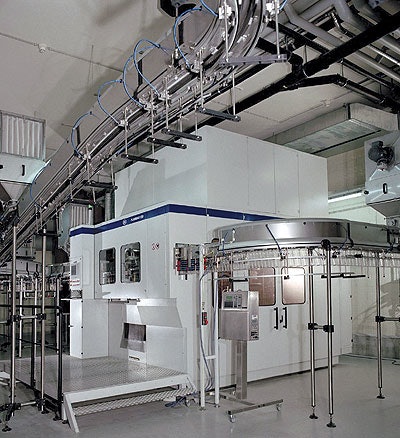
Barrier coatings continue to play a role in aseptic and ESL packaging because of their ability to keep oxygen out of plastic bottles, thus extending a product’s shelf life. While some have set aside their work in barrier coatings, others forge ahead. Sidel, for example, recently announced that one billion of its Actis-coated bottles have now been produced, filled, and sold.
Sig Holdings also remains active in the coatings game. Its Plasmax technology, developed jointly with Schott HiCotec, offers a combination of clarity, barrier, and 100% recyclability. It’s viewed so favorably at Sig headquarters in Switzerland that the firm recently spun off a separate business unit called Sig Plasmax to focus squarely on selling Plasmax installations.
The technology behind Plasmax is called Plasma Impulse Chemical Vapor Deposition (PICVD). Through a combination of microwaves and vacuum, it coats the inside of a PET bottle with a thin, transparent layer of glass. Food Contact Notification 000329, issued in July of 2003 by the U.S. Food & Drug Administration, clears Plasmax for use in food and beverage packaging in the U.S., says Sig. Also giving Plasmax a nod of approval is Petcore-PET Container Recycling Europe, a nonprofit organization that fosters the use of PET containers and facilitates PET recycling. Petcore early this year granted Plasmax a full recyclability endorsement.