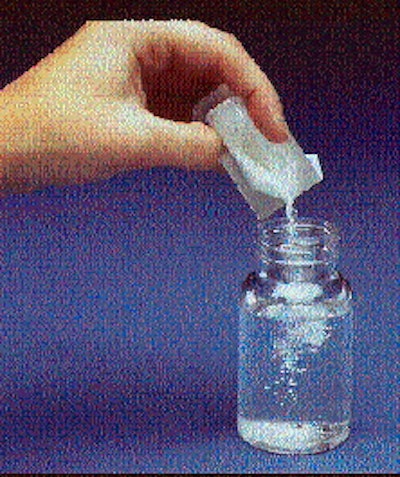
When a product is used to detect dangerous contaminants in drinking water, customers need to feel confident about the product's reliability and consistent quality. Idexx Laboratories of Westbrook, ME, recently gained such confidence in its blister pack of Colilert® reagent powder by switching from a polyvinylidene chloride-coated laminate to high-barrier Pentapharm® ACLAR® film made by Klockner Pentaplast of America (Gordonsville, VA). (ACLAR is a registered trademark of AlliedSignal, Inc.) Idexx is so pleased with the film's performance that it recently extended its use in blister packs for two newly introduced bio-detection products.
Used in labs at municipal water utilities, Colilert is a reagent powder used to test water. It's added to a 100-mL sample, and if the water turns yellow after an incubation period, this indicates the presence of coliforms and tells those performing the test that further testing is required to see if the dangerous E. Coli is present.
Originally developed by Environetics, the Colilert product line was bought by Idexx Labs in 1992. Environetics had just recently switched from small glass test tubes filled manually to break-tip blister packs produced on horizontal form/fill/seal equipment. This f/f/s approach brought significant advantages-including triple the output, a 22% reduction in material costs, and a 60% reduction in labor costs. But the vinyl/polyethylene/PVDC lamination used to make the blister had a serious drawback: It had a tendency to turn yellow, which in turn made the product itself look yellow. This was clearly a problem when the change from white to yellow is the whole key to Colilert's performance.
"Customers were afraid that powder that appeared yellow due to the color of the plastic would not give accurate test results," says product manager Andy Meyer. "Until we switched to the new film, which doesn't turn yellow, we enclosed a note in every package, explaining that if any of the packages had turned yellow, this was only the plastic and that the powder inside was in perfect condition. We encouraged them to pour out the powder onto a piece of white paper so they could verify that the product was still good."
Unwanted complication
This introduced another step in the otherwise simple process of using Colilert. Idexx couldn't accept that because simplicity of use is one of Colilert's main advantages over competitive products.
So operations manager Melanie Meyer and a group from Quality Control searched for a new blister film that wouldn't yellow and would provide moisture protection equal to or better than the PVDC coating in the three-layer lamination. "We don't change packaging lightly here because it directly affects our product," she says. "We tried different materials, different thicknesses of lamination, and still the film occasionally turned yellow."
For help Idexx turned to Klockner Pentaplast, who suggested trying Pentapharm ACLAR 190/02. It consists of a 10-mil layer of polyvinyl chloride adhesive laminated to a 0.9-mil layer of ACLAR fluoropolymer supplied to Klockner by AlliedSignal (Morristown, NJ). Melanie's group began rigorously testing it in October 1994 and was so pleased with the results that they put it into production two months later.
"When we looked at the test results, we saw such a dramatic improvement in barrier performance, compared to the other materials we'd tested, the decision was obvious," she says. The test that all the other films had failed was subjecting the package for several weeks to elevated temperature and humidity conditions.
"The Klockner Pentapharm ACLAR is rock solid after even more than that time under those conditions," says Andy Meyer. And on top of superior water vapor barrier characteristics that are critical with such a hygroscopic product, the material doesn't turn yellow.
"Now we have a light-weight package, with the best moisture protection possible and no discoloration of the vinyl to cast any doubt on the quality of our product," says Andy. According to Klockner, the moisture vapor transmission rate (MVTR) for the flat sheet used by Idexx is .014g/100 sq"/24 hr at 38°C and relative humidity of 90%.
The Klockner film is not only being used for the regular 24-hour Colilert product but also for a new 18-hour version, plus a new product called Enterolert. Introduced in March '95, it detects the presence of enteroccocus bacteria.
Idexx produces blister packs of all three products on a thermoform/fill/seal machine that forms blisters four-up from rollstock. A volumetric powder filler feeds the product to a preset weight between 2 and 4 g. Speeds are in the range of 55 to 85 four-blister units/min, depending on which product is running.
Lidding material, a lamination of paper and 1-mil foil with heat-seal coating, is supplied by Hueck Foils (Manasquan, NJ). As it unwinds from its roll, it's imprinted with product and company identification as well as lot number and 12-month expiration date. The foil is then heat sealed to the forming web and after a series of perforation tools and a punch station, the 4-blister unit emerges. Randomly selected packages are subjected every half hour to a vacuum seal test to verify seal integrity and absence of pinholes. Finally, 50 packs are loaded manually into a chipboard carton.
Melanie acknowledges that the Pentapharm ACLAR material carries an upcharge over the former material, but she declines to quantify it. "It's worth it," she says simply.