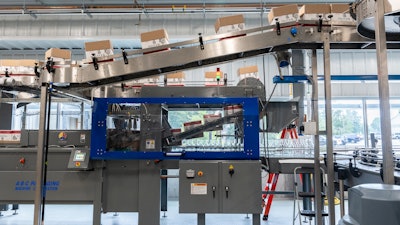
Situated in the picturesque town of Bloomington in the rolling countryside of southern Indiana, Oliver Winery has long specialized in Moscato, Sangria, Sweet Rose, and other sweet and fruit-forward wines. Sales over the past decade have grown steadily, but once the pandemic hit, Oliver witnessed the same spike in sales that many other makers of alcoholic beverages experienced. That’s what led to the recent installation of a new bottling line for 750-mL glass bottles.
“The existing line was beginning to show its age anyway,” says vice president of operations Pete Batule. “And as long as we were going to increase capacity, we wanted to make some additional improvements and upgrades. But filling speed was a key priority, and with this line we reach 12,000 bottles per hour instead of maybe 7,000 max on the old line.”
Assisting on machine selection and line integration was Prospero Equipment, which offers customized, turnkey solutions for wineries, distilleries, and breweries. All of the equipment manufacturers that Prospero represents are based in Europe.
“They served as our integrator, too, helping with the whole installation and integrating the individual machines with the conveyors connecting them all together,” says Batule. “Machine selection, design, and installation was Prospero’s responsibility.”Shown here are bottles as they enter the monoblock rinser/filler/closer.
In addition to greater capacity, what was also realized with the arrival of more automation were some ergonomic benefits. One example is in the elimination of manual de-casing bottles from reshippers. “Dumping glass from cases manually is pretty strenuous, and now it has been replaced by an automated system,” says Batule. That system, which comes from A-B-C Packaging Machine Corp., picks bottles from the case and places them on a conveyor leading to the next equipment downstream. It also inverts the now empty cases so that they rest on their bottoms as they are conveyed at an overhead level to the case packer located downstream. “There’s always a nice clean separation of bottles from corrugated,” says Batule.
Leaving the decaser, bottles are conveyed to a monoblock rinser/filler/closer from GAI. According to Batule, Oliver Winery founder Bill Oliver has a longstanding relationship with GAI, which led naturally to the installation of a GAI monoblock on this particular line.
Filtration system
Ahead of the monoblock, notes Batule, is a two-stage filtration system provided by Prospero. “Basically it’s a set of three filters with progressively finer filtration media,” says Batule. In addition to being highly effective, he adds, it’s flexible. “If we need to switch over to a new product or switch out the filters if their useful life is up, we can quickly make such changes with no waste of time. It also helps that we have a fully automated safety system and overnight CIP, which was a major upgrade for us. Getting started up each morning is much quicker.”
Bottle rinsing on the monoblock is done by a rotary module having 40 stations, after which the bottle enters a 60-nozzle rotary filler whose electro-pneumatic valves perform whatever functions the production recipe calls for. For example, if regular still wine is in production, bottles entering the filler are immediately filled. But if the product being filled is something that’s especially sensitive to oxygen, the valve can pull a vacuum to remove oxygen from the bottle and then inject an inert gas to purge the inside of the bottle. If need be the system can even do a double pre-evacuation, where a vacuum is pulled, the bottle is purged with inert gas, and then the bottle is evacuated and purged again. Multiple recipes can be stored in the Schneider Electric control system, and the operator just picks from the HMI the recipe that’s called for.
“We’ve been very pleased by this filling technology and the reliability of it all,” says Batule. “The control is so precise.”
A six-station rotary corker is next. If threaded closures are in production, the corking turret is simply bypassed and bottles move into the turret that applies closures.
Filled and corked, the bottles enter a G540 Infinity accumulation table from Garvey, a Columbus McKinnon company. By providing several minutes of accumulation, it’s just the buffer needed to allow the filler to keep running steadily should there be any downtime in the downstream equipment. “It’s basically a race track configuration, and the reason we selected it is for how gently it handles the glass bottles without letting them bang into each other,” says Batule. “Once we got it set up and dialed in, it’s been really great.”Bottles closed with corks have plastic laminated capsules applied by this machine.
Next bottles run through a rotary capsuling machine from Robino & Galandrino. Bottles having corks get a laminated plastic capsule rolled onto their necks. Bottles with threaded closures bypass this machine entirely.
At this point the bottles enter a pressure-sensitive labeling machine from Makro that applies front, back, and neck labels. Backup label rolls ensure non-stop operation, as once a roll of labels is depleted, the new roll automatically kicks in.
Vision system
The labeler also has Makro’s own vision system built into it so that if a label is missing or skewed, that will be detected immediately and the bottle will be rejected. “The inspection system also has text recognition,” adds Danny Prospero of Prospero Equipment. “So if you’re running three different flavors, for example, and all the back labels are the same except for a UPC code, if the inspection system sees the wrong UPC it will pick that up. And once you have three or four consecutive rejections, the machine will shut down automatically, saving you the cost and aggravation of having to remove multiple wrongly applied labels.”Near the end of the line the filled corrugated reshippers enter a machine that cuts the tabs holding the flaps down, folds the flaps, and tapes the cases shut.
Also onboard the labeler is a laser coder from Videojet that puts the date code information on each bottle. “It’s nice having it onboard the labeler as opposed to somewhere downstream because it makes it easier to position it for putting the code wherever you want it to appear on the bottle,” says Batule. “That’s not always as easy to do if your coding is done more or less on the fly further downstream.”
The bottles are now ready to be placed back into the corrugated reshippers in which they arrived, and this is done on a Standard-Knapp Model 939S case packer. Just downstream is an Elliott Tab Lock Separator from Massman that closes and tapes cases closed. That machine also breaks the tab holding the flaps down before plowing the flaps closed and applying the tape.
Case labeling is done by a Model 9550 print-and-apply labeler from Videojet. All that’s left is a palletizer from APE and a stretch wrapper from the same firm. PW