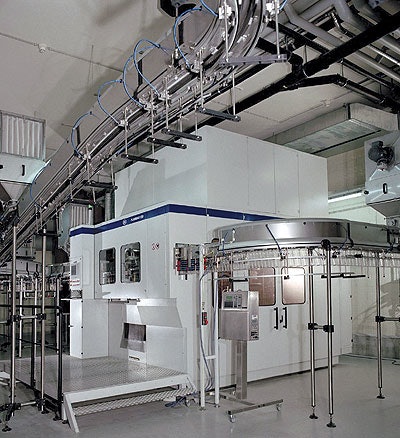
Barrier coatings continue to play a role in aseptic and ESL packaging because of their ability to keep oxygen out of plastic bottles, thus extending a product’s shelf life. While some have set aside their work in barrier coatings, others forge ahead. Sidel, for example, recently announced that one billion of its Actis-coated bottles have now been produced, filled, and sold.
Sig Holdings also remains active in the coatings game. Its Plasmax technology, developed jointly with Schott HiCotec, offers a combination of clarity, barrier, and 100% recyclability. It’s viewed so favorably at Sig headquarters in Switzerland that the firm recently spun off a separate business unit called Sig Plasmax to focus squarely on selling Plasmax installations.
The technology behind Plasmax is called Plasma Impulse Chemical Vapor Deposition (PICVD). Through a combination of microwaves and vacuum, it coats the inside of a PET bottle with a thin, transparent layer of glass. Food Contact Notification 000329, issued in July of 2003 by the U.S. Food & Drug Administration, clears Plasmax for use in food and beverage packaging in the U.S., says Sig. Also giving Plasmax a nod of approval is Petcore-PET Container Recycling Europe, a nonprofit organization that fosters the use of PET containers and facilitates PET recycling. Petcore early this year granted Plasmax a full recyclability endorsement.
The first Plasmax prototype has been tested at Bischofszell in Switzerland. A Plasmax 12D unit went into production in June of 2003 and has been coating PET bottles in various sizes from 0.4-to 1-L at speeds to 10ꯠ/hr. The coated bottles are then aseptically filled with juice and sold through the Migros chain of stores.
Other Plasmax coating systems are running commercially in Japan, says Promeet Nag, head of sales and marketing at Sig Plasmax. He also indicates that certain U.S. companies have expressed interest, though naming them, he says, “would probably rock too many boats” at this particular time.
Nag also says that a certain amount of process improvement is still underway where Plasmax is concerned. “We’ve made tremendous strides since the first machine went into the Bischofszell plant,” he notes. “But we’re still optimizing the process and the machine.”
See the story that goes with this sidebar: Aseptic and ESL packaging keeps evolving