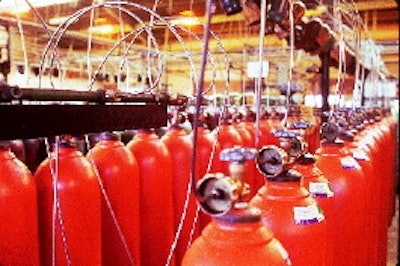
Despite the burst of attention paid to oxygen generators because of their alleged role in the ValuJet crash in Florida, it is really gas cylinders--totally different and considerably bigger and older than oxygen generators--that are center stage at the Research and Special Projects Administration (RSPA). This is the Dept. of Transportation (DOT) agency charged with assuring the safety of hazardous materials packaging. RSPA published a mildly-controversial, narrow final rule on cylinder retesting in May, and is about to unveil what doubtless will be a contentious mega-rule meant to "accommodate contemporary manufacturing technology...and make safety enhancements." This imminent rule, when it becomes final, will have a big impact on the price of new cylinders and the cost of retesting old ones. Safety requirements need to be updated. There are certainly some parallels between unheeded warnings about the Federal Aviation Administration's (FAA) hazmat program--for example, a 1992 internal report by FAA's office of civil aviation security--and ignored recommendations on improvements to the RSPA cylinder rules. The National Transportation Safety Board (NTSB) made recommendations on cylinder safety after serious accidents in 1988 and 1993. Both the RSPA and the Compressed Gas Assn. (CGA) failed to implement any of them. Industry has its own cylinder spec change wish list. "We need to harmonize U.S. cylinder specs with international specs," explains David Sonnemann, manager of DOT and Fleet Safety at Praxair, Inc., one of the largest packagers of industrial gases in the U.S. "Now, when we get a cylinder manufactured in Europe at one of our U.S. facilities, we have to retest it to make sure it passes the DOT requalification standard. That represents an additional expense. "And if it doesn't pass the DOT test, we have to scrap it or return it without refilling with product. That's another cost." The DOT requires cylinders to withstand a test pressure of five-thirds of the service pressure of the cylinder. The European standard is 11/2 times. DOT statistics estimate there are about 100 million cylinders in circulation in the U.S. Praxair alone owns five million cylinders, which are refilled on average three or four times a year. The airline industry alone uses cylinders for about 350 tasks, including providing emergency air to passengers, a role that oxygen generators has begun to usurp. Jim Jones, chief of the approvals branch at RSPA, says a 747 has 350 different cylinders for various applications, including tasks such as deploying the emergency exit chute and the emergency brakes. In all fairness, the accident record for cylinders appears to be pretty good. There were 51 incidents between 1991-95 where the RSPA reported "packaging failure" as the cause of a hazardous materials accident. Those resulted in two major injuries, 19 minor injuries, no deaths and just $82궍 in damage. These statistics only cover cylinder accidents involving transportation. So an explosion of a propane cooking cylinder would not be included. The RSPA requires hazardous materials to be carried in cylinders that meet any of about 20 specifications. The cylinders have DOT numbers such as 3A, 3AA, 3HT (for airlines), and 4BA. DOT certifies independent inspection agencies who review the manufacture of every cylinder, or batch of cylinders, in the U.S. Those agencies in turn license "retesters." Depending on the cylinder and what it holds, it must be retested, generally, every five or 10 years. The retesting rules needed to be cleaned up and ostensibly simplified because they were either misunderstood or ignored by too many retesters. But the proposal the RSPA surfaced on October 18, 1995, went beyond simple "regulatory simplification" and suggested some fairly significant changes in the retest and inspection rules. For example, the agency had proposed requiring every cylinder owner to have his cylinders restested by a company with a retester identification number (RIN). Some companies such as Tanner Industries, Inc., which packs ammonia in large cylinders, retests its cylinders itself via visual inspection. Tanner does this every five years, instead of sending the cylinders out for hydrostatic retesting every 10 years. Visual retesting is legal as long as it is done by someone who is "competent." Dave Binder, a compliance officer at Tanner, says it is difficult to find a retest company who has large enough "water jackets" with which to test the large ammonia cylinders. Even if those retesters were conveniently located, each retest can cost about $27/cylinder. There is also an additional cost because Tanner has to depressurize the cylinder and pull the valve before sending the cylinder to the retester. On the cylinder's return, it has to be flushed and refilled, sometimes with a lower value-added gas, perhaps for agricultural use. Tanner might have to retest 10 or 20 cylinders a day, based on the 100 to 200 they refill daily. In the final rule RSPA revised its proposal "to clarify that a person is not required to obtain a RIN if the person only performs visual inspections on DOT specification or exemption cylinders." Binder says, "That's good for industry and it still maintains the safe transportation of hazardous materials cylinders."