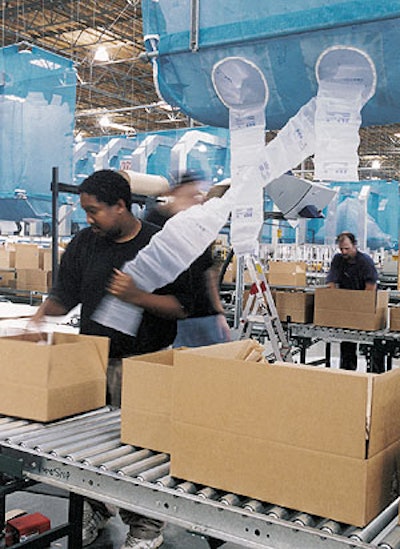
New dunnage-making equipment, conveying systems, case tapers and printers efficiently package orders at eToys’ 764ꯠ sq’ distribution center in Ontario, CA. To protect these Internet-ordered parcels during shipment, workers manually insert air-filled plastic bags into corrugated shipping cases. The bags fill voids in boxes, limiting product movement to help prevent damage.
The facility uses different sizes of the high-density polyethylene Cell-O air cushions, from 4”x8” to 8”x8”. The cushions, and the Cell-O MKII machines that fabricate them, are supplied by FP Intl. (Redwood City, CA). The portable machines are positioned near the end of the six packaging lines at the Ontario facility. The cushions are held in large blue storage bags above the lines.
Conveyor systems that carry boxes filled with customer orders to the packaging lines are provided by Rapistan Systems (Grand Rapids, MI). Later, loaded cases are taped shut on equipment from BestPack (Rancho Cucamonga, CA). Case-coding equipment comes from American Barcode Concepts (Phoenix, AZ).
The equipment was installed at the Ontario facility for its opening last June. The company started operations in 1996. According to Richard Tannenbaum, the company offers more than 125ꯠ skus on its www.etoys.com Web site. Anticipating holiday seasons, the distribution center runs 24 hours a day, seven days a week. During non-rush times, the plant runs either five or six days a week, operating either one-and-a-half or two daily shifts, he says.
At the time of Packaging World’s late-December interview, Tannenbaum was eToys’ director of fulfillment strategy. He was reportedly terminated shortly thereafter, apparently part of a 700-person layoff announced by the toy e-tailer in early January.
Order picking
For now, the company continues to ship toys, books, videos, music and other children’s products from the massive Ontario center. Products range in size from replacement kite string to swingsets, in weights from a few ounces to around 100 lb. The Ontario facility receives products packaged from manufacturers, storing them in its warehouse.
Workers try to pack one order per box, depending on the number and sizes of items in each order. Tannenbaum says that about 10 orders are typically placed on a cart and brought to each of 165 packing stations. The station operator packs those orders one at a time, selecting the appropriate box for an order from among 13 possible case sizes.
“We developed an internal, proprietary warehouse management system in which we have a digital image and information about each sku,” he says. “When a packer is packing a particular order, he or she can see the image on the screen to verify that the right item has been selected. The packer would also use a bar-code scanner to scan a UPC code on the packaged item, then choose the box size that would best fit that particular order,” Tannenbaum explains.
Upon operator activation, an Eltron thermal-transfer printer from American Barcode Concepts prints information onto a pressure-sensitive label that’s hand-applied to the box. The packer sets up the box, closing but not sealing its bottom flaps. Top flaps are left open. Products for the order are placed into the box, and the case is conveyed downstream towards final packing steps.
“The conveyor system for the packaging process is from Rapistan,” says Tannenbaum. “They really integrated the entire project for us, did all the installation and helped coordinate the project with the other vendors, making sure everything was placed properly on the line. Conveyors run from the 165 packing stations to the dunnage systems.”
Airbag advantages
The dunnage systems are positioned at the packaging lines. Each of the six lines includes large overhead storage bags that are fed with filled Cell-O air cushions produced on the MKII machines near the end of each line. Cushions are produced in a continuous web, with perforations between each Cell-O bag to allow eToys workers to separate the number of cushions they need for each case.
“The overhead storage bags are perfectly aligned directly over the conveyor, and boxes are conveyed underneath the bags,” explains Tannenbaum. “We have cut several [slots] in the bottom of the overhead bags, with strings of the [cushions] descending from each of the [slots] so that workers can pull strands of bags for each box. Some boxes may only need three or four cushions, others maybe 10 or 11. We don’t necessarily try to fill all the voids in every case. But we want to add enough cushions to adequately protect the products and minimize the rattling around of the items in the box. Workers judge how many cushions to place in each box.”
The decision to use the FP Intl. air-cushion packaging was made due to a good relationship between the vendor and eToys, says Tannenbaum. “We were using biodegradable loose-fill ‘peanuts’ from FP, and we still do,” he notes. “We use them for safety reasons, mainly for baby products, just in case a young child might get a hold of them and put them in their mouth.
“FP’s manufacturing plant is not far from our [now closed] City of Commerce facility,” he continues. “We have an excellent relationship with them, and they helped us get through our recent holiday seasons. Because of that great relationship we considered them for the air bags for our Ontario facility. The film [used to make the cushions] is shipped to us in rolls in boxes.”
Tannenbaum points out, “there are some key advantages to the air bags. First, they take up a lot less room than the biodegradable peanuts. And they take up less space than the paper dunnage that we also use (see “Dunnage options, economics” sidebar, p. 22). Another advantage is that you can print the bags, though we’ve chosen only to print small safety warnings about using the bags as a flotation device or as a child’s toy.”
Equipment benefits
Once the air cushions are added to the box, an operator closes the top case flaps and the box is conveyed into the BestPack machine, which applies tape along the bottom and top to shut the case. “We experimented with another case taping machine,” asserts Tannenbaum, “but we decided to go with the BestPack. It seals across the center of the box, both top and bottom. The taped case then continues on a conveyor to our manifesting stations.”
At those stations, operators pull the sealed boxes off the conveyor and weigh them. The box label is scanned, and the order comes up on a computer screen. The weight of the box is captured from the electronic scale. A bar-code scanner then scans the p-s label that was applied to the box during upstream order-packing. Scanning the label brings up that particular order on a computer screen. The weight is entered into the label information on the screen, along with the carrier and destination. All that information is then printed onto a p-s shipping label by an Eltron bar-code thermal-transfer printer and hand-applied to the box.
Boxes are placed onto a takeaway conveyor through what resembles an airport baggage carousel. Tannenbaum says that each of the major carriers has a truck backed up to a shipping dock at the facility. The driver uses the box shipping label to identify cases destined for shipment by his or her company. Those packages are loaded onto the truck for direct-to-consumer delivery.
“When you’re buying online from an Internet company like eToys, the dunnage that’s used is important,” Tannenbaum relates. “The air cushions have a ‘hi-tech’ appeal and look more advanced than the old, traditional ‘peanut.’ That look is helpful to us from a branding perspective. Everything we do is focused on the children and parents buying our products. We’re trying to be their ally, even when it comes to packaging.”