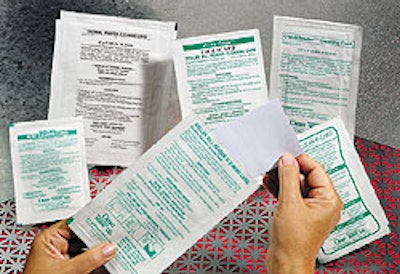
Visiting a manufacturing plant and observing interesting or unusual packaging machinery ranks among the most rewarding aspects of an editor’s job. That was the case during a recent stop at San Diego-based Clean Team Co., makers of more than 1ꯠ cleaning products, including head-cleaning cards that are inserted into magnetic stripe readers, point-of-sale credit card terminals, currency readers, and thermal printing machines. These cards are swiped through the reader device much like a credit card, except that they’re designed to remove contaminants to allow the device to continue to function efficiently.
Clean Team uses an unusual 4SS sloped-head packaging machine from Doyen Medipharm (Lakeland, FL). It’s equipped with a slitter that creates both top and bottom webs from one wide film web. The slitter is from Coast Controls (Sarasota, FL). The Doyen machine also includes a two-head pick-and-place unit supplied by MGS Machine (Maple Grove, MN). From a magazine, the machine vacuum-picks absorbent cleaning cards and places them onto the infeed conveyor of the 4SS. The machine is sloped on a 5° angle toward its discharge end. The pitch accommodates the system’s intriguing dosing system.
Each cleaning card is conveyed between the top and bottom webs, which are then heat-sealed along the two longitudinal edges/sides, and the leading cross seal. A closed-loop dispensing system pumps cleaning solution from a tank through two small tubes that deliver 2 to 6 mL of the liquid into the card-containing pack. The angled conveyor allows the alcohol solution to flow naturally as the pack is pulled downstream by end- and side-sealing rollers toward the discharge end of the machine. Before reaching the end, however, the fourth side is sealed, with a knife cutting through the seal area to also create the first seal for the next pack.
“We added the 4SS machine in early 2000,” says Dan Hastings, Clean Team’s production manager. “We pump out an average of 50ꯠ cards a day on this machine, which we run on one shift, five days a week.” Clean Team uses the new Doyen machine for about 50 product varieties, in package sizes ranging from 3 5/16” x 4 ½” to 7 1/8” x 12 ¼”.
The machine helps Clean Team meet growing product demand that its two older-generation machines couldn’t handle. The 4SS delivers several key benefits compared to the older machines, which Clean Team continues to use for “overflow” production. The advantages include:
• Quick changeovers. “We do about four changeovers a day on the machine,” says Hastings, “each of which can be done by one person in 20 to 25 minutes with simple hand adjustments.” The other machines took more than one person to change and weren’t made as quickly.
• Faster speed. “We run at an average of about 100 packs per minute,” says Hastings, “which is three times faster than the other equipment.”
• Reduced labor. “We run this machine with one person, whereas the older lines take four people,” he adds.
• Less waste. “In the past, our loss of packaging materials and product ranged from 10 to 20 percent,” Hastings estimates. “Now it’s less than two percent on a bad day.”
Delivering film and cards
The Coast Controls unit is mounted to the back end of the 4SS, on a 90° angle to the pick-and-place and sloped seal areas. Mounted to the unwind is a roll of film from Alcoa Flexible Packaging (Richmond, VA), formerly Reynolds Metals Co. The adhesive lamination includes 26# paper/7.2# low-density polyethylene/ 0.00035 foil/Surlyn® from DuPont (Wilmington, DE) sealant layer.
The preprinted material is fed to the machine from a split-and-turn unwind. The material is slit down the center to create two separate webs—one for the top of the package—the other the bottom. Web printing is registered on both sides. The webs pass over a series of turn bars. Automatic guiding and tension systems ensure consistent web control as the material moves to the sealing area of the 4SS.
