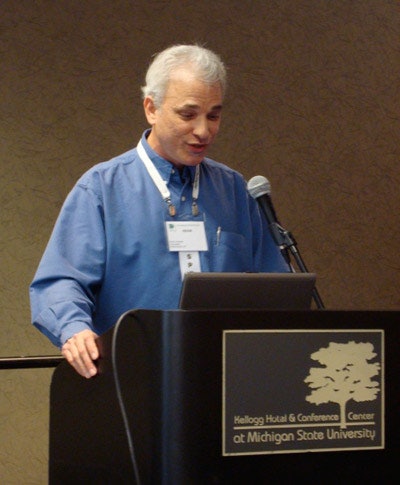
Kevin Howard
Space—or, more accurately, the elimination of space—was the topic of a sustainable packaging presentation by consultant Kevin Howard of Packnomics, LLC at a late January event held by Michigan State University’s School of Packaging. MSU’s second annual Packaging Executives Forum explored the potential economic opportunities of sustainable packaging, and Howard’s message, in “Space…The Final Frontier,” was clear: “Space costs money… minimize it!”
According to Howard, the cost of distribution logistics has more than doubled over the last several years and is now five to 10 times the cost of packaging itself. “Wasted space means excess materials, excess transport, excess handling, and excess storage,” he told the audience. “Packagers have to do more with what’s there—they have to use space more effectively.”
Typical places where surplus packaging, space, and costs can lurk, he related, include “around components, inside of boxes, on pallets, and between pallets.”
Reasonable tests = less packaging
Howard noted that excess space in packaging is often the result of inappropriate test levels, whereby packaging is designed and evaluated to withstand too rigorous of conditions. “It is vital to understand what is happening in your own environment,” he said. “Some packages that don’t pass ISTM [International Safe Transit Assn.] standards pass real-world tests and vice versa. Walk through your distribution pipeline.”
Getting rid of inefficient packaging requires that engineers design packaging “from the outside in, rather than from the inside out,” Howard said. To design from the outside in, he advised, start with the known sizing of transport modes, such as the size of the truck or sea container, and maximize densities for the longest travel. Then, maximize pallet densities for in-region loads. Finally, use the minimum package size to hold everything at the minimum cost. “Anything larger increases costs,” he noted.
To determine the minimum package size, Howard recommended the following:
• Calculate the lowest possible cost.
• Show management the cost differences between the lowest cost and the next logical size.
• Let the optimum package size determine the amount of cushioning.
• Recommend product modifications in geometry and fragility.
• Recommend better material handling methods to allow for less packaging.
Designing packaging from this perspective, Howard noted, is an important step to becoming “an un-packaging” engineer. “Redefine your job,” he advised. “Is your job to design packaging or to figure out how to get products from point A to point B at the lowest cost with acceptable levels of damage? You were hired to design packaging, but your knowledge can be extended to product design, testing, material handling, and the supply chain to contribute more.”
According to Howard, the cost of distribution logistics has more than doubled over the last several years and is now five to 10 times the cost of packaging itself. “Wasted space means excess materials, excess transport, excess handling, and excess storage,” he told the audience. “Packagers have to do more with what’s there—they have to use space more effectively.”
Typical places where surplus packaging, space, and costs can lurk, he related, include “around components, inside of boxes, on pallets, and between pallets.”
Reasonable tests = less packaging
Howard noted that excess space in packaging is often the result of inappropriate test levels, whereby packaging is designed and evaluated to withstand too rigorous of conditions. “It is vital to understand what is happening in your own environment,” he said. “Some packages that don’t pass ISTM [International Safe Transit Assn.] standards pass real-world tests and vice versa. Walk through your distribution pipeline.”
Getting rid of inefficient packaging requires that engineers design packaging “from the outside in, rather than from the inside out,” Howard said. To design from the outside in, he advised, start with the known sizing of transport modes, such as the size of the truck or sea container, and maximize densities for the longest travel. Then, maximize pallet densities for in-region loads. Finally, use the minimum package size to hold everything at the minimum cost. “Anything larger increases costs,” he noted.
To determine the minimum package size, Howard recommended the following:
• Calculate the lowest possible cost.
• Show management the cost differences between the lowest cost and the next logical size.
• Let the optimum package size determine the amount of cushioning.
• Recommend product modifications in geometry and fragility.
• Recommend better material handling methods to allow for less packaging.
Designing packaging from this perspective, Howard noted, is an important step to becoming “an un-packaging” engineer. “Redefine your job,” he advised. “Is your job to design packaging or to figure out how to get products from point A to point B at the lowest cost with acceptable levels of damage? You were hired to design packaging, but your knowledge can be extended to product design, testing, material handling, and the supply chain to contribute more.”