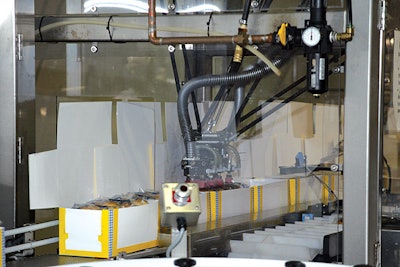
Since opening its breakfast-sandwich packaging facility in Dickson, TN, back in 1989, Tennessee Quality Foods, Inc., has frequently upgraded its packaging equipment to remain efficient.
Last summer is a good example. That’s when TQF, a division of Madison, TN-based Odom’s Tennessee Pride Sausage, Inc., replaced older cartoning equipment with an HS2/60 carton erector, LJ-SRT robotic carton loader, and Tri-Liner carton closer, all from Bradman Lake.
“When we considered cartoning equipment, Bradman Lake offered what we were looking for,” recalls Ed Scarbrough, plant manager at the Dickson plant. “The machinery was competitively priced, it doesn’t take up a lot of floorspace, it’s high-quality equipment, and it’s easy to maintain.”
The decision to purchase the cartoning machines from Bradman Lake was also based on TQF’s previous experience with that supplier’s carton-erecting and -closing machines.
A key benefit of the new units, Scarbrough says, concerns changeovers. “With these machines, we can change them over in 10 to 20 minutes, whereas it took 30 to 40 with the older equipment. That time difference is very important because if we have a line down for a changeover, it means that line’s not running production.”
Upstream functions
The 65ꯠ-sq’ facility operates five days per week on two daily eight-hour shifts. “We have four packaging lines, all of which can produce any of the 25 different line items we run,” says Scarbrough. All of the eggs, sausage patties, and cheese products are prepared at other Odom’s Tennessee Pride plants, then individually quick-frozen and shipped to the Dickson facility where they’re stored in a warehouse freezer. A local baker supplies fresh biscuits. Product is brought to a 50º cool room for packaging at speeds between 180 and 200 packs/min.
All four lines are equipped with a flow wrapper from Campbell Wrapper. These machines range in age from six months to six years. All four wrappers have a 20’ flighted conveyor. On each side of the conveyor are stations where workers assemble the different food products and load them onto a conveyor that carries the 3.2-oz breakfast sandwiches into a curtain of 2.6-mil film from Alcan Packaging. The polyester film is printed flexo in one color with Odom’s logo and heating instructions. The film also has a polyethylene sealant layer.
“All of the packs are gas flushed,” says Scarbrough, “which gives us a shelf life of 55 to 60 days for products sold through the refrigerated chain, and six months for frozen sandwiches. On the Campbell machines, we introduce a blend of nitrogen and carbon dioxide to eliminate oxygen.”
The Campbell machines heat seal the film and a knife cuts through the seal area, separating the leading packed sandwich while creating the leading seal for the subsequent pack. TQF can set the machine to cut between each sandwich pack, or to cut between every other seal for two-packs.
Before adding the four new Campbell Wrapper machines, Scarbrough says TQF had used “wrappers from when we opened the plant in 1989 that just didn’t give us the versatility we needed with the different products. There were high maintenance costs involved, and the speed and throughput were about 50 percent of where we are right now.”
Also, he says, changeovers on the previous equipment were a lot more involved. “There were more than 20 sealing heads on a carousel. The new wrapper has only one rotating head on it. It takes standard open-end and boxed-end wrenches and sockets to do the changeovers. And we can change over from one product to another in 10 to 20 minutes. Before it was 45 minutes to one-and-a-half hours,” says Scarbrough.
Cartoning flexibility
On one of its four lines, TQF employs a bagger that wraps 10 twin-packs in a printed bag. Each of the other three lines is outfitted with a Bradman Lake machine. One of the lines uses right-angle Bradman Lake carton-forming and -closing machinery. The two newer lines employ straight-line equipment.
The newest of the two lines with straight-line equipment employs an HS2/60 carton erector. It sends erected cartons on a conveyor to the Bradman Lake LJ-SRT robotic product collator and loader. Formed, empty cartons accumulate in a set of servo-driven side-running belts. Cartons are supplied by Caraustar, in 17- and 22-pt versions. All cartons are printed offset in six colors. Next, cartons are transferred into a second set of servo-driven running belts that are computer-programmed to advance cartons accurately to predetermined positions for top loading. Filled cartons are automatically released on a discharge conveyor to a carton closer that uses hot melt glue to seal cartons shut.
“We were just looking for something that was dependable and would do what we wanted it to do,” says Scarbrough of the cartoning equipment. “But we did eliminate some labor costs.” In fact, he says that the machinery helped to free up three people per line.
Sealed cartons are conveyed to an automatic case packer on one line. The other three lines are packed manually. “Last year we put in automatic case packing and palletizing on this one line,” says Scarbrough. “We have plans within the next two to three years to automate the other three lines.” One line is automatically palletized, the other three are manually palletized prior to stretch wrapping on an older machine.
Either 12 or 24 cartons are packed into a case. These are shipped frozen from the Dickson plant by contract carriers to distribution centers primarily in the eastern half of the United States. At the store level, some sandwiches are sold refrigerated, some frozen.
“We’ve been very happy with the Bradman Lake equipment,” says Scarbrough. “They’re good people to work with, and they provide service and technical support.” As for the equipment’s return on investment, he concludes, “it’s been anywhere from 18 to 24 months on all the equipment, and our newest line is dependable, user friendly to operators, requires little space, and allows us to handle additional production.”