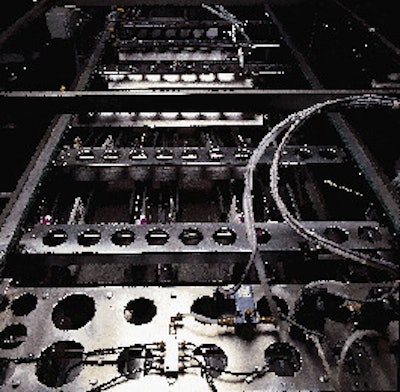
A leading maker of wood fillers, putties and adhesives, Eclectic Products is probably best known for its Goop® adhesive. Sales of this versatile home repair product have grown rapidly since Eclectic, which is headquartered in Springfield, OR, consolidated its manufacturing operations in Pineville, AR, in 1992.
Until recently, the firm was able to keep up with its growth with no more automation in its secondary packaging operation than two rotary blister-sealers, both supplied by Alloyd (DeKalb, IL). But as sales in the past year or so continued to climb, the handwriting was on the wall. "We had no choice but to automate," says plant manager Bob Bright.
And automate they did. A new blister-sealer/collator/case packer line dedicated to 8-oz tubes of Goop is attended by five people and runs at a steady rate of 45 packages/min. Before the automated system was installed, that same output required 12 to 14 workers.
A key supplier of equipment in the new line was Alloyd. Alloyd engineers also took responsibility for managing line integration.
According to Bright, his firm's experience with its first two Alloyd machines was enough to convince him that sticking with the same manufacturer was a good idea. So from Alloyd came a six-station rotary blister sealer. Each station has three blister cavities, and the machine runs at 15 cycles/min for a throughput of 45 packages/min.
Also contributing significantly was PMI Cartoning (Elk Grove Village, IL), which supplied three machines in the new line: an indexing conveyor, a collator, and the case packer. At the end of the line is a thermal- transfer printer that prints and applies a label on each case.
The line was installed in September, in a single day, says Bright. "We received the equipment on a Saturday morning at eight o'clock," he says. "By four o'clock that afternoon it was fully ready to run."
Pick and place
Secondary packaging begins as polyvinyl chloride blisters are picked from magazines and automatically placed in the cavities on the turntable of the intermittent-motion Alloyd machine. Alloyd also suplies the blisters, which are thermoformed from 15-mil Pentaform® PVC supplied by Klockner Pentaplast (Gordonsville, VA). Operators load an aluminum tube of Goop into each blister by hand, and paperboard backing cards are picked from a magazine three at a time and placed automatically on top of the tube. Supplied by Rohrer (Buford, GA), the 21-pt SBS cards are printed on a sheet-fed offset press in four colors on the front and one color on the back. Heat sealing of coated paperboard to blister follows, and the last station in the machine ejects the blisters.
Three vacuum arms pick up three finished packages and place them blister side down in the cavities of an intermittent-motion indexing conveyor. It carries the packs to the PMI collator.
A single DC motor drives the large turntable of the rotary blister sealer. Through linkage and gearing, this motor also drives the mechanical arms that load blisters and paperboard cards into cavities and the three eject arms as well.
Synchronizing all these motions is an onboard Allen-Bradley (Milwaukee, WI) 502 PLC and an Omron Electronics (Schaumburg, IL) encoder tied into the main drive shaft. As the encoder rotates from 0 to 360 degrees, it constantly signals its position to the PLC. Based on the program written for the application, this input enables the PLC to send output signals. The PLC's output signals govern the machine's movements. The end result is that a complex sequence of actions unfolds with precise timing.
Custom built
The indexing conveyor linking the blister sealer with the collator is about 10' long. Packages make a right-angle turn as they enter the PMI collator, which was custom-designed and built for Eclectic's needs.
