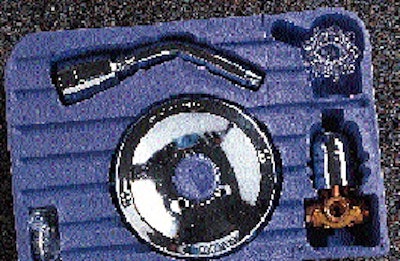
(Markham, Ontario, Canada). The Hydropulper is part of a complete molding system from Emery that also includes storage tanks, a forming unit and a dryer. This machine blends the mixture for approximately 45 minutes before piping the slurry into a storage tank. Dye is added to the mix to create the rich blue color used by Peerless. Then the tray is formed on custom tooling, similar to that used in thermoforming, according to MPP general manager John Beiersdorfer. The aluminum-based tooling has vacuum holes drilled through it. The mold is covered with a wire mesh screen-like material. The tooling is rotated down into the slurry and vacuum is pulled to draw the water and fiber. While water circulates through the screen for further processing, fibers contour to the shape of the mold. After the trays are formed, they are deposited onto a conveyor where they pass through a five-zone drying oven. Here, oven temperatures between 250° and 300°F cure the tray. The investment in tooling by Peerless proved to be an economical decision. Beiersdorfer explains, "Since the outer footprint of the trays used for Peerless are the same, we were able to use the same mold bases. To accommodate the different products they put in the trays, we simply used change parts. That way, we didn't have to build a tool for each product." Finished trays are shipped to Peerless where operators insert faucet parts into the recessed areas of the tray.