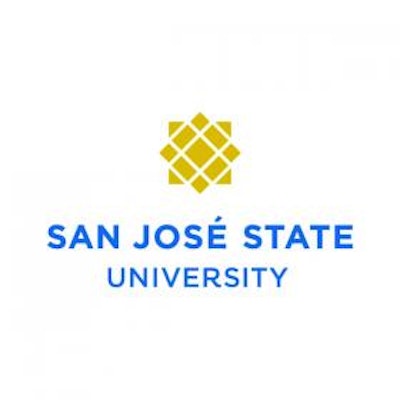
But this is simply not the case. This relatively simple concept is a good tool that all manufacturers can use to meet government regulation, to assure quality, and to reduce costs.
In the packaging space, validation comes down to package validation and process validation. Package validation is the process of providing scientific proof that the package has the desired qualities and performs its intended function. Process validation is a matter of providing scientific proof that the assembly, construction, filling, capping, coding, and other processes involved in the packaging of a product are performed correctly and reliably.
Package validation is more common across various industries, but it’s sometimes overlooked as a formal and necessary part of package design. The process begins with a listing of the required functional properties of the desired package. This list begins with understanding and stating requirements of the user, the package, and the packaging process. Package validation typically focuses on distribution testing. The shock and vibration testing to determine if a package can survive the rigors of a distribution system to transport the product to the consumer is usually the most basic analysis performed. These distribution tests can be required by the government—as in the pharmaceutical and medical device industry where ASTM test standards are utilized—or they can be developed by the firm itself. Either approach can be equally valid. In addition to these distribution simulation tests there may be other functional performance tests required of the package. The opening force of the package may be required to fall between certain force levels, for example, or the package may be used to dispense the product and may have to perform a measuring function. Each of these functional attributes should be reviewed and quantitatively evaluated to prove a level of performance. The most important aspect is that the evaluative tests must be quantifiable, repeatable, and valid when evaluating a particular feature.
Process validation is a matter of proving that the operations of filling, sealing, coding, capping, thermoforming, and labeling are done correctly and are repeatable within certain parameters. It is understood that any process has variation and that variation must be within limits for the operation to be acceptable. The formal evaluation process and documentation of that process is where the medical device and pharmaceutical industries have taken the lead in packaging validation.
The process validation begins with the Installation Qualification or (IQ) of the packaging machinery. The IQ begins with the review of the physical location and the requirements of the machinery, space, electricity, air quality, to name a few items. A key component of IQ is “system completion,” where the machine or system is reviewed to be sure all the work has been completed and documented during construction and installation.
The next step in process validation is Operational Qualification (OQ). This is the operational process evaluation to demonstrate that the machine or system operates as intended throughout various operational ranges. This requires a level of operational performance (goal) to be identified and quantitatively specified in a performance document developed before the IQ is performed. The intent is to prove that the system operates to a specific quality level in upper and lower processing limits as well as normal levels. The spread in operating parameters covers settings that may prove to generate the greatest probability of process failure.
The third leg of validation is Performance Qualification (PQ). This process examines the effect of each of the critical parameters together in an actual production run and how the variation of each parameter normally occurring in routine production affects the product under normal operating conditions. Similar to OQ, critical parameters and acceptance criteria must be defined. The completion of the PQ typically requires an examination of consecutive batches of product (typically three) to identify any change that may occur between shut-down and start-up.
The outcome of the validation is a formal report documenting the variability of the process and the reproducibility of the process. The benefit of this validation process is not only an understanding of your process, how well it performs, and where significant contributing variables to the process exist, but also an understanding of how the variables interact to influence the process.
Fritz Yambrach ([email protected]) is director of packaging at San Jose State University.