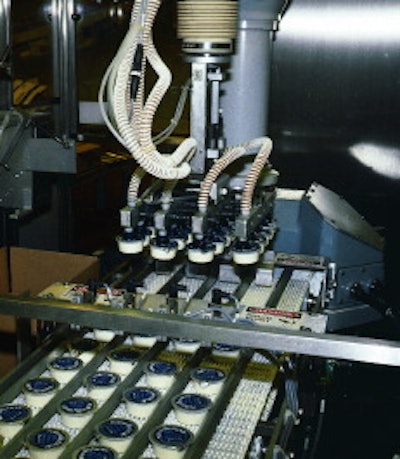
Born almost 30 years ago as a supplier of coffee creamer to airlines, Atlanta-based Eastern Foods has expanded to supply salad dressings, dips, sauces, oils and vinegars to a variety of institutional accounts and retail markets under its Naturally Freshยฎ brand. On the institutional side, airline business still accounts for a significant degree of its portion control cups of refrigerated salad dressings. But increased demand from institutional foodservice and restaurant accounts necessitated an increase in portion cup production at its Atlanta plant, which PW recently visited.
Of the facility's 15 packaging lines that fill a variety of products and container sizes, six are dedicated to portion cups for salad dressing. The six portion cup lines are run two shifts/day to produce 76 varieties of salad dressings in cup sizes from 3/4- to 4-oz.
The company had been relying on an older model of portion cup filler with an aging mechanical case packing system. That unit would pick a row of finished cups off the line with a back-and-forth vacuum head and place them into a corrugated case, forming layers a row at a time. Trouble was, it was slow and occasionally caused damage to the delicate cups. When it came time to upgrade its 3/4-oz cup filling line, Eastern needed an automatic case packing system that would keep up with the new filler's 500/min speeds.
The solution turned out to be a robotic packing station from Flexicell (Richmond, VA) that was specifically engineered to work with the portion cup filler, supplied by Winpak Portion Packaging (Bristol, PA). Both suppliers as well as Eastern Foods claim that this is the first such installation that matches robotic case-packing with portion cup filling at high speeds.
"Compared to the mechanical packing system, the robot operates much more smoothly," says Jerry Greene, executive vp at Eastern. "It has a much shorter distance to move, and isn't as rough on the cups. As a result, we're able to basically double our production." Eastern liked the unit so much that a year later, in March '96, it bought a second filler and robotic packer to upgrade its 2-, 3- and 4-oz line. That line now runs at 300 cups/min. Two more fillers and packers are approved for this year with two more planned for 1997.
Many parts, one whole
More than the sum of its parts, the Flexicell machine contains a variety of components from several equipment manufacturers that are engineered to work together as one system. At its heart is a washdown-grade robotic arm and 486-based controller from Adept Technologies (San Jose, CA). Next to the 2-oz line is an automatic case erector from Wexxar (Naperville, IL) that erects and bottom-tapes cases and supplies them to the robotic packing station via a short conveyor. (Eastern used an existing erector for the 3/4-oz line.) Also included is an automatic chipboard sheet inserter from MGS Machine (Maple Grove, MN). It places a tier sheet in the bottom of each empty case as well as atop each layer of cups.
The single greatest benefit of the robotic packers, according to plant manager Ed Wicker, is increased productivity. "On the old packers, we were running at 50- to 60-percent efficiency" as a result of downtime, which was often related to damaged cups.
By contrast, the robot is much more reliable. "We're now running at 80- to 90-percent efficiency," says Wicker. In addition to the higher output, Eastern has cut its labor costs in half for each of the two lines, since only two operators are required per packaging line versus four previously.
Another significant benefit is that the machine is also able to handle the delicate and top-heavy 3/4-oz portion cups without mishandling or damaging them. Eastern's previous mechanical packer wasn't so graceful, requiring an inspector at the end of the line to check for damage.
Unlike the mechanical case packer, which is dedicated to one case size, the Flexicell machines can be changed over to accommodate a new cup size and packing pattern, though it's by no means a speedy process. "We don't change case sizes that much," admits Greene, who says it takes about two hours. Adds Wicker: "We haven't had to do it enough to get it as fast and smooth as a pit crew operation."
Changeover involves selecting the new pack pattern with the machine's controller, changing out the robotic head and adjusting the width and alignment of the lanes on the accumulation conveyor.
Double-indexing fillers
The new fillers are standard portion cup fillers that denest preformed high-impact polystyrene cups--also supplied by Winpak--and fill and heat-seal them 4-up. The filler on the 2-oz line places precut foil lids, whereas the filler on the 1-oz line die-cuts the lids out of a paper/film rollstock. (precut foil lids are used for bigger cups because they offer direct placement on each cup without the tracking problems associated with a wider roll of film.) All lidding is sourced through Winpak as well.
To achieve the high line speeds, both fillers index two rows of four cups at a time through each station of the machine. "Compared to the older fillers we had," says Greene, "these are more reliable and require less maintenance."
Though cups are filled four-up, at the end of the 3/4-oz filler an air diverting device gently blows every other cup into one of two lanes, spreading the four lanes out into eight lanes. On the 2-oz line, cups remain in four lanes. On both machines, after exiting the filler, cups travel on a 10' accumulation conveyor that also serves as the infeed to the robotic case packer.
At the other end of the accumulation/infeed conveyor, lanes of cups accumulate to form a pack pattern. When sensors detect the appropriate number of cups in each lane, the robotic head--outfitted with a separate vacuum head for each portion cup--lowers and picks up the cups. It picks up 40 cups per cycle (8 lanes of 5 cups per lane) or 20 cups/cycle (4 lanes of 5 cups), depending on the cup size. Cycle speeds range from 12.5 to 25 cycles/min.
A high-volume, low-pressure vacuum is used to pick up cups without crushing them. The vacuum is also designed to work in a wet environment, as water is sometimes present on the containers.
When the head lifts, the rows of individual vacuum heads squeeze together, eliminating what used to be the space between lanes of cups. The head then pivots to the side and lowers the product into a waiting corrugated RSC. When the head returns to the home position over the conveyor, the rows of vacuum cups spread out again.
Meanwhile, an MGS (Maple Grove, MN) sheet inserter automatically deposits a chipboard tier sheet on top of each layer of cups. Once five layers of cups is packed--typically 100 or 200 cups per case--the box passes through an existing case sealer that uses pressure-sensitive tape.
Cases then pass by a Patrion large-character coder from Marsh (Belleville, IL) that is one of the first such installations of this unit for testing under actual production conditions, according to Wicker. Two heads--one mounted on either side of the conveyor--print the product name and product code. Also printed on one side of the case are date, time and other information related to product tracking.
Wicker says the Patrion's large keyboard and display contribute to entry accuracy. "Some calculator-type keypads are small and difficult to handle." Jerry Greene adds, "We've cut down on code dating errors significantly. We've had good success with Marsh."
Solving an industry problem
Greene feels the Eastern Foods installation may signal the beginning of automation of case packing for the portion packing industry. He estimates that 80% of the portion packing industry is still case-packing cups through manual or semi-automatic means. As filling speeds increase, case packing this way becomes a much less practical solution, pointing up the need for automation. "I know there have been several attempts to automate case-packing for this type of filler," says Greene, "but apart from what we've got, nothing has really materialized yet." He adds, "I've always felt that if you could have a case-packing system that could go with these fillers, it would solve the industry's problem."
Greene says the two suppliers continue to work together to refine the process. "They're looking at some new ways to actually pack the cups as soon as they're filled, right off the filler, without an accumulation conveyor."