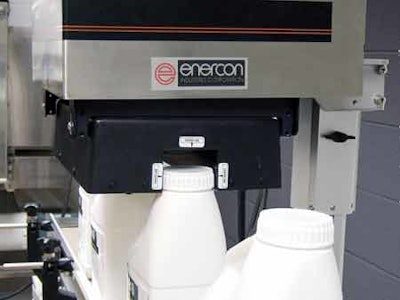
MGK, a manufacturer and packager of pesticides in Golden Valley, MN, was struggling to seal their 63-mm caps using a flat-head induction sealer with a universal head. To seal the caps properly, the operator had to pivot the sealing head into position and line up each bottle with an imaginary line so that it passed diagonally underneath the sealing head. Lining up the head and the cap proved challenging and time consuming. The process was too operator-dependant and resulted in inconsistent seals. “You'd think everything was fine, and you'd move on to another cap,” says Grant Getty, MGK's production manager, “then you'd spend all this time trying to get it to work again.”
MGK turned to Enercon (www.enerconind.com) to design a sealer that would accommodate their 63-mm cap and provide a consistent seal. Rieke Corp. (www.riekepackaging.com) supplies the threaded injection-molded polypropylene caps, which have inner seals made of coated polyester film bonded to aluminum foil, which is wax-bonded to white lined pulp board. As the caps run under the sealer, the heat melts the wax that holds the foil liner to the pulp board and bonds the foil liner to the lip of the container. The pulp board remains in the cap, allowing the bottles to be resealed once the foil is removed.
Typically, a flat sealing head is used to seal a 63-mm cap because tunnel or channel sealing heads do not ensure an even heat pattern on a cap that large. However, after numerous laboratory tests, Enercon's engineering team determined that a flat sealing head would underperform due to the cap's unique geometry. The profile of the cap features a raised crown, which creates a gap between the bottom of a flat sealing head and the location of the liner. The air gap between the top of the container and the bottom of the sealing head should be 1⁄8”; therefore, some of the sealing energy would be lost in this additional air gap.