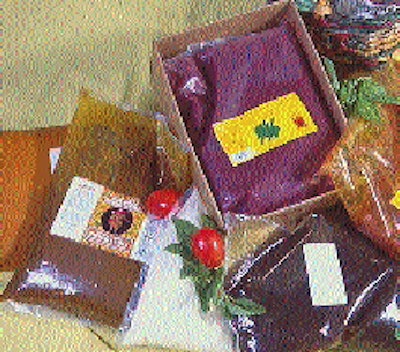
In the early 80s, J. Michael Buscaino made pesto sauce in his basement and sold it to a single retail store in the Miami area. This year, his company, Fontina(TM) Foods, predicts sales of $6 million, a threefold increase over 1994's. This impressive growth is attributable in great part to a new 27ꯠ-sq-ft headquarters facility in Port St. Lucie, FL, where Fontina processes herbs, sauces, chutneys, salsas and cobblers, then fills them into flexible pouches or bottles on either of two new lines. Products are sold both under Fontina Foods' brand name and private labels.
Approximately 60% of Fontina's sales are packaged on a Key-Pak V-350 from Research & Development Packaging Corp. (Lebanon, NJ). The vertical form/fill/seal machine is equipped with a Model SP-160B liquid piston filler from Hinds-Bock (Redmond, WA). This customized system packs more than 30 SKUs, including both hot-fill products and ambient-temperature fills. Fontina's products range from water-thin juices to particulate-laden sauces. The primary package is a 1-gal pouch filled at about 15/min; production of 1/2-gal sizes, filled at 25/min, is limited. A 6-oz pouch may also be in the cards.
The second line fills some 25 SKUs into glass or polyethylene terephthalate bottles, in sizes from 1 to 32 oz, at speeds between 60 and 100 bpm. At the heart of this line is another Hinds-Bock filler.
Fontina (the name comes from an Italian cheese) sells about 90% of its production to the foodservice market, primarily restaurants. Another 8% goes to institutional customers, mostly other sauce producers. The remainder is sold to specialty retail outlets in Florida and New York.
Pouches replace pails
Pouches produced on the vf/f/s line have replaced 1-, 2- and 5-L high-density polyethylene pails/lids, which were filled by a contract packager. The change results in numerous benefits for Fontina Foods and its customers.
"We wanted to get out of HDPE pails for several reasons," says Craig Basiliere, Fontina's director of operations, purchasing and supplier quality assurance. "Our customers were demanding flexible film as a means of easing solid waste disposal problems. There's a big space, weight and cost difference between disposing of a corrugated case and two 1-gallon pouches versus two gallon pails. Switching to pouches was a perfect opportunity to give customers what they wanted, and in turn, save us considerable money."
Much of Fontina's savings are labor-related. "We use two people to fill the pouches compared with 10 needed by the contract packager to denest pails, fill them, apply tops and label them," notes Basiliere. "Labor savings alone will give us a return on the investment in about 8 months."
Besides labor, the change to pouches reduces material costs. "We used to pay 78 cents for the pail and lid. It's about 20 cents now for the film required for the 1-gallon pouch," he points out. "That reduction helps offset rising costs for things like raw materials and corrugated. This means we're able to hold the line on prices for our customers."
Warehouse space savings offer yet another advantage. "Instead of bringing in a truckload of pails, I order a single pallet of film," he says. "That pallet takes up about 4 percent of the space of a load of pails, so that's a 96-percent space savings."
Custom vf/f/s
The actual filling process on the vf/f/s line begins as product is pumped from an adjacent processing room to the 20-gal hopper of the Hinds-Bock SP-160B, which is mounted above the Key-Pak machine. The single-piston filler pushes the liquid product through a valve spout which extends into the filling tube of the Key-Pak.
"We like the Hinds-Bock liquid filler because it is versatile enough to work with everything from a thick, heavy paste to liquid as thin as water," he says. Plus, "we needed a filler that wasn't going to break up the particulates in our sauces," he continues. "We put whole olives, mushrooms and so forth into the product. We want those to be intact at the restaurant so that the recipes they serve look as though they've been cooked in their own kitchen. We don't want broken vegetables, we want them whole. The Hinds-Bock filler does that for us."
For the most part, Fontina personnel have foodservice, not packaging backgrounds. "We realized that as a small company," Basiliere explains, "we weren't going to have an army of engineers running around. In making our equipment purchasing decisions, we needed good, reliable machinery that was easy to change and maintain.
"There are many excellent machines out there that can handle much greater volumes and speeds, but we really don't need them," continues Basiliere. "They're almost overengineered for our volumes. We matched the Hinds-Bock filler and the Key-Pak vertical machine, and that cost us about half of what some of the larger, higher-production machines would have."
