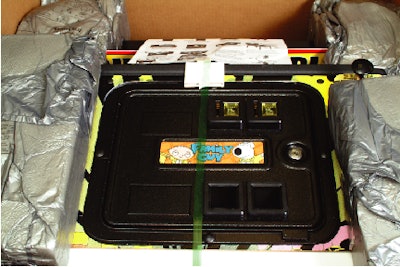
Stern Pinball of Melrose Park, IL, was having issues with aesthetic damage to its pinball machines. The corrugated shippers the company was using created scuff marks on the machines during shipment, tarnishing not only the machines but Stern’s reputation, as well. The company needed a new packaging solution to solve the scuffing problem as well as reduce packaging cost, without sacrificing protection.
So Joe Blackwell visited the Packaging Design and Development Center of Sealed Air Corp. in Hodgkins, IL. "I was impressed," says Blackwell.
The visit led to Stern’s use of Instapak® GFlex® QS foam packaging. This unique foam formulation, in conjunction with the Speedy Packer® foam-in-bag packaging system from Sealed Air (www.sealedair.com), was selected as the best solution to package a pinball machine of considerable weight and size. The high-performance foam packaging is resilient enough to hold up to the rigors of transporting a pinball machine around the world.
The SpeedyPacker foam-in-bag packaging system is designed to dispense foam-filled bags in a variety of sizes. Once dispensed from the SpeedyPacker, the foam inside the bag continues the expansion process and is placed in a simple mold to form custom-fit protective cushions. GFlex high-performance foam is specifically engineered to accommodate heavy products that require multiple impact protection during shipping. Additionally, the foam’s unique physical characteristics create high-performance cushions using minimal material, allowing for an overall reduction in package cube.
Blackwell supplied Sealed Air with a pinball machine and standard corrugated shipper for Sealed Air design engineers to use in creating a trial packaging solution. The design engineers recommended cushions on each corner of the machine because this offered the most protection with the least amount of material. Also designed were ten foam cushions that fit along opposite sides of the pinball machine.
The pinball machines were getting damaged during shipment because the detached legs of the machine went into paperboard tubes that ran the length of the machine. Vibrations during transport caused the tubes to scuff the machine. Sealed Air engineers decided to notch out two of the cushions so the legs would be held securely in place away from the body of the machine—keeping the two objects from rubbing together and ultimately preventing abrasions.
Blackwell was not concerned with the machines getting damaged from being dropped, therefore the testing process for verification focused on vibration only. Blackwell and Sealed Air packaged two separate pinball machines—one with the old package design and the other with the new package design using InstaPak foam packaging. For two hours, each package went through a random vibration test at Sealed Air’s Packaging Design and Development Center to simulate conditions a packaged product might encounter during shipment.
After both packs were tested, they were pulled from their cartons. The pinball machine packaged in corrugated had blue streaks where the paperboard tubes had rubbed the surface of the machine. After two hours, there was enough abrasion to indicate the corrugated pack would continue to abrade the machine during longer shipments.
The pinball machine packaged with Instapak foam showed no signs of abrasion. The cushions were still in good condition, and the machine looked just as it did prior to the vibration testing.
After surviving the rigors of the vibration test, the new packaging design was then tested in the field. Blackwell shipped and tracked the condition of numerous machines. None of the pinball machines received damage—convincing Blackwell that the Instapak design was successful. A group of Sealed Air representatives spent the day at Stern, teaching and assisting with the packaging process and making suggestions to help increase speed and flow. The employees experienced a more streamlined process than they had had with the corrugated package design.
An added benefit is that the new solution requires less storage space than all the corrugated materials used formerly. It’s one more reason Blackwell was so pleased by the final outcome.
"Sealed Air analyzed my needs and used a consultative approach to create the perfect packaging solution for our pinball machines," says Blackwell.