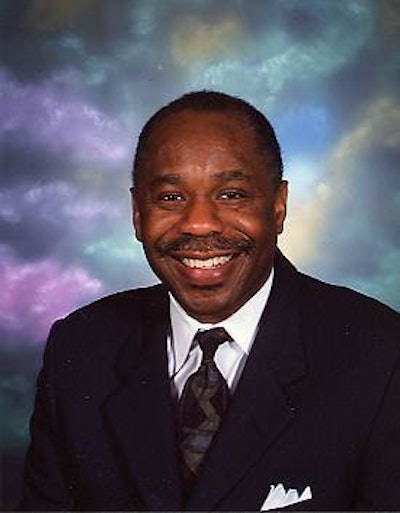
Water vapor transmission rate (WVTR), also known as moisture vapor transmission rate (MVTR), measures the permeation of water vapor through a membrane—for this discussion, that membrane is a flexible packaging material. Permeation can occur inward or outward, meaning that the interior of a package can gain moisture or lose moisture. Either scenario can be harmful, depending on the product category, as exemplified by foods, beverages, pharmaceuticals, medical devices, personal care items, and cosmetics.
Rather than detail the harmful effects, suffice it to say that dry products need to stay dry and wet products need to stay wet. Directly affected are expiration dating and shelf life to be sure, but ramifications extend throughout the supply chain, particularly for inventory management.
In the vast majority of flexible packaging applications, moisture barrier is provided by a polyolefin, either polyethylene or polypropylene. Their moisture barriers range from fair to good, however they are achieved cost effectively. High-density polyethylene (HDPE) is better than low-density polyethylene (LDPE) and oriented polypropylene (OPP) is better than polypropylene (PP), with OPP and HDPE being close in performance. But PP beats LDPE by a wider margin.
An understanding of how the polyolefins compare helps in understanding WVTR. First, such an understanding establishes performance expectations, even before any testing and calculations. It also shortcuts the list of candidates when excellent moisture barrier is not needed, as provided by aluminum foil, metallized film, and PVDC. Similarly, it facilitates decision making when a package is a monolayer, coextrusion, or lamination in which the polyolefin’s role is to provide moisture barrier as opposed to being a tie layer. In a competitive environment that emphasizes speed-to-market, all possibilities for streamlining should be used.
The international standard for reporting the results of WVTR testing is grams per square meter per 24 hours: g/m2/day. In the U.S., typically, it’s grams per hundred square inches per 24 hours: g/100 in2/day. In both standards, the lower the rate, the higher the barrier. And each standard has its expected range. For example, the expected range for the international standard is 0.001 to 2400 g/m2/day. A rate expressed in one standard can be converted to a rate in the other standard. There is an inherent element of imprecision (however slight it might be) in the conversion.
During permeation, moisture collects on one side of the material, goes through it, and emerges on the other side. That’s a simplistic but accurate description, albeit one that belies the complexities of the theory of permeation. The process proceeds at a rate affected by temperature and relative humidity (RH) such that, for test results to be comparable, those two variables have to have been controlled. One of many possible standardized pairs of test conditions is 100°F (37.8°C) and 90% RH. The importance of test conditions does not reside solely in their standardization, rather the conditions should be relevant to the conditions that a given product is expected to encounter within its supply chain.
Permeation is affected by additional factors. One is thickness—a thicker material provides more barrier than is provided by its thinner self. Logical and intuitive, yes. Still, it doesn’t eliminate certain tradeoffs, such as between competing materials that provide acceptable barrier, but at different thicknesses and at different costs. Another factor is molecular makeup. It’s understandable to feel beset by talk of crystallinity, density, chain length, chain branching, orientation, etc., but take heart. They all affect the paths water molecules travel through and out of the material. The more tortuous the path, the slower the permeation and the lower the WVTR. Conversely, the more straight the path, the faster the permeation and the higher the WVTR.
As for the conducting of WVTR testing, standardized protocols are published by various organizations, such as TAPPI, ISO, and ASTM. Since they share the same objective, discussing ASTM will serve for the others in this column. ASTM F1249-20 is applicable to barrier flexible packaging, whether film or sheet and whether monolayer or multilayer. The barrier flexible packaging test sample is sealed between a wet chamber and a dry chamber. Moisture passes through the material, driven by the pressure differential created between the two sides. A modulated sensor measures the passage, from which a WVTR value is calculated.
It sounds so scientific and matter-of-fact, but that perception is in disguise of certain realities. The ASTM F1249-20 abstract acknowledges as much, to wit: “Values for water vapor permeance and water vapor permeability must be used with caution.” That’s sage advice, cautioning that matters are not necessarily absolute. It’s consistent with the bedrock idea that packaging requires a systems approach, consisting of components and their tradeoffs.
In illustration, the calibration of the equipment plays a role. So too, does the attention and care exercised by the test conductor. Those realities are to be kept in mind, especially since most packaging users don’t conduct their own WVTR testing. Instead, they rely on packaging suppliers (converters) and laboratories that specialize in such testing.
The requirement, “all other things being equal,” rarely (if ever) applies to WVTR, accounting for why the testing is complex, time-consuming, and challenging to interpret. None of that, however, subtracts from its importance. PW
Sterling Anthony, CPP, consults in packaging, marketing, logistics, and human-factors. A former faculty member at the Michigan State University School of Packaging, his contact info is:100 Renaissance Center, Box-176, Detroit, MI 48243; 313/531-1875; [email protected]