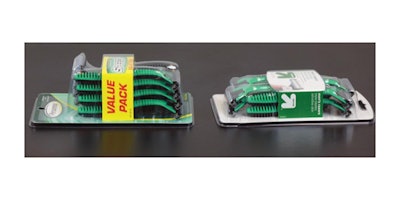
Sometimes in packaging it’s the numbers more than anything else that tell the story, and there may be no better example than the redesigned blister pack executed not long ago by Energizer Holdings. By realigning the way in which eight men’s razors are placed in their package, the Energizer team was able to go from a thermoformed cavity about 23⁄4 in deep to a cavity just 11⁄2 in deep. The savings this brought were quite impressive.
Best known perhaps as the firm behind the famous Energizer Bunny, St. Louis-based Energizer Holdings comprises 30 established consumer brands—Schick, Wilkinson Sword, Playtex, Banana Boat—that are popular in markets around the world. The firm also does a considerable amount of private-label business, and that is the part of its activities we examine here.
The eight-pack of private-label razors, manufactured by Energizer in its plant in Ciudad Obregon in the Mexican state of Sonora, faced a series of packaging challenges. Regardless of which private label ultimately markets the razors, they’re all packaged by Energizer in the same PVC blister with front and back paperboard inserts. The company was facing increased competition in the marketplace, and management knew there were packaging and supply chain opportunities to address in both materials and design. A key goal was to reduce costs associated with packaging materials and with supply chain related items such as logistics, labor, storage, and warehousing.
Knowing that a multi-faceted approach was required to solve all of these challenges and achieve real savings goals, the Energizer engineering crew and the Packaging Optimization team at Chainalytics rolled up their sleeves together.
“In addition to the cost and display consequences of excess packaging, we were also shipping a lot of air,” said Matt Bouvia, Industrial Engineer at Energizer Holdings. “The implications of packaging projects reach much farther, much deeper into the product supply chain than is often expected. The entire team, including the representatives at Chainalytics, understands just how small changes in packaging can lead to a ripple effect of cost savings across the entire supply chain. We took all of those opportunities into account when developing and considering new designs.”
Team work
The Energizer and Chainalytics team went to work modeling package design options. A three-pronged approach emerged as the solution, including a significant size reduction on the primary packaging matched by corresponding size reductions in secondary packaging (typically six-count paperboard cartons) and tertiary packaging (corrugated cases). The team
• Figured out how to align the razors in the thermoformed PVC blister in such a way that the dimensional silhouette of the finished package was reduced by 38%
• Improved nesting orientation in secondary packaging, reducing paperboard usage 55% and dimensional cube by 45%
• Increased pallet density by 86% (from 21 to 39 cases)
• Created optimal pack out arrangement in outer shipping case, reducing corrugated material usage by 35% and dimensional cube by 43%
• Improved overall shipping density per cubic foot by 61%, resulting in a more favorable LTL freight classification
• Saved more than $200,000 on expenses directly related to eight-count primary packaging in the first year
• Removed 1,635,476 sq. ft. of paper annually from the Energizer system
• Reduced freight trailer usage by 24%, removing 17,604 transportation miles from the supply chain
• Saved 2,515 gal of diesel and 56,333 lb of CO2 emissions
• Eliminated more than 1,500 physical pallet movements in the supply chain
Blister sealing equipment changed little as the project unfolded. But thermoforming of the blisters has been brought in-house. Roll-fed PVC sheet is now brought into the plant and blisters are formed on a system supplied by Zed Industries. The thermoformed blisters are stored until needed and then brought to one of several rotary-style blister pack sealing systems. On these machines, operators load empty blisters into a cavity followed by a front-facing paperboard insert, the eight razors, and the back paperboard. Once this is complete, the cavity is rotated into a sealing station where the back-facing paperboard is heat-selaed to the flange of the PVC blister.
“This project demonstrates the capabilities of packaging design to drive significant cost savings with an added environmental upside to boot,” said Bouvia. “The team, particularly the packaging experts with Chainalytics, brought deeper knowledge of packaging design, its potential, and its impact from an outside perspective and allowed us to achieve goals that we initially thought to be difficult to obtain. By incorporating expertise in shipping, supply chain, materials, and a vendor perspective, the team generated a solution that solved every concern we had, plus a few we didn’t even realize we had.”