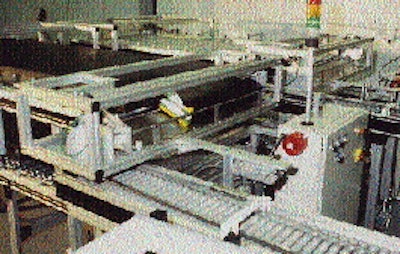
As movie and music videos continue to gain popularity worldwide, they present considerable opportunities for all related businesses. That pleases Sony Music Operations, the U.K.-based video cassette manufacturing arm of Sony Music Entertainment U.K., a subsidiary of the Japanese parent company. On the flip side, the booming video cassette business created somewhat of a packaging dilemma for SMO: How to efficiently handle production runs as small as a few hundred to runs numbering in the tens of thousands. The solution: Internally powered conveyor rollers from Interroll (Wilmington, NC). The rollers guide video cassettes along three identical 25-meter (82') lines that continue from post-manufacturing through labeling, film wrapping, boxing and overwrapping functions. Material handling specialist Robdale Ltd. (Woking, Surrey, England) worked with SMO to develop the packaging lines. Two of the lines account for the majority of video cassette output. The third is used primarily for rental cassettes. Maximum line speed on each of the two primary lines is 16/min. That amounts to 23갈/line/day. "We use Interroll conveyors throughout our lines," notes Sony's project engineer Phil Roberts. "The lines work on somewhat of a flow system that's run by the video cassette packaging machine towards the end of the line. If that machine stops, all machines upstream of it have to stop as well. For example, the film wrapper has to be stopped so film doesn't feed into it and burn. We use powered rollers that allow us to start and stop before each machine as necessary. We bolt on sensors and use photocells between roller gaps to help track the cassettes through the line(s)." The line(s) begin as recorded and wound video cassettes discharge from a clean-room manufacturing area onto a two-lane conveyor. One lane carries cassettes to an upper-level accumulator; another to a line-level accumulating station. These accumulating stations are also referred to as "buffer zones." When video cassettes from one level run out, the other level takes over. Additional cassettes from manufacturing replenish product at the both stations to maximize efficiency. Cassettes are moved to each buffer zone, or accumulating level, via two Interroll Driveroll® internally powered rollers. The 1.9"-diameter Driveroll rollers can be installed and removed quickly by means of a spring-loaded shaft, and by connecting or disconnecting a single electric wire. A Mitsubishi Electrical (Hatfield, Hertfordshire, England) programmable logic controller works in conjunction with electronics built into the Driveroll rollers. These electronics sense the presence of the video cassette. That information is used by the PLC to determine whether it should continue to send additional cassettes, or slow or stop according to cassette traffic. Cassettes are collected in groups of 36, on their spines, at both buffer zones. Once the entire group of 36 is sensed by the PLC and Driveroll rollers, cartridge arms gently guide the group onto a roller conveyor system, in correct orientation, for downstream labeling, wrapping and packing. Video cassettes continue along a 2-meter Interroll Modulink Light conveyor section to two print and apply labelers. One unit applies a face label, the second a spine label. Rollers are positioned with gaps between to assist in label application. Labels are tamped on under the control of photocells that monitor the cassettes as they pass the labelers. After labeling, cassettes index along another section of Driveroll conveyor. Roberts refers to this section of conveyor as a "lifting" conveyor because one end is hinged. Lifting the opposite end creates a clear path for employees to exit. The labeled cassette is turned over and a 90° cross-pushing device sweeps it onto a belt conveyor and through a film wrapper. Polypropylene film is used for customers requesting it. A powered roller section delivers the cassettes to the C.F.D.A. (Teteghem, France) packing machine where inserts may be added prior to the cassette being placed in what Roberts refers to as a PP "library case," which is similar to the hinged clamshell that holds video rentals in the U.S. Cased cassettes pass through another labeler, then are placed into corrugated trays for downstream palletization and distribution.