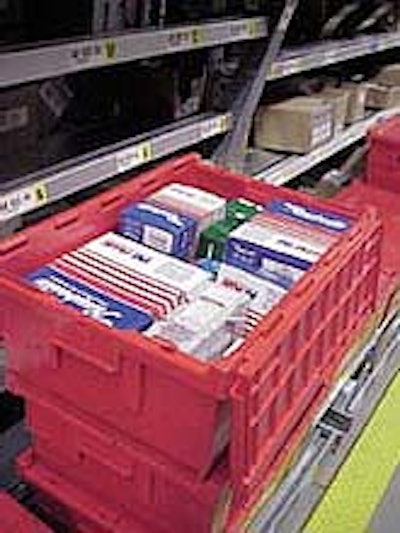
Pep Boys, Philadelphia, PA, a retail and service chain serving the automotive aftermarket, has changed its footprint. No, not that of Manny, Moe or Jack, the company’s character icons, but of the returnable totes used at the company’s new distribution center (DC) in Chester, NY.
When opening the DC last October, Pep Boys opted for new sizes and a different type of reusable totes. The company standardized on the FlapNest™ Series totes from IPL Products (Northborough, MA) for its Chester DC. The 24’’x16’’ footprint containers are designed to optimize the space of a standard 48’’x40’’ GMA pallet. Five totes fill out a pallet layer. Pep Boys uses two heights of these totes, 14’’ and 9 ½’’, the smaller one used for more dense products. Two colors, gray and red, distinguish the two sizes of totes, both imprinted with the Pep Boys logo.
“They contain the merchandize from the DC to the store, and are then used to return merchandise from the store back to the DC. They get pretty roughed up during distribution,” explains David Schneider, director of engineering and logistics.
At the DC, workers pick packaged products from shelves and place them into the totes as they are pushed along on a gravity-flow roller conveyor. After loading, totes are palletized and shipped to the particular Pep Boys store. The Chester DC services company stores in the Northeast.
The FlapNest totes replace a single-sized tote that the DC used before. “A one-size-fits-all approach doesn’t work with our wide variety of products,” says Schneider. He says items packed into totes are from among 36ꯠ different items, ranging in size from small bags of springs to fiberboard containers for 22’’-long shock absorbers.
Tote options
“For example, our air filters take up a lot of space while spark plugs do not,” explains Schneider, “yet spark plugs are dense. Workers would maximize a tote by filling it up, and when a large tote is filled to capacity with dense products, it’s too heavy to lift easily.” Thus the option of using either a larger and smaller tote works great. He says the average cost for the two sizes of totes is less than that of the previous tote.
“Also, we have better cube utilization onto pallets with these totes,” Schneider points out. “The previous ones were not sized for a pallet.”
The former totes often overhung the pallet and were prone to damage during distribution, especially during fork truck transfer, Schneider says: “Those would end up getting cracked and crushed.”
Schneider estimates Pep Boys typically restocks from 8ꯠ to 10ꯠ totes yearly at each DC (the company has six others throughout the U.S.) He points out that the attrition rate isn’t entirely due to damage: some are used to store inventory, or paperwork, and some are simply given away to customers who “love our totes.” Nonetheless, “We’re hoping with the FlapNest totes that we don’t have that kind of replacement rate,” he says.
Although he can’t quantify damage reduction attributable to using the new totes, he says “I don’t see a pile of damaged totes when I walk through the Chester DC as I do in the others.” Pep Boys’ contract for the totes calls for 45ꯠ FlapNests.
The totes used by Pep Boys are molded of high-density polyethylene, although depending on resin pricing, IPL has also molded FlapNest totes of polypropylene for other users. Schneider likes the 1/8’’ thick molded sidewalls.
“The totes we used before were more brittle, but these seem more ductile, so they flex rather than crack,” says Schneider. “They seem to take more abuse.”
The opening mechanism is also different. “With the previously used brand, a wire hinge had to be pulled off to replace the lid,” he explains, “and broken lids would render those totes unusable. If a FlapNest top needs replacement, the old one is simply popped off and the new one is popped on. It is that easy to repair.” The all-plastic construction also makes the containers transparent to metal detectors.
The totes’ ease of use begins when the DC receives a shipment of them. Schneider points out that, rather than fully nest, the totes “telescope” inside one another, which makes denesting a cinch. The previous totes had nested so tightly it made removal difficult, he adds.
Schneider says the change has been relatively transparent to DC workers, but that stockers at stores noticed the difference: “They like the different tote sizes,” he relates, “and have noted how they seem to pack better on the pallets.”
His plan is to use the FlapNests in the future at the six other Pep Boys DCs.