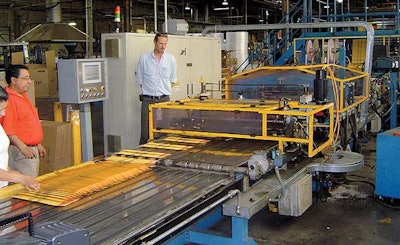
Converting equipment used by Toronto-based Polyair to make protective packaging envelopes was retrofitted recently with servo motors, drives, and an integrated motion and logic controller all supplied by the Electric Drives and Controls unit of Bosch Rexroth.
In a single pass, the converting system joins two rolls of plastic film to make air-filled cells, laminates the air-filled cell substrate to paper, and—after some folding, gluing, and cutting stations—spits out finished envelopes. Two servo motors play key roles. One is responsible for pulling the roll-fed materials through the converting process—from roll stand through laminating and cutting stations and out the discharge end. The other servo motor actuates the cutting action that separates finished envelopes from the continuous rolls.
The original drives and controls package on the system had a serious flaw in its PLC logic-timing. The servo motor pulling material through the system was badly timed relative to a brake mechanism near the material infeed station. In essence, the machine was fighting itself by pulling material through yet braking material infeed at the same time. This caused failure of expensive components, and eventually it caused Polyair to take the machine out of operation until a new controls package could be retrofitted.
Contacting the supplier of the original drives and controls package was not an option because the products were obsolete and no longer supported. Replacement was the only way to go.
Based on experience it had with other Bosch Rexroth controls components in its plants, Polyair contacted Bosch Rexroth for help on this project, too. That firm brought in systems integrator Custom Control Solutions, whose president, Dave Stuber, elected to take on the Polyair retrofit. Polyair maintenance manager Jim Boyd gives him credit for doing so. “Some integrators who looked at the problem just walked out scratching their heads,” says Boyd.
In addition to installing and programming the new controls, a communications program was recreated from scratch, and significant modifications were made to the original PLC, which remained in place on the machine. This required a systems integrator capable of handling PLC, motion, and HMI programming. Custom Control Solutions was up to the task.
The specific Bosch Rexroth components involved were a Power PC integrated motion and logic controller with SERCOS interface, two synchronous AC servo motors, and two Ecodrive03 intelligent servo drives, also with SERCOS interface.
“Bosch Rexroth has a very capable and open motion-control platform,” says Stuber. “This greatly simplified the task of linking motion control to an existing PLC.”