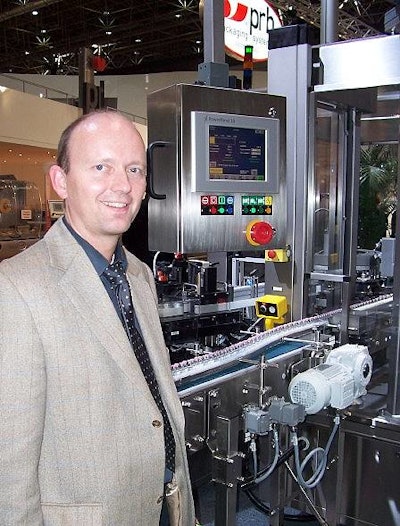
With 17 halls, 2깼 exhibitors and 176ꯠ plus visitors, it is very difficult to get a handle on interpack 2005, which convened April 21-27 in Dusseldorf, Germany. However, after talking with quite a few equipment manufacturers, both U.S. and European, as well as a number of controls companies, we found that the exhibitors were pleased, show sponsor Messe Dusseldorf (Messe Dusseldorf North America in the United States) was happy, and even the weather—for the first four days at least—cooperated. There was a lot to see and think about, including the following intelligence and insights.
The specter of China
Haunting the proceedings was frequent talk of China and its growing capacity for producing and—one day—exporting packaging machinery. And not just China. “Watch out for India, too,” said one veteran European packaging journalist.
Not everyone was convinced of China’s ability to own sizable portions of western markets for packaging machinery anytime soon. Most Chinese OEMs are still in the copycat stage, and they don’t even have that down yet.
One controls supplier observed that “walking these halls is like being at a machine tool show in the late 1970s.” Certain Chinese opportunists have no moral compunction about stealing intellectual property, he said. An end user remarked, “they will copy what they can get their hands on, but they cannot replicate controls, software and engineering.” One exhibitor said he saw a coding system built by a Chinese OEM “that looked like Frankenstein: one part Imaje, one part Markem, one part Videojet.” Wonder if the stitches showed?
China figures: A maker of coding equipment says 8ꯠ ink-jet coders are being purchased each year in China. By comparison, some 10ꯠ are sold annually in the United States.
At one press conference, a German OEM remarked, “we do not have dozens of competitors in China, we have hundreds.”
China’s first generation of packaging machines will be poor, but will improve.
Away from China…
Cavanna exhibited what it claimed was the first ultrasonic flow wrapper. Running conventional film grades, including OPP, it gives a tighter seal, says Cavanna, than flow wrappers relying on heat seal coatings.
Can esthetics sell packaging machinery?
The assumption is yes at Epipack, a 15-year-old maker of pallet wrappers that is based in Slovenia. Clad in silver ABS, their machines are sleek, curvilinear, and futuristic (see image 3). PRB, a custom end-of-line specialist based in Bologna, Italy, was also emphasizing smoothly rounded forms on some of their machines.
At Domino Amjet the talk was of laser coding replacing embossing on blister packs with much greater frequency. Laser-based printing devices are even beginning to play a role in reducing packaging materials inventory. For example, a carton can be customized on line with variable information, thus requiring fewer pre-printed materials in the warehouse. Also, RSS (Reduced Space Symbology) may be giving way to 2-D data matrix symbology. Previously, the cost of the scanners needed to read the data matrix codes was prohibitive, but that cost is coming down.
Sidel showed its SBO Universal blowmolder for PET bottles. Said to be 12% faster and capable of cutting bottle-blowing costs by 20%, the new machine is the result of three years, 60 people, and some 25 million Euros.
Cermex of France demonstrated a case packing system that incorporates vision system technology from Omron to help verify accurate case counts (see image 4).
Better, faster, cheaper, simpler: a recurring theme.
The Ezx X-ray metal detection system from Thermo Electron is a good example of this theme. It costs about twice as much as metal detection systems that don’t use x-ray technology. Heretofore, the premium has been 3 to 5 times more. A digital signal processor rather than a large industrial processor keeps costs down.
