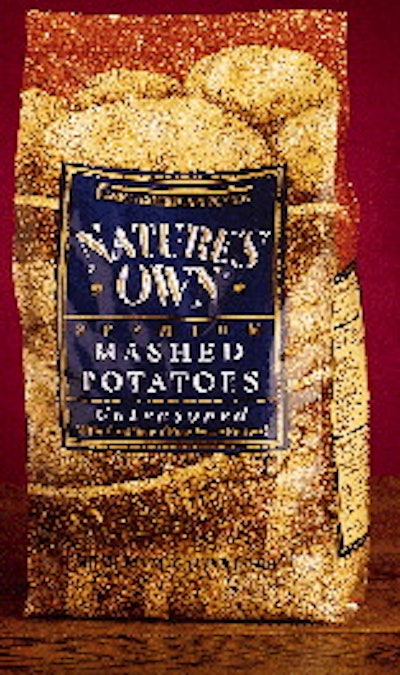
Bags of Nature's Own(TM) dehydrated potatoes may not rival the masterpieces of artist Georges Seurat. But the bag graphics do echo Seurat's pointillistic methods, the end result being a package that would stand out on any store shelf. That's why it's surprising to learn that these potatoes, marketed by Basic AmericanFoods of Walnut Creek, CA, are exclusively sold to foodservice accounts.
To be certain, the points of color that adorn the bag's background of whole russet potatoes are eye-catching. More distinctive, though, are the stand-up bag's four "pleated" edges that many may recognize as the Stabilo Bag(TM) made on a machine from Rovema (Lawrenceville, GA). Rovema confirms that Walnut Creek, CA-based Basic American Foods is the first U.S. user of the Stabilo bag for foodservice. Nestlé Chocolate & Confections was first in the U.S. to use the bag for a retail product last August, with its introduction of Pretzel Flipz(TM) (see Packaging World, Sept. '97, p. 2).
The 1.75-lb foodservice bags are made on Rovema's continuous-motion Model VPR-320 vertical bagger, at Basic's Blackfoot, ID, facility. The machine was added last summer to launch the Nature's Own seasoned and unseasoned dehydrated mashed potatoes.
Other products are also under consideration for packaging in the Stabilo bag, according to the company. Basic American Foods dehydrates vegetables, mainly potatoes and beans, for foodservice customers. Basic also supplies the products in bulk to processors as ingredients.
"This is a new brand and [to introduce it] we chose the Stabilo bag. It has a distinctive appearance, with four sealed vertical edges and a gable-like top," notes Larry Parks, section leader in packaging engineering at the Blackfoot plant. "First, we feel it's a functional and attractive bag. In our [foodservice and institutional] markets, that's very important," he points out. "We've done considerable customer testing, and we've learned that they really want an all-around quality package. Like a consumer at a grocery store, if a customer, say a chef, sees this bag, its form and graphics will communicate that there's a quality product inside."
The focus on this package stems from Basic's top management, which views graphics as more than merely cosmetic. "There is a growing need to provide [customers], food preparers and waitstaff with more information," says Gordon Lewis, vp of new business development. "One means to do this is to use packaging graphics to better differentiate product quality and usage applications."
Designed along with SBG Partners (San Francisco, CA), the bags for delicately seasoned and unseasoned potatoes are nearly the same, with the exception of certain graphic elements. The unseasoned version features blue-colored rectangular blocks for front, back and side panel copy while green is used for the seasoned variety. Detailed preparation instructions for hand or machine mixing, as well as recipe suggestions, are printed on a large back panel.
Basic American Foods selected the Stabilo bag for more than artistic merit, however. "The package was designed to be easy to handle, stack well, provide strong product identity and minimize packaging waste," says Lewis.
Parks says that the Stabilo bag "uses about ten percent more material than a standard flat-bottom stand-up bag." However, he believes it is worth the extra cost "because of its design and strength advantages, and the results we think it will give us in the market." He says that Basic's handling, compression and transportation testing proved that the unusual edges give the bag "quite a bit of additional strength compared with other flat-bottom stand-up bags.
"The package is also a waste reducer, which is very important in this industry," adds Parks. "We used to pack a flat bag with dehydrated potatoes that took a lot more corrugated [protection]. We packed eight of these flat bags into an outer corrugated shipping case. The Stabilo package is much more economical for us from a secondary packaging standpoint and for shipping. We package nine Stabilo bags in a corrugated tray, then shrink wrap it in film." Basic wouldn't quantify the cost savings gained by this switch.
Bagmaking process
Basic operates the new Rovema machine at speeds of 65 to 70 bpm, not slow considering the 28-oz fill volume. Printed film rollstock is supplied by Curwood (Oshkosh, WI). The five-layer metallized lamination includes oriented polypropylene that's reverse-printed flexographically in six colors. Other materials in the complex structure were not identified by Basic.
As on most vf/f/s machines, the continuous-moving film unwinds through a series of guide rollers to the forming collar. But the forming process on this machine is atypical. The forming collar and tube for this machine are rectangular. As film proceeds continuously around the collar and tube, proprietary heated sealing tools grasp the four corners of the film and create about a 1/8" edge that resembles pants pleats.
Maintaining fill accuracy
Potato pieces are dumped from a bin into a vibratory conveyor that feeds them into a 14-head Ishida scale system from Heat and Control (Hayward, CA) that maintains fill accuracy of within ±1-g/bag, a considerable improvement over the ±5- to 7-g/bag variance on scaling systems mounted to other machines in the plant. "It's greatly lessened our product giveaway," says Parks.
After filling, heated cross-seal jaws create the top seal for the filled bag and bottom seal for the next bag. Gusseting fingers fold the bag's sides inward, creating the gabletop carton shape. While the top seal is made, gusseting fingers fold the bottom sealed area flat up against the bottom of the filled bag to help it stand up.
Future investment
Filled and sealed bags are manually packed into corrugated trays before they're automatically film wrapped and conveyed through an older shrink wrapper. As the film shrinks around the nine-pack, it pushes down the bag tops. The shrink-wrapped packs are then manually stacked five-high on pallets. Pallet loads are trucked to Basic's Idaho Falls distribution center where they're stacked four-high in the warehouse.
"We've been happy with the Rovema machinery," says Parks. "This new continuous-motion machine does about 20 more bags per minute than our intermittent-motion form/fill/seal machines at the plant. And it gives us the flexibility to produce different bag styles whereas our other equipment can only make the pillow-style packs."
As to justifying the machine purchase, Parks tells PW, "This is an investment in the future. We're looking at packing other products in the Stabilo bag."
In summarizing the economics of the new machine and bag investments, Gordon Lewis points out that it's important to consider customer satisfaction. "Packaging is an important part of the new product equation. Customers are continually faced with operational and storage constraints that make packaging functionality a critical element of the product mix.
"At Basic American, we strive to maximize functionality through packaging format, copy and graphics. Packaging decisions are made on the basis of which elements add value for which the customers are willing to pay."