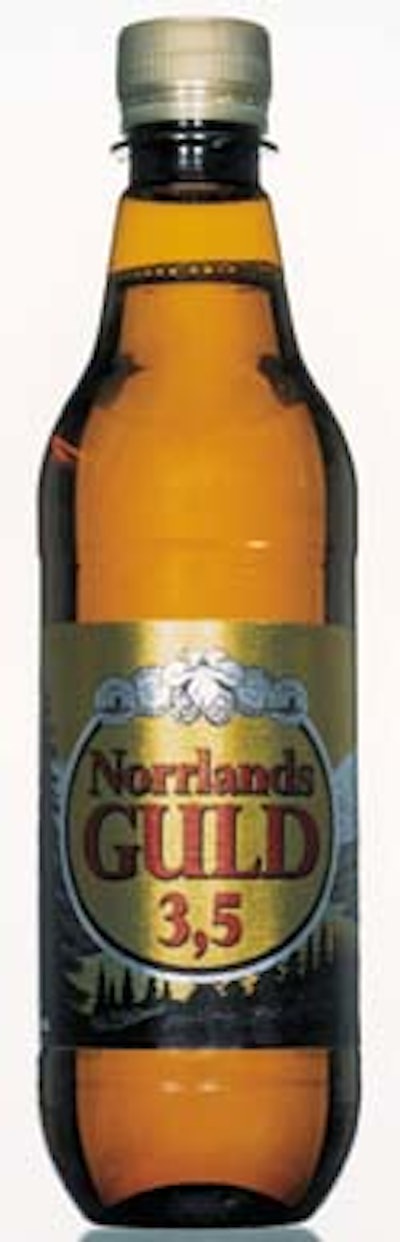
New technologies for beer in plastic are moving forward (see p. 2). Among the newsiest launches is in Sweden, where Spendrups Brewery of Stockholm last month introduced its Norrlands Guld beer in 500-mL (16.9-oz) high-barrier Glaskin™ bottles. Developed by Tetra Pak (Geneva, Switzerland), the proprietary Glaskin technology relies on a vacuum deposition process to coat the inside of blown PET bottles with a clear layer of silicon oxide. Spendrups is the first to use the technology on a commercial basis.
The bottle will be sold alongside other beers at supermarkets in Sweden. According to Spendrups corporate communications director Ulrica Franzen, the bottles will be sold individually. She says consumers will pay about 1 Swedish krona (US 11¢) more for 500mL of Norlands Guld in plastic than for 450mL in glass. She also says the company views the plastic bottle as an alternative to glass, not a replacement.
At a Feb. 17 press conference in Stockholm, Spendrup’s managing director Jens Spendrup had this to say about the new bottle.
“Tetra Pak is today able to deliver a bottle combining the lightweight, recloseable and environmental advantages of a plastic bottle with a glass bottle’s durability, taste and quality gains. We want to be able to offer a beer for every occasion without having to reduce the quality of the beer. A PET bottle is better and easier to carry than a glass bottle, both in normal circumstances and on more special occasions, such as a picnic.”
The bottle weighs 34 g empty and takes a 28-mm threaded closure that’s injection-molded of polypropylene by Germany’s Bericap, represented in the U.S. by Bericap North America (Burlington, Ontario, Canada). The Tapsid® BO 2S closure incorporates a liner that is a five-layer lamination. It includes ethylene vinyl alcohol for gas barrier and an oxygen absorber as well. Between the barrier bottle and the barrier/scavenger cap, shelf life is six months, says Franzen, the same as glass bottles.
Spendrup’s bottles are made and coated in Tetra Pak’s Darmstadt, Germany, facility and shipped to Stockholm for filling. Coating speeds, says Tetra Pak, range from 100 to 300 bottles/min on bottle sizes from 0.2 to 2 L.
The barrier material is separated from the bottle when it’s processed for recycling, which means the bottle will fit into Sweden’s well-established PET recycling system, according to Tetra Pak.
And in France
Equally busy in developing beer in plastic is Brasseries Heineken. This French subsidiary of Amsterdam-based Heineken NV is adding a 1-L size to its mix of one-way plastic beer bottles. The firm has sold its “33” Export brand in
1/2-L multilayer bottles since December ’98 (see Packaging World, December ’98, p. 38 or packworld.com/go/beer). In March, the same brand will be launched in a 1-L bottle. Once again, supermarket shoppers will be the target.
Like Brasseries Heineken’s 1/2-L bottle, and similar to the bottle used by Miller Brewing (see p. 2), the new container consists of three materials in five layers and is coinjection/stretch blow-molded by Continental PET Technologies (Florence, KY). CPT is guarded about the bottle’s precise structure, but it’s believed to include post-consumer PET, an oxygen scavenger and nylon for barrier. A glue-applied paper label wraps around the center of the bottle and decorative embossing appears on the bottle sidewall above and below the label. The bottle weighs 53 g, takes a roll-on aluminum closure and offers a six-month shelf life.
The brewer plans to replace 1-L one-way glass bottles with the new plastic bottle, though the substitution won’t be complete until the end of the year. Packaging development manager Catherine Lopez declines to comment on glass/plastic cost comparisons.
Also in March, says Lopez, Brasseries Heineken will introduce its Panach beer/lemonade drink in a five-layer, 1/2-L plastic bottle from CPT. It will be sold in supermarkets in four-pack paperboard carriers.
When asked if any of the recently developed barrier coatings for plastic bottles are being evaluated by Brasseries Heineken, Lopez indicated that the Actis™ (Amorphous Carbon Treatment on Internal Surface) process from Sidel (Norcross, GA) is being tested. This interior coating is said to provide 30 times the oxygen barrier and 7 times the CO2 barrier of conventional monolayer PET.
Meanwhile, one French brewer appears beyond the test stage with Actis. Kronenbourg, with headquarters in Strasbourg, France, expects delivery of an Actis machine some time this year. The brewer will blow its own bottles, too, also on a Sidel system. A division of the Paris-based Danone Group (known in the U.S. as Dannon), Kronenbourg is being assisted in its leap to self-manufacture of barrier PET bottles by bottled water company Evian, also a Danone division.
“We have been working in the brewing industry on [a variety] of PET solutions likely to fit as sensitive a beverage as beer with the help of the Research Centre in Evian,” Pierre Jacquesson, managing director at Kronenbourg, is quoted on Sidel’s Web site. “The Actis process can guarantee an optimal ‘best before’ date identical with the one of glass, that is, nine months. In our opinion, it best suits the use.”
The Kronenbourg move is unusual because the other purchasers of Actis machinery, including Plastipak (Plymouth, MI), have all been commercial blow molders, not beverage marketers.
On the regulatory front, Sidel planned to file for a letter of non-objection with the U.S. Food & Drug Administration this spring. The firm believes a response from FDA is possible by mid-year. In addition to developing migration and toxicological data for FDA, Sidel is also working with leaders in the recycling industry to determine the performance of Actis-coated bottles within the PET recycling stream.
In a hurry? Request more info via Web-based reader service by clicking on the reader service number.
Or you can jump right to their Web site.