matthias Klauser, project manager and sustainability expert at Syntegon.
For the PACK4SENSE trays and cups, the paper runs directly from the roll into the feeder – the barrier layer required for sealing is applied and joined to the paper without any further conversion step. Alternatively, manufacturers can use a converter to connect paper and protective layer of mono-material without heating. A forming station presses the materials into shape before the trays are filled and sealed. In addition to using a particularly stretchable paper that can withstand wrinkling during the forming process, it is important to preserve the separability of the materials: a specially adapted geometry of the forming tools reduces the tension on the materials during the manufacturing process.