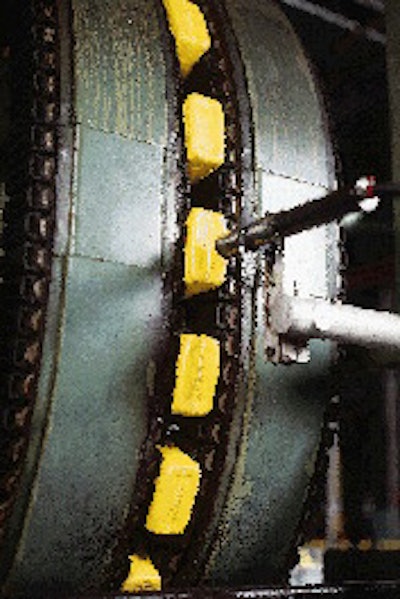
For Pennzoil Products Co., Houston, TX, the small-character ink-jet coders on its various packaging lines are just as crucial as the largest filler.
"We can't run without the ink-jet coders," says Jim LeSaicherre, project manager for Pennzoil's operations support group at the company's Houston corporate headquarters. "We have to code every single bottle that goes through our filling line, so it's critical equipment for us."
The units apply production codes to the bottoms of high-density polyethylene bottles containing 1 qt of motor oil or other automotive chemicals.
After Pennzoil felt it had squeezed the last life out of its first-generation ink-jet coders purchased in 1984, it sought replacements. At Pack Expo 96, LeSaicherre was impressed after he spotted the model 460Si small-character coder from Willett America (Fort Worth, TX).
"What sold me on the Willett was the overall ease of operation. It offered easy refill of the fluids, virtually no handling of the ink or solvent, and appeared to be easy to maintain." LeSaicherre adds that the price was comparable to other coders on the market.
Tried and true
After testing a unit in Pennzoil's Shreveport, LA, plant shortly after the show, the company began rolling out the coders to the rest of its plants over the ensuing months. "Maintenance-wise it's worked out fantastic," says LeSaicherre.
Typical was the experience of its Rouseville, PA, plant, which replaced two of its aging coders with two 460Si units in January '98. There, the units have reduced ink-jet coder maintenance by at least 50%.
The most visible benefit: single-button shutdown and startup. "When you shut it down, it goes through its own purge cycle and flushes the heads itself, cleans itself and completely shuts itself down," says LeSaicherre.
The old coders required a vigorous and messy cleaning with solvent to flush out stale ink, which then had to be treated as a hazardous waste. Since the new coders don't generate that waste when they clean themselves automatically, LeSaicherre says across all plants, the new coders have sharply reduced such hazardous waste, by at least 80%.
Start-up, too, is similarly easy. "On start-up, it's basically a one-button show," reports LeSaicherre. "We've had operators come in after a three-day weekend, hit the start button and it just fires up."
Refilling the unit with ink is also a trouble-free process and can be done while the unit is running, according to Ron Campbell, the Rouseville, PA, plant's maintenance supervisor. When the unit flashes a warning light indicating that fluids are low, the operator simply lifts the lid and replaces either of two bottles-one for the ink, and the other for what Willett calls top-up solvent. (The top-up solvent mixes with the ink to maintain the proper viscosity at whatever the current ambient temperature is, as measured by the units' built-in temperature sensors.)
"The bottles are designed so you can't mistake putting one into the opening meant for the other," says Campbell. He confirms that the ink never touches the operator's hands. The entire refill process takes about three minutes. And the new coders need their fluids replenished "a lot less frequently" than the previous coders, according to Campbell, due to what Willett says is efficiency of the ink system.
Another benefit of the coders is reliable operation regardless of ambient temperature. The coders continually monitor and adjust the temperature and viscosity of the ink regardless of ambient temperature or whether the equipment is started cold or has been running all shift. According to Willett, maintaining the proper viscosity and temperature of the ink is an important part of reliable ink-jet printing reliability.
Routine maintenance is easier on the new coder because the unit's built-in electronics tracks the coder's hours of operation and manages its own maintenance schedule by informing operators when service needs to be performed, such as a filter replacement. "There are little icons on the LCD readout that tell you what it needs," says Terry Boocks, plant technician.
Remote diagnostics
A feature that Pennzoil has yet to take advantage of is a built-in modem that allows remote diagnostics by Willett technicians. "We haven't really used it yet," concedes LeSaicherre, "but it's there if we need it. Willett can dial in and troubleshoot the programming on the machine should we run into any glitches." The Rouseville plant also likes the modem capability but confirms it hasn't used the feature yet.
Unlike Pennzoil's old coders, the new ones require only AC power. Pennzoil's previous coders were pneumatically operated, requiring "clean, dry air," says Boocks. "We [often] had trouble with our air compressors, dryers and had subsequent problems with the coders."
And, like any modern coder, the built-in memory is a great convenience. "Everything that we run on these lines is programmed into it," says Campbell. "So all the operator has to do is push the keypad, and it will bring up what he wants to print. And then he just pushes go." The old coders required operators to re-enter the codes each time they wanted to make a change.
Like many of Pennzoil's plants, the bottling lines at Rouseville begin with bulk-bottle depalletizers that deliver bottles to a cable-track lowerator from Crown Simplimatic (Lynchburg, VA). The tracks capture bottles from the sides, exposing the bottoms, carrying them in a sideways arc until they're at the height of the rest of the packaging line. On each lowerator, the printhead is actually mounted sideways right at the point where bottles are tipped 90°, thus giving each coder access to the bottom of the bottle. The code that's applied is a production code that indicates plant, line, date, time and SKU.
At Rouseville, typical line speeds are 240 bottles/min, though LeSaicherre says some Pennzoil plants using the coders run at speeds as high as 350 bottles/min. After empty bottles are coded, they continue on to downstream filling and packaging operations. Though eight of the nine Willett units installed to date have worked flawlessly, the Rouseville plant actually had an opportunity to test Willett's service and support when it experienced trouble with one particular coder when it was first installed.
"I called and asked for a service person, and he was here the next morning," says Campbell. After some attempts to get the coder to work properly, Willett ultimately supplied a replacement unit. "They were very good about it," Campbell says. Agrees LeSaicherre: "They stood behind their unit." In addition to valuing Willett's support, LeSaicherre, Campbell and Boocks also spoke highly of the supplier's training.
For his part, LeSaicherre plans to continue buying Willett coders to replace the aging ones in Pennzoil's plants. No wonder. Rouseville's new coders continue to work without clogging, leaking or malfunctioning, reports Campbell.
"We usually run two shifts a day, five days a week, sixteen hours a day," says Campbell. "I've had virtually no trouble with them at all since I've installed them," he says. "They seem to run practically trouble-free."