Meanwhile, individual cleaning cards are automatically deposited onto a dual-pusher infeed by the MGS pick-and-place unit. The MGS uses vacuum cups powered by Piab Vacuum Products (Rockland, MA). The dual-pusher infeed comprises a series of high-density polyethylene lugs mounted to a chain that drive each equally spaced card about 10’ to the 4SS’s sloped sealing area, with each card fed between top and bottom film webs as they’re brought together prior to sealing. These lugs, or pushers, can easily be removed and replaced, in 3” intervals, to accommodate different card sizes, which speeds changeovers.
Sealing steps
The 4SS’s side-seal module includes side-seal assemblies. Each assembly grips one longitudinal edge of the continuously moving top and bottom webs. Each side-seal assembly uses a pair of heated sealing rollers to initially seal the top and bottom film webs together to create two sealed sides. A simple hand-crank adjustment on the outside of the machine allows Clean Team operators to easily move these assemblies when a product changeover is necessary for material width changes. Hastings tells Packaging World that this no-tool quick-changeover feature is one of the key benefits that led Clean Team to invest in the 4SS.
As the side-sealed material is pulled downstream, it moves to a cross-seal module that uses a twin rotary-jaw configuration. This servo-driven assembly rotates continuously, sealing at the speed of the web. Its heated jaw contacts the material from above, pressing against a similar assembly beneath the bottom web. The two assemblies use heat and pressure to create the cross seal.
This cross seal is made just before dosing. The independently controlled liquid cleaning solution is stored in a tank upstream. The closed-loop pumping system delivers the liquid cleaning solution through the two small tubes onto the absorbent card in the pack. The tubes extend to a point between the two film webs, just above the card.
The machine’s PLC signals the pumping system to dose when the card is in position under the tubes. The Allen-Bradley SLC 5/04 programmable logic controller is from Rockwell Automation (Milwaukee, WI). Once filled, the next cross seal is made, encapsulating the card within a four-side-sealed pouch. After this seal is made, a rotary crush knife cuts the four-side-sealed material, separating the pack from the web. The packs exit via a discharge conveyor for hand-packing into a corrugated shipper.
Hastings says, “Shelf life is two years, though we have cards that are still good and wet five years later. The foil, Surlyn, and paper keep the solution packed so that it does not evaporate. This is similar to a pack of hand wipes.”
Quick changeovers are key
Clean Team’s decision to add the 4SS was based on its satisfaction with its two older Doyen machines. When the company looked for a faster, less labor-intensive machine to meet its growing volume, adding another Doyen machine made sense. However, Hastings admits, “there were other machines we looked at, but the 4SS’s ability to be changed over easily and quickly was critical for us.
“We do about four changeovers a day, and each one takes about 25 minutes and can be done by hand on the machine,” he explains. “With the turn of a hand crank, I can adjust the web width for the seals. On the pick-and-place unit I only have to undo four bolts and change the magazines. Then there’s two adjustments on the PLC.
“We had no computer system with the older machines,” Hastings notes. “The Allen-Bradley computer is why it’s so easy to do changeovers. I have every product ‘recipe’ set up on the computer, including heat settings, package sizes, speeds, and sensor settings. When I want to rerun a product, I touch the correct recipe on the keypad, load it, and make the hand adjustments on the machine.”
Quick changeovers, faster speeds, and less labor add up to what Hastings estimates are savings of around $10ꯠ/month. “The machine is our lifesaver, our bread and butter,” says the energetic young production manager. “Without this machine, we’d probably need to use contract services for packaging.”
Looking to the future, Hastings believes production demands at Clean Team’s 7귔 sq’ plant will continue to elevate. To meet those expectations, he hopes “to make some additions to the 4SS.” His “wish list” includes a web printer so the company can print on demand and save costs associated with buying preprinted material. He also hopes to add two more pick-and-place heads and a unit at the discharge side of the machine that will count and stack the four-side-sealed cards. “And if our volume increases steadily, we’ll add another new 4SS machine to replace the two older units.”
That potential equipment acquisition has the makings of another winner for the Clean Team.