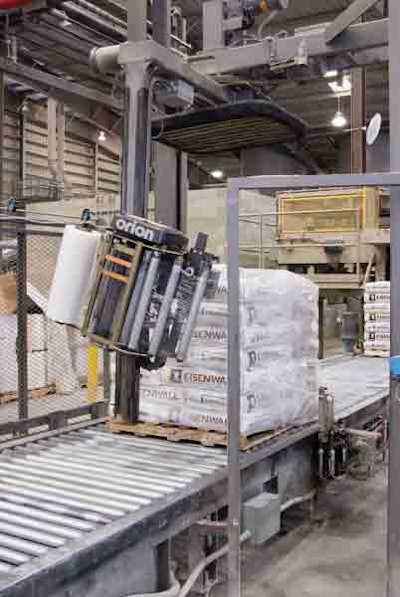
Angelus Block Co., Inc., Sun Valley, CA, is a major national, multi-location producer of bagged concrete dry mix products (including pre-blended mortars, grouts, and additive mixtures), as well as interlocking pre-formed pavement blocks, retaining walls, masonry fence systems, and glass-block products for builders, contractors, and retail outlets.
Beyond product shipment size and weight (typically about 2,500 to 4,000 lbs per pallet), Angleus Block also faces other formidable packaging challenges. A good part of the shipper pallet preparation takes place outdoors or within semi-enclosed areas, where products being palletized are exposed to weather elements such as temperature extremes, humidity fluctuations, precipitation, wind, and accompanying concrete dust. These elements potentially can threaten product quality and take a toll on packaging equipment.
Pallet-wrap problems
Until a few years ago, Angelus Block used manual stretch-wrapping procedures to secure pallets of all its bagged and block product shipments. A worker would stretch a roll of film around each pallet using a manual wrapping tool. This method was time-and labor-intensive, failing to keep up with production. And the amount of stretch film used per pallet was generally far more than necessary.
For Angelus Block, the impetus to automate was driven by four major concerns: 1) An interest in improved worker safety; 2) Retailers’ requirements that all concrete block and bagged product deliveries be stretch-wrapped; 3) A desire for faster pallet-wrapping speeds; and 4) Reduced film usage.
“Aside from the production inefficiencies of manually wrapping, the film costs were adding up,” says an Angelus Block’s project engineer and spokesperson. “If a pallet is being manually wrapped, the worker does not always know how many times he has gone around the pallet. He might go around and around 8 or 10 times and lose track of how many wraps he’s done.”
Automated wrapping
In an effort to improve pallet-wrap efficiencies, Angelus Block undertook a comprehensive study of automated stretch-wrapping options. The project engineer says, “We began an exhaustive search for automated stretch-wrapping equipment that could withstand dust and the open environment of our plants. We finally selected the MA-55 Rotary Tower Automatic Stretch-Wrapper from Orion Packaging Systems, a division of Pro Mach (www.orionpackaging.com), and distributed by Novatech Packaging Systems, Inc. (www.novatechpackaging.com). We selected the Orion machine based on its capability to handle the maximum bag and block workloads that we produce. And it is specifically built for operation in the harshest environments—including extremes of heat, cold, and dust.”
Manufactured from structural steel to accommodate heavyweight products, the Orion MA-55 stretch-wrapper features a positive airflow system in the slip ring where the electrical power transfers around its rotating tower. The positive airflow keeps out dust and other particles. The basic stretch-wrapping function only envelops the four sides of the pallet, not the top. But this wrapper also incorporates a top sheet dispenser that drapes a sheet (or sheets) of film over the top layer of the palletized bags for enhanced protection against weather elements and to deter load slippage.
As the Angelus Block project engineer explains, “Other systems have a top sheet dispenser, but outside the machine. That means you need 10 to 12 extra feet of floor space, and it slows down the process. And a top sheet placed on the pallet outside of the main machine may not fully enclose the top of the pallet or might become displaced during transit. The design of the MA-55 wrapper eliminates these concerns.”
He adds, “The machines are capable of running 20 to 24 hours per day. We installed Orion wrappers to take care of our bagged dry-mix products at our Sun Valley, CA main plant in October 2003; our Rialto, CA concrete mixing plant in January 2004; and our Rialto cement bagging plant in July 2004. We installed the same equipment for our block operations in Sun Valley in November 2003; in Orange, CA and Gardena, CA in July 2004; our Oxnard, CA plant in November 2004; and our Indio, CA plant in February 2007.”
Rewarding results
With an automated wrapper, the amount of linear low-density polyethylene film material used can be controlled, and significant money can be saved on stretch-wrap materials. The 80- to 90-gauge LLDPE cast film is supplied by distributor GL Packaging (714/385-2813). Angelus Block’s study indicated that automated stretch wrapping equipment (with a standard stretch rate up to 260%) can stretch linear film much more efficiently than manual or semi-automatic operations, and can save the company up to one-third on stretch-wrap film costs.
Angelus Block is pleased with the production speeds and cost efficiencies of the Orion wrappers, and believes its automated stretch-wrapping system sets a new benchmark for the concrete products industry.