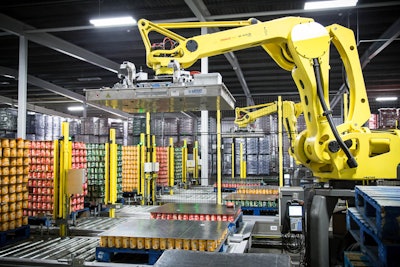
Founded in 1972, Mackle Petfoods, located in Co. Armagh, Ireland, is a family-owned company catering to family pets. With well-known brands such as Brandy, Cat Club, Jessie, Champion Professional, and Husky, Mackle is Ireland’s fastest-growing pet food manufacturer and a standard-bearer for a local, sustainable, high-quality approach to pet nutrition.
Says CEO John Mackle, “For over 40 years we’ve been using nothing but the finest natural, local ingredients to produce top-quality pet foods. At Mackle, we work closely with vets and pet nutritionists. Quality and value are at the heart of everything we do. That’s the Mackle promise, and we’re committed to keeping it.”
This commitment to quality and variety, coupled with the firm’s rapid rate of growth, has brought with it certain challenges in the packaging department. In 2011, the company began planning for a fully integrated secondary packaging facility located 10 minutes from its primary production plant to handle these challenges.
“At Mackle we deal with a huge range of products and formats, but our rigorous quality standards apply right across the board,” explains Operations Director Philip Hamilton. “When we decided to create a new secondary packaging facility in Moygashel, we needed a solution that was fully integrated and supremely flexible, striking the right balance between operational expenditure and capital expenditure and encompassing full project management. Gebo Cermex achieved that balance through the right combination of automatic and manual changeovers, and that’s why we chose them to guide this project to fruition.”
Before bringing secondary packaging capabilities to the new plant, Mackle used automated and manual packaging solutions at its production facility as well as co-packing services, depending on the production volume.
Explains Hamilton, the new plant serves several purposes: “While in the past secondary packaging’s main purpose used to be the secure transportation of the product, nowadays its goal is to enhance brand/product awareness. Thus, for us, secondary packaging has become a critical element of the product selling cycle, which we use to convey our commitment to providing local, sustainable, and high-quality nutritional food. This was one of the reasons we decided to do our own packaging. The second reason was cost efficiency. With the variety of products we manufacture, creating our own packaging proved to be the most cost-effective solution.”
The Moygashel facility is equipped to handle the wide range of products and formats the company manufactures. These include branded and own-label pet foods, and wholesale and specialty products in single cans and multipacks of three and six cans, and packs from 12 to 24 cans.
Secondary packaging formats include film only, tray and film, and pad and film combinations. Consequently, in specifying equipment for the line, Mackle was looking for a highly flexible system capable of rapid changeovers with minimal operator intervention. The company also needed the line to be able to handle conveying and shrink-wrapping of mixed product varieties.
To meet Mackle’s requirements Gebo Cermex engineers worked in close collaboration with the company to determine the optimal line configuration and to identify and integrate the best machines for the job. The resulting line features robotic depalletizing and palletizing equipment and two shrink wrappers that can handle anywhere between 15,000 and 50,000 products/hr and 25 SKU configurations, with just two to three operators.
The line begins with six pallet infeeds leading to two Depal-Vite® 4010 robotic depalletizing cells from Gebo Cermex. Each cells is equipped with a Fanuc M-410iB four-axis robot, which uses a single gripping head to handle cans, interlayers, and pallets. The depalletized cans are placed on six outfeed conveyors that merge into two rows of three lanes leading to a Gebo Cermex VersaFilm® 5S-T SFR shrink wrapper capable of producing mixed-product multipacks.
From there, another VersaFilm shrink wrapper, the 3S-T MB, handles the re-packing of multipacks (e.g., three six packs), after which a Divislat 1-2 pack diverter diverts one conveying line of shrink-wrapped multipacks into two. These conveyors carry the multipacks to two Pal Pack® 4750 layer-by-layer automatic palletizers, also from Gebo Cermex.
Among the benefits of the system cited by Hamilton are improvements in cost, productivity, and flexibility. “Cost was impacted positively,” he says. “The line features a low total cost of ownership and can be easily upgraded with newer options when the need comes along. Productivity increased due to higher product handling capability. Not only is the line able to handle a variety of current products and formats, but it is also able to handle future expansions in product formats and sizes. And, one of the main advantages of the line is flexibility, along with ergonomics, compactness, and efficiency. The new production line handles two can formats and 25 packaging configurations, including pack repacking and variety packing.
“Automation is the key to maintaining growth and competitiveness. In fact, it is the only solution to some of the most critical challenges that manufacturers face—low-speed lines, high labor costs, and long changeover times. It solves these by boosting line speed, cutting down labor costs, and shortening long changeover times.”