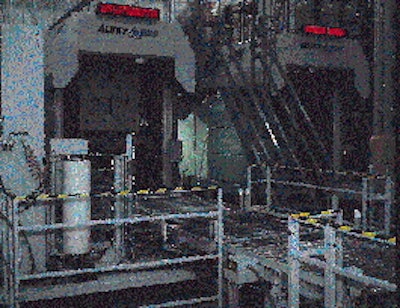
Ocean Spray Cranberries operates plants in six states, but until recently it had no manufacturing muscle in the fast-growing Southwest. That changed dramatically last September when the Lakeville, MA, firm officially opened its $50 million, 200ꯠ-sq-ft plant outside Las Vegas in Henderson, NV.
On three lines-multi-serve, aseptic, single-serve-the plant is capable of packaging all 16 Ocean Spray fruit juices and drinks as well as a variety of aseptically packaged concentrates. A look at the single-serve line illustrates much of what makes the Henderson plant special. The line can fill both aluminum cans (5.5- and 11.5-oz sizes) and glass bottles (10 or 16 oz). Targeted speeds are 500/min for 16-oz glass, 600/min for 10-oz glass, and 1ꯠ/min for 11.5-oz cans. Thus far no production of 5.5-oz cans has been scheduled. These small cans are used mostly in foodservice settings, and Ocean Spray will begin running them later this year.
"We were driven to create a multi-package line because we wanted high speeds from a capacity perspective but we knew we wouldn't have huge volumes until later in the plant's life," says project manager Greg Raco. One way to ensure high-speed filling is to install dedicated lines, but this was considered unacceptable, says Raco, because it would have meant tying up too much capital and then watching those assets sit idle for several years as volume was building.
"Keep in mind that single-serve packaging is still quite new for Ocean Spray," says Raco. "Multi-serve containers are what we're more experienced at. A lot of our growth in single-serve will be in the future. So if we had gone into production with dedicated high-speed can and glass lines in 1994, the lines probably would have been about 40% utilized for several years."
When demand for product in cans and glass outstrips the current line's ability to keep pace, one of the two fillers will be moved to its own line, and at that point the Henderson plant will indeed have dedicated lines for glass and aluminum. But only when they're justified.
Until then, Henderson is the only Ocean Spray plant that organizes filling lines by container size, not by material. In its other plants, all glass bottle sizes are filled on a single line. At Henderson, the company will enjoy substantial improvements in efficiency and reductions in changeover time by grouping multiserve glass and plastic bottles on one line, single-serve glass and aluminum on another line.
Changeover goals
"We had clear-cut goals in terms of changeover and operating efficiency," says Raco, "and to meet those goals we felt we should avoid coping with a changeover from 10-oz glass to 48-oz glass. As we looked into it, we realized that the similarly-sized containers, whether 11.5-oz aluminum or 10- or 16-oz glass, all had fairly consistent dimensions and shared similar equipment." So large glass and large plastic bottles go on one line and small containers stay on the single-serve line.
As for equipment that makes up the single-serve line, "There's nothing earth-shattering about the individual machines on this line," says Raco. "In fact, we deliberately avoided 'bleeding edge' technology where the machines are concerned. We picked winners from our experience in other plants and then assembled the best line possible."
Because both bottles and cans run on the line, it incorporates two fillers and plenty of conveyor trackwork that takes containers through or around a filler according to need. Elsewhere, preprinted cans have to be diverted around a bottle labeler and bottles are diverted around a plastic ring carrier applicator. Again, diverter gates on conveyors take care of this. In either case, the containers eventually wind up on the infeed conveyor of the same tray packer, supplied by Standard-Knapp (Portland, CT).
While sticking pretty much with the tried and true on equipment selections, Ocean Spray was much more aggressive when it came to management information systems (MIS) and computer-integrated manufacturing (CIM). Consequently, say Raco and the key vendors involved, the real-time production and inventory reporting system operating at the plant may be unparalleled.
"Several pieces of software here were Beta versions as we were designing the plant," says Raco. "But then we have some pretty high case requirements we're trying to meet. In a day we're supposed to make 35ꯠ cases of 11.5-oz cans. And 16-oz glass should be in the range of 24ꯠ cases per day. CIM will play a key role in getting us to that point."
