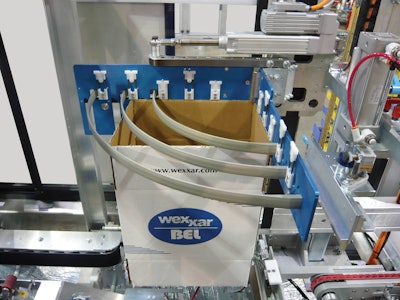
Servo-based motion continues to replace both mechanical and pneumatic alternatives in many packaging machinery categories.
A recent example is the WF30 case erector from Wexxar (www.wexxar.com), which is available with either tape or glue-bottom sealing. Because it relies on servo motors, it’s capable of 30 cases/min while comparable Wexxar machines that are pneumatically driven top out at about 20 cases/min. Added benefits that come with the new servo-based motion, says Wexxar general manager William Chu, are reduced energy consumption, a closed-loop exchange of data that enables the machine to react to changing conditions of corrugated board material, and a whole new level of operator friendliness and ease of use.
“With pneumatic cylinders,” says Chu, “motion is not as finely controlled. The actuator accelerates to a more or less peak speed and then at the end of its stroke there is a sudden stop. This can result in a yanking motion that can cause the corrugated case to be dislodged or dropped altogether. With servo motion you don’t get that abrupt stop. Instead you create a high-precision motion profile that lets an actuator accelerate gently to maximum speed and then decelerate slightly before coming to a halt, which produces a much gentler, more finely controlled stop.”
There are two main axes of servo motion on the WF30. One pulls the case blank from the magazine feed and the other squares it up. Each is driven by an EMMS Servo Motor from Festo (www.festo.com), and each is governed by a CMMP Series Drive, also from Festo. A Festo DNCE Electromechanical Rod Actuator rounds out the servo-controlled package where these two main axes of motion are concerned.
Four other axes of motion having more to do with case width and height adjustments have also been improved on the WF30. Operators used to change these parameters by means of hand cranks. Now the cranks have been replaced by four MTR-ECI servo motors, also from Festo. The MTR-ECI is an integrated combination of gearbox, power electronics, and controller. The machine operator now goes to an HMI, pulls up a menu of case types, and selects the one that’s desired. The four MTR-ECI motors automatically reconfigure the machine for that case’s dimensions.
The main controller on the machine is CompactLogix from Rockwell (www.rockwellautomation.com). The CMMP drives are connected to the EMMS motors by a motor cable and an encoder cable. The CMMP drives and the MTR-ECI servo motors are connected to the Rockwell controller by an Ethernet connection that is made through an NT100 Ethernet/CanOpen Gateway from Hilscher (www.hilscher.com). The PLC connects to the Ethernet side of this gateway while the CMMP drives and the MTR-ECI motors are connected to the CanOpen side.
Because information is exchanged so quickly and readily in such a closed-loop architecture, the WF30 can automatically make continuous adjustments to unexpected variations in corrugated quality.
“One of the changes we’re seeing in packaging is an increase in the amount of recycled material being used in corrugated cases,” says Chu. “That makes the case blanks more unpredictable than if they were made of virgin materials, especially when you’re operating at higher speeds.”
The WF30’s servo system meets this challenge by reacting to the resistance that cases present when being opened. The electromechanical actuator sends information to the Rockwell controller, which compensates for variances in corrugated board material so that a consistent case-forming speed can be maintained.
“In less demanding environments, unexpected variances in corrugated can be addressed manually,” observes Chu. “But at the higher speeds this machine is designed for, these corrugated variances can have an impact on the time it takes to open cases and can affect case flow across an entire production line, especially over long periods of operation.”
As for the energy savings brought by servo-based motion, Chu calls it considerable. “When you’re running a pneumatic system, you may need a standby air compressor running, probably 24/7. With servo, you don’t need that.” He estimates the savings in energy costs at about 30% compared to a comparable machine pneumatically driven. pw