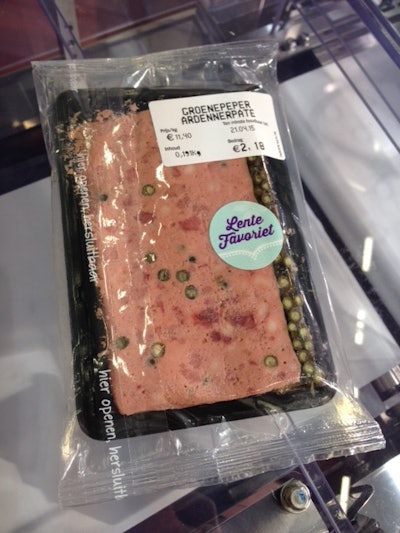
The new show, which will be focused on processing and packaging technologies serving the food and beverage marketplace, will launch in spring 2017. “The experience and recognition that Koelnmesse and Anuga bring to the table, particularly in Europe, is invaluable," says Chuck Yuska, PMMI President and CEO. Echoing this sentiment is Gerald Böse, president and CEO of Koelnmesse: "PMMI and the PACK EXPO portfolio of shows are recognized around the world as industry leaders for processing and packaging solutions, and we're eager to work with them on this exciting new venture."
Meanwhile, out in the exhibition halls of Anuga FoodTec 2015, a fascinating new concept called the Slit Machine was on display at the Fuji booth. A bit difficult to describe, it’s a new approach to modified atmosphere packaging where the finished package is easy to open and reclose. Essentially it’s a flow wrap system. A plastic tray gets product—meat, cheese, etc.—placed on it automatically and then moves through the wrapping system. Barrier film is fed from rollstock and slit in the machine direction so an “overlap” can be formed. A double-sided adhesive tape is applied, and out comes the package of pate that is shown here. Capable of being produced at speeds to 150/minute, the package is easy to open and reclose. First to install the system is Ter Beke, a Belgium-based company specializing in processed meat and ready meals that supplies Europe’s Albert Heijn chain of supermarkets.
HPP, or High Pressure Processing, created considerable buzz at Anuga FoodTec. At the Multivac booth there was talk of that firm’s 2011 partnership with UHDE, a Thyssen Krupp division that makes HPP systems. Both vacuum skin pack and MAP packs produced on Multivac machines can be sent through the UHDE system. A number of Multivac/UHDE installations around the world are up and running, but soon the first in the U.S. will go into production. Conversations at Avure and Hiperbaric, other makers of HPP systems, made it clear that food and beverage producers of all stripes are drawn to the idea of using HPP to extend the shelf life of food and beverage products without the need for preservatives.
Package shape is so crucial in achieving the differentiation that brand owners seek, and one of the most intriguing package shapes displayed at Anuga FoodTec was a three-piece steel can of tomato product marketed under the CAB brand in Nigeria. Made by Turkey’s Sarten Ambalaj, it’s filled on a system supplied by Italy’s Bonicomm, and its ring-pull steel end is seamed on by a machine from F.B.L. Food Machinery, also of Italy. If any food category’s packaging suffers from the sea of sameness syndrome, it’s the canned tomato products category. This package breaks out of the sameness syndrome in a big way.
Digital printing for labels and packaging is, according to many observers of the packaging scene, about to break through in a huge way. At Ballerstaedt’s Anuga FoodTec booth, a new capability in digital printing was attracting considerable attention. Partnering with an ink supplier and a maker of digital ink jet printing equipment, Germany’s Ballerstaedt has perfected a way of digitally printing on pre-cut aluminum lids that are sent to food manufacturers to be heat-sealed onto polypropylene cups holding anything from salad dressing to hot sauce. According to Ballerstaedt Sales Director Harry Schindler, finding UV-curable digital inks capable of withstanding heat-sealing tools without degrading was no walk in the park (which is one reason he prefers not to identify the ink supplier or the digital ink-jet press manufacturer involved in this development). But several years of persistence have paid off, and now Ballerstaedt can bring to heat-seal foil lids the short-run capability that has made digital printing so attractive to brand owners in categories like pressure-sensitive labels, flexible film, and folding cartons. Among the customers who have found this technology appealing is the Czech Republic’s Spak, a maker of own-brand as well as private label sauces and condiments. The Joghurt dressing and KFC Hot Sauce lids shown here are two examples. Spak buys its digitally printed heat-seal aluminum lids from Ballerstaedt in volumes from 10,000 to 100,000.
Elsewhere on the digital printing scene, conversation at the KHS booth tells us that KHS Innoprint technology is very close to commercialization. It’s a rotary carousel method of digitally printing directly on the sidewall of a PET bottle. In the print heads, the ink flows continuously through piezo-active channels that can be activated by electrical pulses with a frequency of up to 50,000 Hz. By narrowing these channels, drops of varying fineness from 6 to 42 picoliters can be created. The result is very sharp printing outlines. A “pinning lamp” partially dries the applied ink by way of LED UV in each printing station so that the ink won’t run during subsequent ink applications. In the last carousel, an LED UV curing unit hardens the ink and causes it to adhere tightly to the PET surface.