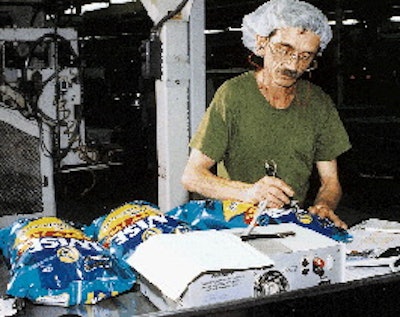
Four and a half million lb. That's how many potatoes Wise Foods Inc. processes at its plant in Berwick, PA, each week. And once they're cleaned, peeled, sliced, fried and flavored, if there are glitches at the packaging machine, Wise could end up with a lot of chips on the floor.
Two years ago, Wise was having problems at its packaging machines. The packaging material performed erratically on the forming tubes of the 33 vertical form/fill/seal machines running at the company. To solve the problem, Wise teamed up with the Films Div. of Mobil Chemical Co. (Pittsford, NY) and converter Bryce LLC (Memphis, TN) to design a new film with better machinability.
The film they came up with is an extrusion lamination of two 70-ga three-layer structures. The outside structure is a clear three-layer coextrusion of heat-sealant/oriented polypropylene/skin layer corona-treated for ink laydown. Bryce reverse-prints this material on a flexo press in up to eight colors. Then, in a separate operation, Bryce uses polyethylene to extrusion laminate that three-layer structure to a 70-ga Metallyte BSM-2 from Mobil. New from Mobil, the BSM-2 is a three-layer adhesive lamination consisting of an OPP core with a metallized film on one side and a sealant layer on the other. The metallized layer gets buried when the BSM-2 is laminated to the three-layer coextrusion.
The material formerly used was similar in construction, but the sealant layer on the inside of the bag had poor slip characteristics. On the vf/f/s machines, this sealant layer comes in direct contact with the forming tube as the draw-down belts press the film against the tube. As the tube grows warm from the friction, the heat-seal layer would react to the heat, thus causing the film to stick to the tube.
The superb slip characteristics of the sealant layer in the Metallyte BSM-2 allow the new bag material to slide smoothly over the forming collar and tubes of the Hayssen (Duncan, SC), a subsidiary of Barry-Wehmiller Co., bagging machines. But the sealant still offers good hot tack and seal integrity over a wide range of temperatures.
Converting 1.5 million lb
Wise began using the new bag material in 1997. This year, Bryce will convert nearly 1.5 million lb of film for the snack food company. According to Bryce technical director Michael Williams, the Metallyte BSM-2 brings benefits not only to Wise's bag-filling operation but also to Bryce's converting operation.
"It's a robust film that we can run on all of our extrusion-lamination machines with consistent performance," says Williams. He especially appreciates the way it resists "crazing," or the tendency for metallization to fracture and be picked off of the film when it's handled at high speeds. "The consistency of the material has helped us move away from dealing with film issues and concentrate on improving production processes," he says.
According to all involved, the development of Metallyte BSM-2 grew out of a true team effort.
"We brought the group together and first got our questions out on the table to pinpoint what exactly we were trying to accomplish," says Williams. "This effort proved to be positive since it allowed all of us to work toward the same goal."
After the team established the product requirements, technicians at the Mobil Technical Center in Macedon, NY, were off and running. They developed samples and sent them to Wise and Bryce for testing and screening. "We were always in communication with each other," says Jim Williams, packaging specialist at Wise. "During testing, we talked to each other to find out how things were working. It was a valuable learning process in how to work successfully together."
And working together paid off for all involved. "We solved a lot of problems by changing [to the new film]," says Jim Williams. "Our packaging machines run thirty to one hundred and twenty bags per minute, and we need a film that runs without a lot of adjustments. The BSM-2 film is a forgiving material that runs at different temperatures and has excellent sealability and coefficient of friction."
Best of all, it helps keep those 4.5 million lb of potatoes moving smoothly and profitably each week through Wise's plant.