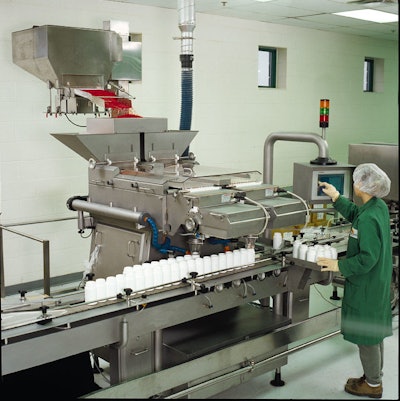
A brand new filling line anchored by an electronic tablet counter is among the recent developments at the Windsor, Ontario, facility of Toronto-based Jamieson Laboratories.
Jamieson is the largest manufacturer and marketer of vitamins and nutritional supplements in Canada. Installed in April, the new equipment replaces an older line that included a slat counter rather than an electronic counter. The new tablet counter has added a welcome measure of flexibility to Jamieson’s manufacturing process.
“We looked at both slat and electronic counters, and we quickly realized that because we do so many different tablets and capsules, the electronic counter would suit us better,” says facility manager Ken Cook. “Slat counters would require a new set of slats for each different tablet. I know some companies that carry as much as a million and a half dollars in slats just to handle all their tablet varieties. An electronic counter, on the other hand, doesn’t require those parts, nor do you have to spend time changing or cleaning them.”
Available for about the last 10 years, electronic counters rely on scanners to count each tablet as it drops from a multichannel vibratory pan. When the appropriate number has dropped from the pan into a chute, additional tablets are blocked from the chute until it discharges its load of tablets. As this takes place, counting continues unabated. As soon as the chute is empty, the next load of tablets is allowed in.
Slat counters operate differently. The number of slats on a machine varies, but each slat has channels designed to fit a specific tablet shape. When a slat reaches a tablet-filled hopper, its channels are flooded with tablets while a brush prevents more than one tablet from occupying a channel. Then the slat carries its tablets to a discharge section, where tablets fall out and down a chute to the waiting bottle.
Packaging lines dedicated to one or two tablet varieties generally lend themselves to slat counters for two reasons: Speeds are high and, with only two sets of slats, investment in change parts is minimal.
Electronic counters are typically favored when a wide variety of tablet shapes have to be packaged, which is precisely the case at Jamieson. “We have about 25 different shapes to contend with,” says Cook. “That used to mean a lot of time changing slats.”
Changeovers used to take two hours if product-contact parts had to be cleaned. Now they take as little as five minutes and never more than an hour.
Made in Holland
The electronic tablet counter selected by Cook is a Model CF-1220 machine made in the Netherlands by Cremer. NJM/CLI (Lebanon, NH) represents Cremer in North America.
Among the machine’s virtues, says Cook, is its ability to operate in a relatively dusty environment. This is important because the large vitamin C tablets Jamieson makes create a lot of dust when packaged. According to Cook, the machine’s electronic counting sensors are set back in a way that prevents dust from clogging them. “For a large bottle and a dusty product, this machine has proven itself most efficient,” says Cook.
Bottles per minute was an important criterion, too, as Jamieson searched for its new filler. The Cremer machine, notes Cook, does not disappoint. The bottle filled most frequently on the new line is a 120-count container of large chewable vitamin C tablets that are 5/8” in diameter. This container is filled at 52 bottles/min.
Cook says a higher speed is prevented by the size of the neck finish. “There’s only a 31-millimeter opening to get those tablets through,” says Cook. “Fortunately, there’s a vibratory funnel that gently forces the tablets in the container without breaking them. It’s a great feature.”
Unscrambling is first
Bottles filled on Jamieson’s new line are either high-density polyethylene (primarily for contract customers) or polyethylene terephthalate (see sidebar, p. 34). They enter the line by way of an unscrambler supplied by Pace (Fairfield, NJ). As bottles reach the tabletop conveyor that carries them through electronic filling, a diverter sends them down one side or the other of a lane divider. This permits the Cremer to fill two-up.
The smallest bottle filled on the line has an internal volume of 60 cc, the largest 375. Products include gelcaps, tablets and two-piece capsules. All product is fed into the line through a bulk bin that holds the contents of seven 20-L pails. Once this hopper is full, an operator hits a switch to elevate the hopper up to two overhead hoppers that feed directly into the Cremer machine. Cook says the floor-level bin is a welcome improvement over the method used on the old line. “It’s nice not having to run up and down manually filling an overhead hopper,” he says.
Each side of the twin-fill Cremer machine has three 12-channel vibrating pans. As tablets drop from the hopper into the first pan, they’re essentially in a bulk flow. By the time they’re vibrated to the second pan, they begin to separate from each other. By the third pan, the tablets are neatly aligned end to end in their channels. All that remains is for the tablet to be counted as it drops out of its channel and passes the counting sensor.
“Once the correct number of tablets has been counted into the delivery chute, memory flaps are shut above the chute so that the product for the next bottle can begin being counted immediately,” says Cook.
Exiting the filler, bottles are conveyed to a cottoner and then a capper, both from NJM/CLI. Each cap has a foil liner that’s induction-sealed, shortly after the capper, by an Enercon (Menomonee Falls, WI) system. “It produces a nice, clean seal, and it’s easy to run,” says Cook.
A surge table after the induction sealer allows time for a label roll change downstream without having to shut down the filler. Then bottles enter a retorquer, also supplied by NJM/CLI.
Labeling a challenge
Next is labeling, done on a Model 510E pressure-sensitive system from NJM/CLI. Round bottles are a snap, says Cook, but most of the bottles Jamieson runs on the line are squared-off PET. These are more challenging to handle because what’s applied is almost like a five-panel label, Cook says. The labeler accomplishes its task with the aid of starwheels that help wipe down the two trailing flaps as the bottle passes.
The final piece of equipment in the line is a Model RALS L-sealer from RBS (Toronto, Ontario, Canada). Its automatic swing gate channels the single row of incoming bottles into three lanes. At the end of these lanes is a mechanical stop that halts bottles after the six bottles have passed. These six are then pushed at a right angle through clear shrink film and, subsequently, through a shrink tunnel. The unsupported bundles are then case packed or palletized by hand.
Cook says the flexibility of the new line has been especially helpful in meeting requests by Jamieson marketers for new products. “With the slat counter, we just didn’t have the flexibility to quickly add a new tablet size to our mix because we had to wait for slats to be made,” says Cook. “With the electronic counter, we punch in the parameters of the new item and run it.”
Gratifying as the whole project has been, says Cook, his work is not over yet. Additional packaging upgrades are now on the drawing boards. “It’s all about being efficient and looking for opportunities to be better at what we’re doing.”