Tough film is beneficial
The Key-Pak's unwind holds a 25"-wide web of film for the 1-gal pouch size. The approximately 4-mil film structure, from Curwood (Oshkosh, WI), comprises a 3-mil coextrusion of ethylene vinyl alcohol and adhesive, laminated to a 1-mil layer of biaxially oriented nylon, inside out. Basiliere says that the film structure was developed to meet hot-fill demands, so it more than suffices with ambient fills. The 1-gal pouch replaces a #10 can for foodservice customers. The same Curwood film structure is used for the 1/2-gal pouch.
"The machine, and the film's EVOH layer, provide excellent sealing characteristics," he says. "It also guarantees us good shelf life. We work with about a 6-month shelf life. We did extensive testing of the film with Curwood and we really expect the life to be closer to a year. Also, the film's thickness makes it pretty tough to damage. It resists sliding and friction in the outer corrugated case that could cause damage."
The film unwinds through a series of rollers to the forming collar. Film is driven through the f/f/s process via dual stepper motors. The machine is equipped with an ink imprinter that stamps a freshness date onto the film structure. The film is formed into a tube shape. Heat sealing creates a longitudinal fin seal. Teflon-coated sealing jaws heat-seal the bottom of the first pouch formed from this film tube. Microprocessor control helps the machine deliver the precise amount of liquid into the pouch. During the fill, the Key-Pak uses micro stepping motors that carefully pull the film tube downward, by the length dimension of the pouch, as it's being filled. Unlike many bottom-up filling applications where the spout descends to begin the fill, then ascends during the fill, this process moves the pouch downward while the spout remains stationary. The sealing jaws then simultaneously heat seal the top of the initial pouch and the bottom of the trailing pouch.
Film is cut off between the pouches and an operator takes the filled and sealed pouch from the discharge end of the Key-Pak machine, then places it on a portable rack, or stand. Basiliere plans to add a conveyor in the near future to automatically deliver pouches to downstream case packing.
A Comstar (Strongsville, OH) Model 470 thermal-transfer label printer is used to print product name, nutrition and ingredient statements and a bar code on a pressure-sensitive label that's hand-applied to the pouch. Labeled pouches are transported to a Durable Packaging (Countryside, IL) Do-It-All(TM) case erector/sealer. The machine erects the case, an operator places either 2 1-gal pouches or 4 1/2-gal pouches into each case, then the machine folds in top flaps and applies tape to the top and bottom of the case.
Carton Sales & Manufacturing (Miami, FL) provides the 200#-test, C-flute corrugated shipping cases that are manually stacked onto pallets and shipped via truck, usually refrigerated, to distribution centers throughout the U.S.
Outgrew its CP
"We started out in retail by making sauce in the middle of the night, but it was foodservice accounts, particularly General Mills' restaurant group, that helped us hit it big," says Basiliere. The group includes Red Lobster, The Olive Garden and China Coast [an Orlando, FL, establishment] restaurants. Basiliere notes that before the new facility was erected, the company had only administrative offices in North Palm Beach.
"The contract packager we had used did a great job in helping to get our company going," he says. "But we simply outgrew them. As business expanded they ran out of storage space for our packaging materials, raw materials and finished goods. We were taking over their plant. We ended up buying refrigerated trailers and docking them at their site." Fontina president Buscaino and Basiliere decided in late '93 that if the business was going to flourish, the company would have to build its own facility.
After nearly a year of scouting sites within Florida, Fontina was enticed by business incentives offered by the city of Port St. Lucie. "We moved in last December, trained people and started full-time production in February," says Basiliere. "We expect our sales to reach $6 million in '95, compared to $2 million last year, and anticipate 200- to 300-percent growth in the next five years."
Fontina expects much of this growth through the introduction of additional products, which the new packaging lines make possible. "We couldn't have increased our volume at our contract packager," says Basiliere. "By going in-house with our packaging, we've already added about a dozen new SKUs."
The bottle line has also allowed the company to introduce new products. The latest are in the 1- and 12-oz size, including a 12-oz barbecue sauce that Hooters sells to consumers at its restaurants.
By the end of '95, Basiliere expects Fontina's new plant to be HACCP-certified, a recognition that he believes will further increase business. "HACCP is a hazard analysis of critical control points that indicates the plant meets specific food safety measures. It involves documentation to ensure safety all the way from our vendors' raw materials, throughout our processes, to the point where product goes out our doors. We feel it will be mandatory in the next three or four years, so we've decided to be proactive and attain the certification. We're working on a shared technology program with NASA [National Aeronautics & Space Administration] to help us implement it."
To meet this certification, Fontina will likely add metal detection equipment to its filling machinery. "We're already using them at our raw materials end, but in the near future, we'll be looking to add a system in the product transfer pipes above the filler," says Basiliere.
Clearly, Fontina Foods is not content to rest on its laurels. "We've gone from contract packaging to in-house manufacturing," Basiliere summarizes. "We've developed a market niche, just as you [Packaging World] have. We have aggressive growth plans and this new plant and our packaging equipment will help us get there."