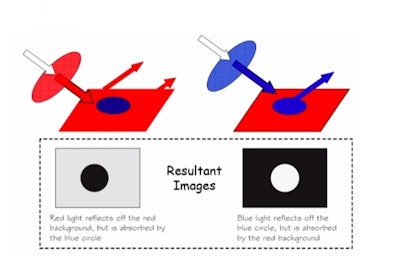
As the global manufacturing market continues to get more competitive, it is important to ensure that your factory is running at a peak level of efficiency. Any downtime due to process-related malfunctions is considered nonvalue-added downtime directly impacting company profitability.
Machine vision is an area that, if set up correctly, can reduce process inefficiencies. If your facility uses machine vision as robot guidance or inspection, there is always an area of improvement that can be investigated. Listed below are the Top Nine areas that if not set up correctly, may be causing nonvalue added downtime to your machine vision process:
Lighting techniques - Are you using the correct lighting techniques to illuminate the region of interest? Backlighting, bright field lighting, grazing, low-angle linear array, dark field, just to name a few, are the lighting techniques that are the most critical aspect of machine vision robustness. Depending on the item or package inspected, the correct lighting technique will enhance flaws or remove image noise, which will increase the efficiency and stability of your system. The intention is to select a lighting technique that will produce the maximum amount of contrast (black-to-white pixels) for the area of interest in your inspection.
[mosimage]
2) Filtering - Are you eliminating background or overhead lighting noise and other harsh environment disturbances with lens filters? By simply placing a filter on the camera lens that matches the frequency of lighting illuminating the part, ambient lighting disturbances can be removed.
3) Lenses - Do you have the correct field of view (FOV) and region of interest (ROI), including the pixel accuracy needed? The correct focal-length lens will determine the size of the region your machine vision system can see and ultimately all the information that is collected. Calculating a FOV too large will result in less detail and accuracy, whereas calculating a FOV too small may result in inspection failure due to the part or object being out of the camera sight.
4) Location - Are the parts or application tolerances too wide to repeatably detect your part?
Having a part that shifts out of the camera field of view can cause system instability. It is important to have some type of physical fixture that limits the motion of the object or part of interest.
5) Calibration - Is the system calibrated correctly, and how do you test that the calibration was and is in conformance? Having a mastering fixture or calibration routine can ensure that your system meets the quality standards of your facility.
6) Features and fiducials – In order to properly inspect an image, the identification of a unique feature that is present in every inspection image can be used as a point of reference or what we call a fiducial. It can be used to reference vision tools in your inspection or detect if you have the correct part present in your image.
7) Resolution – Resolution determines the repeatability of your system. This allows you to quantify the size of a pixel to a measurement value. Determining the resolution of your system is important because it determines how accurate and repeatable your inspection can be. Resolution can also be enhanced by the software you choose if it permits sub-pixel accuracy.
8) Stability – Another important aspect to consider when setting up a machine vision sensor is the stability of the system. It is important to ensure that the mounting of your camera system and lights does not move or shift during your process. Also, when setting up the equipment, it’s wise to place the cameras and lights in areas with little to no vibration or in areas with little traffic so that the potential for the system to get bumped or moved is minimized.
9) Testing – In order to ensure that your machine vision system is working properly, it is important to have a system that can be periodically checked to ensure that defect parts are being captured and rejected by the system. A testing procedure, perhaps using a standard sample, can be used to maximize the system's performance.
Each of the areas mentioned above are critical aspects of ensuring that machine vision will be a successful process in your facility. For expert advice and a more in-depth explanation of how each of these areas pertain to your process, please contact the machine vision department of Applied Manufacturing Technologies at 248/409-2000 or www.appliedmfg.com
Machine vision is an area that, if set up correctly, can reduce process inefficiencies. If your facility uses machine vision as robot guidance or inspection, there is always an area of improvement that can be investigated. Listed below are the Top Nine areas that if not set up correctly, may be causing nonvalue added downtime to your machine vision process:
Lighting techniques - Are you using the correct lighting techniques to illuminate the region of interest? Backlighting, bright field lighting, grazing, low-angle linear array, dark field, just to name a few, are the lighting techniques that are the most critical aspect of machine vision robustness. Depending on the item or package inspected, the correct lighting technique will enhance flaws or remove image noise, which will increase the efficiency and stability of your system. The intention is to select a lighting technique that will produce the maximum amount of contrast (black-to-white pixels) for the area of interest in your inspection.
[mosimage]
2) Filtering - Are you eliminating background or overhead lighting noise and other harsh environment disturbances with lens filters? By simply placing a filter on the camera lens that matches the frequency of lighting illuminating the part, ambient lighting disturbances can be removed.
3) Lenses - Do you have the correct field of view (FOV) and region of interest (ROI), including the pixel accuracy needed? The correct focal-length lens will determine the size of the region your machine vision system can see and ultimately all the information that is collected. Calculating a FOV too large will result in less detail and accuracy, whereas calculating a FOV too small may result in inspection failure due to the part or object being out of the camera sight.
4) Location - Are the parts or application tolerances too wide to repeatably detect your part?
Having a part that shifts out of the camera field of view can cause system instability. It is important to have some type of physical fixture that limits the motion of the object or part of interest.
5) Calibration - Is the system calibrated correctly, and how do you test that the calibration was and is in conformance? Having a mastering fixture or calibration routine can ensure that your system meets the quality standards of your facility.
6) Features and fiducials – In order to properly inspect an image, the identification of a unique feature that is present in every inspection image can be used as a point of reference or what we call a fiducial. It can be used to reference vision tools in your inspection or detect if you have the correct part present in your image.
7) Resolution – Resolution determines the repeatability of your system. This allows you to quantify the size of a pixel to a measurement value. Determining the resolution of your system is important because it determines how accurate and repeatable your inspection can be. Resolution can also be enhanced by the software you choose if it permits sub-pixel accuracy.
8) Stability – Another important aspect to consider when setting up a machine vision sensor is the stability of the system. It is important to ensure that the mounting of your camera system and lights does not move or shift during your process. Also, when setting up the equipment, it’s wise to place the cameras and lights in areas with little to no vibration or in areas with little traffic so that the potential for the system to get bumped or moved is minimized.
9) Testing – In order to ensure that your machine vision system is working properly, it is important to have a system that can be periodically checked to ensure that defect parts are being captured and rejected by the system. A testing procedure, perhaps using a standard sample, can be used to maximize the system's performance.
Each of the areas mentioned above are critical aspects of ensuring that machine vision will be a successful process in your facility. For expert advice and a more in-depth explanation of how each of these areas pertain to your process, please contact the machine vision department of Applied Manufacturing Technologies at 248/409-2000 or www.appliedmfg.com