Systems integration was largely the responsibility of Dynalogic Eng. (Kennesaw, GA). The brain of the single-serve line is a 540E PLC, a programmable logic controller from Allen-Bradley (Mil-waukee, WI). Dynalogic wrote a program for it that controls all the conveyors on the line and interlocks all machines. Through photo cells, proximity switches, counters or other sensing devices up and down the line (there are more than 100 photocells alone on the line), digital inputs are constantly sent to the 540E. These updates on line conditions give the 540E the information it needs to "tell" machines and conveyors what to do and at what speeds.
Graphical user interface
Operator interface with the 540E is through FIX DMACS, a SCADA (supervisory control and data acquisition) software package from Intellution (Norwood, MA). Personnel on all levels, from the plant floor to the control room to Ocean Spray headquarters in Massachusetts, can gain access to real-time process information through personal computers.
On the plant floor, operators constantly update the system's data base to reflect current conditions. For example, if downtime occurs at the traypacker, an operator at the machine can enter that fact and its cause on the data base. Instantly the information becomes available plant-wide.
Could the information have been captured without the software assist? Of course it could, but probably on a log sheet, and probably in an inconsistent (or illegible) format depending on the operator. And then that piece of paper would be the only place the information was available. For anyone else to make use of the information, someone would have to put it in a management report and disseminate it. In Ocean Spray's case, the information is clear, consistent, and available plant-wide on a real-time basis.
Raco believes features like this are what make the line special.
"What's going to take this line to the next level of performance is its integration from an information systems standpoint," he says. "Real-time data is readily available, so as soon as a run is finished the team can compare its performance with targets and seek opportunities to improve on the very next run. They don't have to wait for a management report that reaches them the next day or next week."
Another good example of the real-time data acquisition and reporting system in action is at the two Alvey (St. Louis, MO) palletizers at the end of the line. Each machine has mounted above it a large LED readout that communicates with line operators. As the day's production schedule unfolds, constant updates automatically appear as scrolling text on the LED readouts. Operators are told how many cases are left in a run, when a clean-in-place process is scheduled, what the upcoming product will be, and so on.
"It's all a matter of giving people information so they can make good judgments about how they need to prioritize their tasks," says Raco.
Sophisticated inventory management
Inventory management is also tied into the system. The program automatically verifies inventories of product and packaging supplies prior to the beginning of a run, so if the necessary materials aren't available, an alarm will alert management that the run cannot begin.
Another check on inventory is done at the depalletizer, which was supplied by Simplimatic (Lynchburg, VA). Bulk pallets of cans or glass all have a bar code applied by the vendor, and as a pallet enters the depalletizer, the bar code is scanned. If the container is not the one called for in the production schedule, once again an alarm brings it to the attention of the appropriate personnel.
Inventory adjustments to the system's data base depend not on the number of pallets that enter the depalletizer but on the number of layers the depalletizer sweeps off. So if a run of cans ends while half a pallet is still in the depalletizer, that pallet can be backed out of the depalletizer and the warehouse inventory will still be exact.
Bar code scanning is as useful at the tail end of the line as it is at the beginning. After full pallets of packaged product are stretch-wrapped by a machine from IPM (Naples, FL), a thermal transfer print-and-apply labeler from Imtec (Bellows Falls, NY) puts a bar-code label on the pallet wrap. When the fork lift driver picks up the pallet, he scans the code and then looks at his on-board computer to verify in which warehouse slot the load belongs. When shipments go out, the same system directs pallet pickers so that FIFO inventory can be maintained.
Because communication is so vital to achieving optimal efficiency on the line, it was laid out in such a way that operators have good sight lines of machines and each other. "We spent a lot of time configuring the equipment to optimize the team's resources," says Raco. "The dynamics of the three or four key people that run the line are good because those people are all within 20 feet of each other."
Now that the line has been running for almost a year, says Raco, some of the targets set by Ocean Spray are within reach. That includes being able to accomplish a flavor change in five minutes and a size changeover in 15. Helping to speed up changeovers are wheeled carts on which parts are stored. When they're needed on the line, they're quickly wheeled into place.
Naturally training has been a key ingredient in the plant's first year.
"There was a vast amount of information for people to absorb and remember," says Raco. "It's one thing to show someone how to operate something. But to analyze and trouble shoot and fix problems takes time. That's what the people in this plant have learned to do."