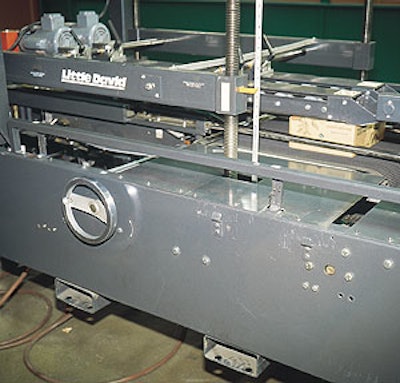
The Harry and David Div. of Medford, OR-based Bear Creek Corp. is widely regarded as the world’s leading shipper of fine fruit and vegetable gifts. The firm’s remarkable growth over the past decade has made automated packaging a must, including the method used to seal fruit-filled corrugated boxes. Automated staplers were tried, but they proved too slow. In addition, consumers are not fond of staples, and they damaged the fruit on occasion.
So case taping seemed a good option. But in seeking out an automated box taper, management knew the equipment would have to be capable of some pretty neat tricks, including these:
• It had to be portable so that it could go from one packaging shed to another, all depending on where the fruit is being harvested.
• It had to be able to seal an overfilled telescoping box.
• It had to apply top pressure to keep the telescoping lid pressed down tightly while tape is applied to the case’s leading edge, bottom, and trailing edge.
Harry and David found the case sealer it needed from Loveshaw (South Canaan, PA). Its portability is immediately apparent: Forklift pickup channels at the bottom of the machine allow it to be lifted from any of its four sides. An extra robust frame helps prevent damage during transit. According to Loveshaw engineers, it’s the first time one of their machines has been built “to go.”
Why does the telescoping box have to be overfilled? Because it’s part of a protective packaging strategy that keeps the fruit from getting bruised. Chris McGee, engineering manager at Harry and David, explains.
“There’s a foam pad in the bottom of each box and one that goes over the top of the fruit, too. Between these pads, the fruit sits in the formed pockets of a fiberboard tray. The foam pad at the top protrudes slightly over the top rim of the box, which is what we mean by ‘overfilled.’ The idea is to have the box top press down and trap the individual pieces of fruit between the two foam pads with enough pressure to keep the fruit from moving around and getting scuffed or bruised.”
With most box tapers, says McGee, it was easy enough to get the leading edge of the package taped down tightly. And the bottom of the box represented no special challenge, either. But the trailing edge would always spring up slightly in response to the pressure applied to the front.
Top compression
The Model SP3-FA machine from Loveshaw addresses this problem by compressing the telescoping lid evenly as tape is applied. First, an 18”-wide belt delivers the uncompressed box into a top-driven compression section. Here, two belts along the outer edges of the top of the box press down to keep it closed tightly. At about the same time, two side belts drive the box forward through two bottom-taping heads. Each applies tape to the bottom of the box, beginning about halfway down the leading edge of the lid, continuing across the bottom of the box, and finishing about half way up the trailing edge of the lid.
One special addition is a linear tucking device. It consists of two rods that stroke forward and push firmly against the trailing edge of each box to make sure there is no gap between the box and its lid. “These tools, combined with the constant pressure exerted on the top of the box, give us the tight, gap-free taping we asked for,” says McGee.
Thanks to a small fin attached to one of the clutch rollers in each taping head, the Loveshaw machine’s programmable logic controller “knows” whether sufficient tape has been applied. With every revolution of the clutch roller, this fin breaks a photoeye beam, and each break in the beam is recorded by the PLC. Not enough breaks in the beam means the wrong length of tape has been applied. If this happens, an alarm sounds and the machine shuts down while corrective action is taken.
Box height, length, and width can change often in a shift, so the taper is equipped with “slide-and-lock” construction for simple changeover. The tape heads slide along a linear shaft and lock into place with the turn of a ratchet handle. Similarly, a hand crank is used to adjust the height of both the top-compression and the side-drive belts. “It’s a tool-less changeover,” says McGee.
Supplied primarily by Weyerhaueuser (Federal Way, WA), most of the boxes filled at the plant are made of 175#-test B-flute corrugated. Printing is done flexo in up to three colors. Sizes range from 7.5”x7.5”x2.0 to 20”x14”x6.5”.
According to McGee, the box that runs most often measures 13.25”x10”x3.75”. But a number of other sizes have to be handled. “It all depends on which fruit we pack on any given day,” McGee says. “This is one of the keys to our box taping requirements. The taper must be easily changed over, in five minutes or less.”
So pleased was Harry and David with the first SP3-FA that it installed in ’98, it has purchased nine more—even though they barely run at all during the seven or eight months when little or no harvesting is done. Each is designed to tape 54 boxes/min and to be trouble-free in transport from one location to another.
“It’s usually more difficult to justify automated equipment purchases when use of that equipment is limited to certain seasons,” says McGee. But in this case, the benefits of the Loveshaw tapers, McGee says, made justification easy.