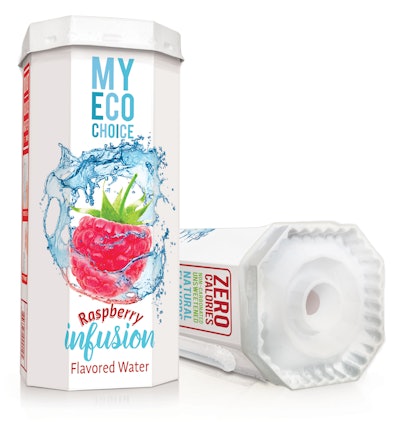
From Carlsberg to L’Oreal to Nestle Purina to Seventh Generation, the idea of a paper bottle has drawn tremendous interest from a range of Consumer Packaged Goods companies. The latest entry, from 3Epack Ltd., takes a decidedly minimalist approach. In fact, once the various components are separated, it’s remarkable just how flimsy this 3EpakR package is. But that’s the whole idea. Because in this case it's flimsiness that makes this packaging concept potentially so environmentally robust.
According to Todor Saslekov, the founder and CEO of 3Epack Ltd, three main innovations drive this development:
1. A novel structure
2. A gas-barrier film that extends shelf life
3. A prototype production line that proves methods and the production process
“The key question behind this development has always been what will make the biggest impact in terms of pollution reduction?” says Saslekov. “There are a lot of solutions out there, but once you begin to measure their global impact, you start finding flaws. To truly have a meaningful impact, we don’t need zero-pollution packaging that only a few people can use. We need packages that, even if they are imperfect, millions can use. That’s how you have an impact. And if millions are going to use such packaging, it has to be inexpensive. So we drove toward the development of a container and a technology that would minimize package cost while having the greatest possible impact on the environment.”
This bottle can be used for a range of noncarbonated beverages in volumes up to 20 oz. Saslekov claims it offers the best combination of low cost, less waste, extended shelf life, recyclability, biodegradability, and compostability. Here are the key metrics he claims:
• 75% compostable under natural conditions
• up to 75% less plastic than plastic bottles
• 75% of materials used are made from renewable resources
• Use of this package can reduce cost by up to 55%
• Materials used are 100% recyclable in standard facilities
Before plunging into the makeup of this container and the technology behind it, it’s important to elaborate a little on item number three above: the prototype production line. Like other inventors of new packaging technology whose concepts are potentially transformational, the principals of 3Epack Ltd. recognized that they had to actually launch a commercially available product to have any hope of proving that their concept was viable. The obvious facility to produce this new product was Toshitomo Co., a water bottling company in Dolnia Bania, Bulgaria, that is 40% owned by Saslekov. The firm supplies mineral water in 19-L (5-gal) reusable PET containers. Since 2018, Toshitomo is also making available MyEcoChoiceR beverages, including flavored waters and iced teas. All are in the 3Epak format, and consumers purchase them online in minimum order quantities of three 12-count shrink-wrapped units.
Container composition
So what is this unusual container made of? Not counting a straw that is automatically attached to each container, there are five parts:
• A body made of standard paperboard carton stock
• A double-wall corrugated bottom
• A top thermoformed from polystyrene
• A multilayer high-gas-barrier bag that holds the liquid
• A polyolefin shrink outer wrap
Central to the entire concept is that once the container’s contents are consumed, it’s easy to separate paper from plastic and put each component in the appropriate recycle stream. “This is where we think we have a decided advantage over aseptic drink boxes,” says Saslekov. “Aside from the use of some biodegradable glue to create a side seam on the paperboard body, we don’t bond the components together. That’s why the outer wrap plays such an important role. First, it protects the uncoated paper from water and humidity. More important, it keeps all the other components together in a strong and durable configuration that readily withstands the rigors of transportation and usage.” The package even has this message printed prominently on the paperboard sidewall: “Do not remove wrapper before drinking.”
Equally crucial in developing this paper bottle was the gas-barrier inner bag. “It took 18 months of research and development,” says Saslekov. “First, we needed a film that can hold different types of liquids—teas, juices, flavored water. It also needed oxygen barrier properties to extend product shelf life and had to be strong enough to withstand the impact of being dropped. Plus it had to be easy to puncture with a straw and be suitable for being formed, filled, and sealed on fairly standard vertical form/fill/seal equipment. The exact formula is proprietary and patent-pending, but the layers in the coextrusion are LLDPE/LLDPE/tie/EVOH/tie/LLDPE/LLDPE.”
Saslekov says the oxygen transmission rate (OTR) of this seven-layer coextrusion is 2.77 cc/m2/24 hr. He admits a typical aseptic carton comprising seven layers, one of which is aluminum foil, has a considerably better OTR of 0.2 cc compared to 2.77 cc. But not only is the cost of such a carton much higher, there’s also the difficulty of separating the layers when it comes time for recycling. As for other popular containers and their oxygen transmission rates, he lists “thick” PET bottles at about 75 cc, “thin” PET bottles commonly used for bottled water at about 350 cc, and three-layer aseptic cartons at about 850 cc.
PET bottles could be made with much better gas barrier properties, but it would require adding EVOH, and doing that couldn’t be justified from a cost perspective. “The general rule of thumb is that you need to substitute 10% of the bottle weight with EVOH,” he points out. “For a standard PET bottle weighing 22 g, you’d need 2.2 g of EVOH. Our pouch weight is only 2 g, so we only need 0.2 g of EVOH. That’s where our cost advantage comes in.”
