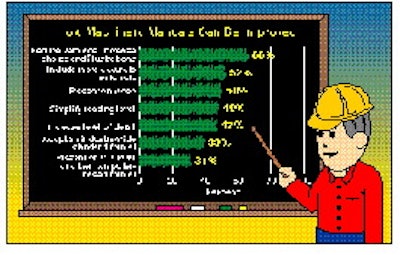
While packaging machinery and control system automation continue to advance, recent research from the Packaging Machinery Manufacturers Institute (Arlington, VA) suggests that more plant personnel need training to cope with that automation. Nearly 70% of respondents to the 1996 Packaging Productivity Trends Indicator survey said that automation in packaging lines has increased the need for higher education levels in the plant. That's almost a 10% increase over the previous year. (For details on the survey's methodology, see p. 76.)
The need for more training was greatest in the beverage industry, where 88% said more was needed. In food, 76% wanted more training, followed by 70% in beauty/cosmetics and 64% in medical/pharmaceutical. At the other end of the spectrum, only 58% of those in the chemical industry said more training was needed, followed by a mere 42% in the electronics field.
When asked which aspects of automation in packaging lines have increased the need for higher education levels, control systems and computers were listed as the two leading items by far, at 85% and 82%, respectively (Chart 1). Responses to this question were fairly con-sistent across the different industry segments, with the possible exception of the beverage industry. Almost 97% of beverage industry respondents said computers increased the need for education, with almost 87% citing control systems.
High-tech training on the rise
Several methods for conducting training were cited by packagers (Chart 2). Most popular are on-the-job training (81%) and seminars (80%), followed by hands-on workshops (66%) and conferences (54%).
Compared to all other training methods, high-tech training tools such as computer-based learning and CD-ROMs saw the biggest jump in usage compared to last year's survey. Almost 43% of respondents used computer-based learning compared to 32% the year before. And CD-ROM, while cited by only about 17% of respondents, appears to be among the fastest growing training methods, up from only 7% last year. So-called "distance learning" via television or satellite feed also increased to 6% from 2.5%, though it's still only used by a fraction of all packagers.
In the electronics industry, as one might expect, the trend toward high-tech training was exaggerated, with just over 60% using computer-based learning, almost 40% using CD-ROM and a whopping 33% using distance learning.
High-tech training was also more discernable in larger companies. Almost 60% of respondents from the largest companies in the survey (over 2ꯠ employees) used computer-based learning, versus 28% from the smallest companies (less than 100 employees). Similarly, almost 30% of the largest companies ranked CD-ROM as a training tool versus 14% for the smallest companies. For distance learning, about 19% of large companies said they used it, compared to only 4% of small companies.
This makes sense, because larger companies are more often able to include the development of custom computer-based and CD-ROM training as part of a capital project's budget. These types of training tools also scale up well for training large numbers of employees in multiple locations. For smaller companies, live instruction is usually more economical.
Better manuals demanded
Many packagers say machinery manuals should be improved: 60% in '96, compared to 56% the year before. Responses to this question were fairly consistent across the entire spectrum of packagers, regardless of industry or company size.
When asked how manuals could be improved (Chart 3), the number one response was to use fewer words, and more photos and illustrations (66%). Half of the respondents said manuals could be improved by including a training video-a clear message to machinery manufacturers that visuals are very important when it comes to training plant personnel.
Respondents also said including a CD-ROM or computer-based training aid would be helpful: 31% requested this type of training aid. Response to this item was fairly consistent across industry and company size lines, indicating that more packagers now have access to computers with CD-ROM players.
Education levels haven't budged
The thirst for more training is evident because as packaging machine automation advances, education levels in the plant have stayed the same, at least according to statistics from this and the '95 survey. Not surprisingly, most packagers (85% of respondents) say the average level of education completed by operators is high school (Chart 4). As expected, associates and undergraduate degrees are quite rare among operators, at 2% and 1%, respectively.
Education levels for management (Chart 5), as one might expect, were higher, with most types of managers having a college degree. The education level of supervisors, however, was quite evenly spread out, with 36% of respondents reporting the average supervisor education level is high school, 28% saying it's an associates degree, 34% an undergraduate degree.
Responses to this question were fairly consistent across industry lines, though interestingly, it did seem that less educated supervisors were more likely to be working at smaller companies and better educated supervisors at larger companies. Indeed, for companies with over 2ꯠ employees, a full half of supervisors had a college degree, versus 30% at companies with fewer than 100 employees.
That better educated managers seem to be employed by larger companies also seems to be true for other job titles, including department managers, purchasing managers and plant managers. But for these titles, education levels were uneven across industry lines. The most extreme example was the average education level of plant managers. While 28% of respondents as a whole said the average education level of plant managers was a post-graduate degree, the number jumped to 50% for respondents from the pharmaceutical/ medical industries. Advanced degrees were scarcest amongst plant managers in the food industry: only 17% of respondents reported them.
Training and education levels are just two of the many areas researched in the PMMI Productivity Survey. The complete Trends Indicator survey is available for $750; $375 for PMMI members.