Driving the design of the collator were the three pack patterns Eclectic uses (see photo). The same size shipper is used for two of the patterns. One consists of 12 blister cards loaded back-to-back; the other is a six-count pack with blister cards all facing the same way. In the latter configuration, workers manually apply polyvinyl chloride "clip strips" to the peg holes in the cards. Such strips are in demand by mass merchandisers whose employees open a case, grab the strip, and easily hang all six packages from a display hook.
The third case configuration has six blisters back-to-back, or "nested," like the 12-count, but the case is smaller.
The collator manipulates the individual blister cards into whatever case configuration is programmed. It then delivers either six or 12 blisters to a station on the case packer where a pneumatic ram pushes the blisters into a waiting case.
Step one in this sequence takes place as soon as six cards are in place at the collator's infeed area. All six cards are picked by vacuum cups mounted on an assembly that lifts and rotates each card 90° clockwise or counterclockwise, depending on the pack pattern, so that cards are traveling on their side edges. The machine operator selects the appropriate preset program from the system's memory.
With blister cards oriented on their edges, the lift-and-rotate assembly strokes forward and releases blisters into six lanes leading to the case packer's infeed bucket. The blisters are propelled forward by reciprocating bars that push the blisters forward 15" with each stroke. The distance between the lanes gradually narrows, so blisters are tightly compacted by the time they reach the infeed buckets of the case packer.
Buckets mounted on a track
In all there are 20 infeed buckets mounted on 133/4" centers on an oval track that resembles a tank tread in the way it rotates. This intermittent-motion track, which sits at a right angle to the lane guides of the collator, has one function: to provide a continuous supply of infeed buckets into which blisters from the collator can be inserted. Once filled with blisters, the buckets are indexed on the case packer to the loading station.
The number of packs in the infeed bucket is first verified by photoeyes from Banner (Minneapolis, MN). These sensors are aimed at the white caps inside the clear PVC blister, and if they don't detect the correct number of caps in the bucket, that group of blisters will drop into a rework bin.
Once the count is verified, a signal is given to erect a case and vacuum cups pull an RSC blank from its magazine. The packer's conveyor flights are also mounted on a track shaped like a tank tread. Cases are held in these flights, which run parallel to the path of the buckets carrying the blister cards. When the infeed bucket with its load of blisters reaches the pneumatic ram of the loading station, product is pushed out of the infeed bucket and into a waiting case. Tucker arms fold the case flaps and hot melt adhesive is applied by a Nordson (Duluth, GA) unit. After a compression station, sealed cases are discharged.
Some tops are taped
This routine changes slightly when clip strips have to be applied. The top of the corrugated shipper is left unglued so that workers can apply the strips by hand. Then they tape the top shut.
Also contributing significantly to the smooth operation of the line are a host of proximity switches and photoeyes supplied by both Banner and Turck (Minneapolis, MN).
These sensors constantly provide input to the two PLCs on the line so that actions can occur in the right sequence.
"With components like photoeyes, I try to standardize as much as possible," says Bright. "If there's a Banner photoeye on this machine and four other machines in my plant, then I can keep a couple of them in inventory and feel confident about being able to replace one if I have to on five different machines. That's what keeps downtime to a minimum.
"Same thing with motors," he continues. "I have a local supplier that can get me these motors right off the shelf. I can't wait four days to get a motor if I need one."
Bright says he was very specific, as the line was in its early stages of design, about the Baldor (Fort Smith, AR) motors he wanted the OEMs to incorporate.
"I specify Baldor motors whenever I can," he says. "They're not made cheaply."
The new Goop line has no shortage of them, either. On the collator alone there are three.
The other component vendor that Bright insists on is Allen-Bradley. "Their failure rate doesn't exist," he says. "PLCs, A-C frequency drives, emergency stop buttons-in this line they're all from Allen-Bradley."
Currently Eclectic runs the line one shift daily, though Bright says he's considering a second shift if sales growth continues to climb. Payback on the $250ꯠ line, he adds, is expected within 17 months.