Pleased as he is with the development of the high-gas-barrier bag material, Saslekov hastens to point out that customers who choose to use the package for water may opt for a standard PE film.
Material component suppliers could vary widely
When asked to identify the suppliers of the packaging components, Saslekov says that with the exception of the proprietary coextruded inner film, any number of suppliers can be used. One particular film producer is supplying the coextruded rollstock currently, but suppliers in Europe and the U.S. are being contacted now. Says Saslekov, “I don’t think film suppliers will be too difficult to find. The same is true for the paper bodies, the corrugated base, and the thermoformed lids. That was really one of the main goals—to eliminate the lengthy and expensive transportation of materials and components.” Saskelov adds that beverage producers who install the 3Epak system “are not required to buy our materials. But we will compete on equal footing for their components business.”
He also emphasizes this: “Remember, we are not trying to become a bottling company and excel in the consumer products business with this development. We want to sell or licence our technology to strategic partners. In the future, customers who decide to use our technology can buy their own components from whoever they like. This should reduce cost and facilitate global implementation.”
As for item number 3 above, the equipment doing the forming and filling, Saslekov says this: “The prototype line was developed by us, including the v/f/f/s machine, so that we could prove out our concept on a commercial basis and get bottles into the hands of consumers. The separate modules have been produced in different factories in China and then shipped to Bulgaria, where they were assembled and fine-tuned. But this is not a commercial line ready for prime time production. We hope to find a strategic partner with whom we can bring our technology to the next level.”
The layout of the prototype line is shown in a line drawing included in this story. The UHT pasteurizing equipment shown at the beginning is not something provided by 3EPack and is included primarily for purposes of illustration. “Many customers already have a pasteurizer, and keep in mind that those who use the package for water won’t need a pasteurizer at all,” says Saslekov.
Starts with film unwind
A quick look at the equipment in action is available here. Film is unwound into an aseptic vf/f/s system, which incorporates a “patent-pending film sterilization process.” Essentially it’s an application of a 3% hydrogen peroxide solution plus exposure to UVC light. Commonly used to decontaminate surgical instruments, UVC light has a wavelength of between 200 to 400 nanometers and is effective at killing bacteria by destroying the molecular bonds that hold their DNA together. Filled pouches move then to an assembly module that relies to a great extent on an oval-shaped track around which stainless steel molds continuously travel. These molds stop at various stations so that a number of automated processes can take place.
First, vacuum cups pick a flat paperboard body from a magazine feed, erect it, and pull it into a mold. The mold closes and moves along its oval-shaped track to a station where the two arms of a pick-and-place device alternate in picking an octagonal-shaped corrugated base and placing it into a body. The bases are delivered by way of a rotary-style hopper that separates, sorts, and feeds them into two parallel discharge lanes leading to the station where they get picked and inserted into the body. The corrugated base is supported by the bottom flaps of the body.
Now the mold moves to the next station: pouch insertion. The beverage-filled pouches are conveyed up a short incline conveyor and drop into a chute that delivers each pouch into a mold. In the next station, mechanical fingers smooth the pouch’s top corners out over the body’s edges. In the next station, the thermoformed lids—which, much like the corrugated bases, are separated, sorted, and delivered to the assembly module in two parallel lanes by a rotary-style hopper—are applied by the two arms of a pick-and-place device that also resembles the one responsible for applying corrugated bases. The lids are pressed down to firmly pinch the pouch’s corners against the paperboard body. If any process is defective, electronic sensors notify the operator and that unit is automatically ejected.
The assembled container exits the assembly module and enters a flow wrapper and shrink tunnel. Just ahead of the flow wrapper, a Markoprint X1JET digital thermal ink-jet printer from Weber Marking Systems puts date and lot code on each body. As containers exit the shrink tunnel, a wrapped straw is automatically applied to the shrink wrap.
“For more than two years we’ve been looking for a company able to produce the U-shaped biodegradable straws from PLA,” says Saslekov. “Finally we found Matrix Pack, a producer in Greece. We’re also looking for a source that can thermoform our lid from PLA. Again, we have found some who can make it. But the minimum order is currently a barrier.”
In some ways the genius of a concept like this is that multiple bets are covered where sustainability is concerned. If consumers behave responsibly, 100% of the materials in the container will be recycled. Enormously helpful on the recycling front is that the effort required to get the materials into the correct recycle stream is minimized because of the uniquely and deliberately flimsy nature of the package structure. If consumers behave less than responsibly and fail to put these packaging components into the appropriate recycle streams, 75% of the materials involved are compostable under natural conditions. Translation: 75% of the materials will NOT wind up floating in the Pacific garbage patch.
When we challenged Saslekov on just how recyclable is the seven-layer coextrusion used for the inner pouch, he said this: “Maybe in the U.S. such a plastic would not be recycled, but in many countries around the world it would be.” Even if he is wrong on that point, he emphasizes that today only about 20% of all reclyable containers are in fact recycled. So that makes the 3EPak bottle, which only contains 5 g of plastic, considerably less harmful to the environment than a typical 22.5-g PET bottle for a shelf-stable juice product. “If this package replaces only 2% of the plastic bottles sold globally today, plastic usage will be reduced by about 114,640,000 pounds per year,” says Saslekov.
So where does 3Epak stand currently? “The most important goal is to find strategic partners,” says Saslekov. “Considering that this format offers the best combination of cost, extended shelf life, recyclability, and biodegradability, we think such partners will step forward soon.”