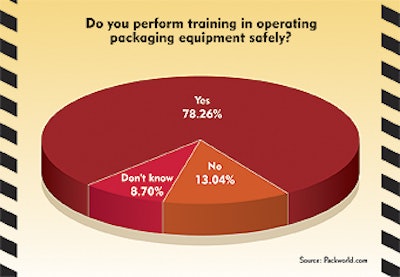
According to a recent survey conducted on Packworld.com, training in how to operate packaging equipment safely is widespread among packaging end users. Yet despite the fact that nearly 80% of 239 survey respondents indicated that equipment safety training is practiced at their companies (see Chart 1), comments from survey participants made it clear that more training in safety is still desired. (For survey methodology, see p. 34.) Some said they’d like the training directed at technicians, while others said the machine operators need it more. Still others said they don’t see any particular need to redirect their companies’ safety training, they just want to see existing programs developed more fully and formalized. As one purchasing agent at a major food company based in the Northeast put it, “I’d like to see an annual safety review with our employees on all online operating equipment.” Like the comment above, many of the recommendations about safety training were directed at the respondents’ own company management. “We should emphasize ergonomics and general workplace health and safety for packers and handlers,” said a quality assurance manager at a Southeastern furniture maker. “We should have a stronger approach toward requiring the use of safety equipment, like safety glasses for example, in the filling room,” said a maintenance engineer at a Northeastern cosmetics and personal care company. “Improved guards around laser coding machines” is another area he felt could be emphasized.
Suppliers’ responsibility Then there’s the comment from a plant manager at a medical/pharmaceutical company in the Northeast, who said he’d like to see machinery suppliers take more responsibility for safety training. His suggestion: When suppliers install machines, have them deliver not just manuals on operating, maintaining, and troubleshooting the equipment but also a safety training manual written specifically for that machine. This thought was echoed by the plant manager of an industrial products manufacturer in the Northeast, who had this to say: “Each piece of equipment we run should contain a safety handbook. Also, there should be safety signage at ‘safety aware’ points in the equipment.” Comments about ergonomics were almost as numerous as those on training. That probably explains why ergonomic features ranked so high in Chart 5, which shows that 60.82% of respondents said they are seriously considering ergonomic features on new packaging equipment purchases they plan for the next 12 months. Guarding was another subject that respondents mentioned frequently. This, for example, came from an engineer at a medical/pharmaceutical company in Canada: “All the new machines need interlocking guard door switches and emergency stops. When it’s not possible to install door switches, we want to install a light curtain or some other safety device.” Another engineer at a Southeast chemical cleanser manufacturer put his concerns about guarding this way: “All packaging machines should have OSHA-required guarding/safety features as standard equipment. The machine buyer should not have to specify them.” He wasn’t the only one to sound the OSHA note. An engineer at a nonfood consumer goods company in the Midwest is in favor of “requiring OSHA compliance for all packaging machines delivered to the plant—in other words, a letter of certification from the supplier stating that his equipment complies with all OSHA standards and that no further safety upgrades or additions are necessary.” One engineer at a large manufacturer in the Northeast had more than OSHA on the brain. He said he’d like to see his company combine the safety regs for OSHA, UL, and CE into one standard for design worldwide. He admitted that this would be a “formidable task.” But it’s clear why he’d like to see such a thing happen: “We have plants around the world and often move equipment from one plant to another,” he said. Pinch points and hot spots A number of respondents emphasized that the guarding features they wanted to see in new packaging equipment are especially important at pinch points and hot spots. Since few people know more about pinch points and hot spots than machine operators, one engineer recommended “inclusion of operators during spec writing and OEM audits.” The importance of operator involvement was mentioned by an engineer at a nonfood consumer goods firm in the Northeast, who said: “Packaging machinery suppliers should be more conscious of an operator’s range of motion while he or she is working with the machine to ensure that there are no protruding parts of the machine in that area that could potentially cause injury.” Designing machines with the operator in mind was also recommended by an engineer at a medical/pharmaceutical firm in the Midwest: “Make sure,” he wrote, “that all controls and loading stations are at a user-friendly height for all operators.” The same engineer advocated padding of areas that can cause injury if someone bumps into them. A plant manager at a food company in India had this idea on how to better educate machine builders about operator needs: “I recommend that manufacturers should visit end users and oversee their operations for a period of time to better identify areas to improve.”