Innovations in materials included roll-fed film labels, the kind commonly used on 2- or 3-L soft drink bottles, that have peel-away promo stickers on the bottle-contact side. Or the peel-away can be a press-on tattoo for kids. They were from Ko-Pack Intl.
Also on the materials side is Peeli-Can from Germany’s Alupak. Specifically for fish that go through the retort (sardines and such), it’s an aluminum container with an easy peel aluminum lid that’s ultrasonically sealed. Alupak also developed and demonstrated a denesting/filling/sealing system for the new container. The first commercial application of Peeli-can is expected this summer in France.
A number of companies were touting integration as a core strength. Just one example was Bradman-Lake, whose booth featured a complete and fully integrated packaging line that combined equipment from two OEMs recently acquired by Bradman-Lake: Autowrappers and Europack. Autowrappers is a global supplier of flow wrap and roll wrapping machines while Europack emphasizes high-speed shrink wrappers and end-of-line packaging equipment. By adding the capabilities of Autowrappers and Europack to Bradman-Lake’s robotic top-load and automatic end-load cartoning systems, says Bradman-Lake, “a formidable new force has been created. Integration is now the benchmark for packaging line efficiency.”
Multivac showed the Serve Box for sliced cheese or sliced luncheon meat. A thermoform/fill/seal system much like others from Multivac, this one differs greatly in that the forming tools push the softened material up instead of drawing it down into a cavity. The resulting container has four corners that are open, and this is where the consumer’s fingers fit easily to remove a slice of cheese or meat without having to dive down into a thermoformed container. Also making the Serve Box system unique is that rather than a flexible film lidding being applied after evacuation and gas flushing, the lid is a rigid thermoform as well. Special materials are involved. More on that later.
Radio-frequency identification (RFID) solutions were on display, but it’s anyone’s guess just how soon some of these technologies will move from development to the implementation stage. While some at the show said it’s all hype, others were predicting widespread implementations—even on unit packs—will come much sooner than many expect. There was also talk of putting chips into bottle sidewalls or caps; this would be done during injection molding of the preform or the cap.
A special presentation, Innovationparc Bioplastics in Packaging, held more than 20 companies showing their latest innovations in the field of packaging materials made from renewable resources. An interesting statistic from exhibitor Natureworks: Its corn-based material once cost $3 per lb. Now it costs 65 to 75 cents per pound in quantities of more than 5 million lb annually. That’s right about where polyester is at today. A number of users of Natureworks materials were in the pavilion. P&G with its Nodax offering was also on hand; Nodax is in a precommercial stage, visitors were told, but P&G wanted to be on hand to learn what the global marketplace wants.
A chat with Stephan Koll, an old friend from Aventis (see image 1), the large pharmaceutical firm, made it sound like injection pens (see image 2) as a drug delivery package will grow rapidly as more conventional vials lose share. It’s all about convenience: with the pens, there’s no need to draw liquid from one vessel and then administer it. Just aim and shoot. It’s also more discreet. Yes, the pens are more expensive, but convenience will win the day.
Also held for the first time at interpack was the Virtual Packaging Engineering Forum, sponsored by MSC.Software. At the forum, sophisticated software tools for building and testing virtual prototypes by simulating motion, stress, fatigue, heat transfer, and other physical attributes of machine components and subsystems were explored.
Other observations:
In the same vein, controls suppliers are offering up function block libraries, in an attempt to get more OEMs to take the plunge into servo technology with low-cost controls solutions. In other words, “we’ve already completed a bagging machine application. We’ll use 85 percent of what we already know and only charge you for the 15 percent we need to customize especially for your machine.” This makes perfect sense and goes hand in hand with the trend cited above.
For more about interpack 2005 or 2008, use the contact information below.
Some additional insights were provided by Jim Chrzan, vice president/associate publisher.