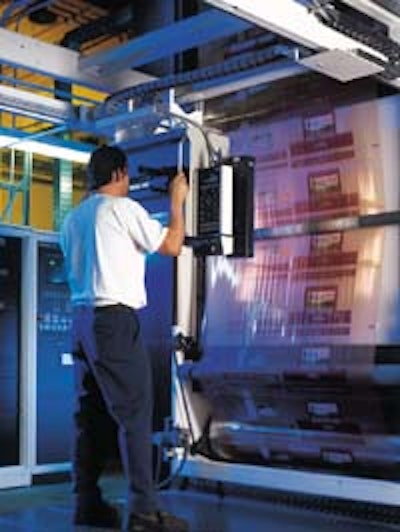
Unlike the case with many stock market investors, Friedman Bag Company knew its investment in a new flexographic printing press would reap a handsome return. Installed last summer to replace three aging presses, the Windmoeller & Hoelscher (Lincoln, RI) Astraflex® central impression press is doing exactly what Friedman Bag expected.
Before purchasing the press, the Los Angeles-based film and bag manufacturer/converter evaluated the fundamental benefits its prospective investment would yield. Among them:
• Eight-color printing capability compared to only six previously. The press can print four process colors and four line colors. The extra color stations would not only prevent the loss of at least one key customer, but also allow Friedman to pursue a wider variety of print jobs.
• Printing speeds of up to 1ꯠ’/min, three to four times the speed of the three older presses.
• Quicker order production thanks to faster run speeds and setup time.
• Labor savings of four people/shift compared to previous presses.
• A three-year payback.
“The Astraflex replaced three older flexo presses,” says Jeff Sway, Friedman’s vice president of marketing and services. “Two of them were four-color machines; one was a six-color press,” he says of the presses that were sold by the company.
“Those machines were slow, running 200 to 300 feet per minute,” he continues. While that pace was unacceptable, speed wasn’t the overriding reason why Friedman sought a new press.
“What we see today, whether it’s on the Internet or in print, are explosive color graphics, and that’s where the printing business continues to go,” Sway believes. “We wanted the opportunity to produce in eight colors and improve the quality of our print runs.” Why the Astraflex?
“We looked at a variety of presses before we made a final decision,” recalls Jim Watts, general manager for the converter’s Polyethylene Division, which uses the new press. Textile bagmaking represents the company’s other primary business.
“W&H offered us a longer repeat length [47”] on this press than some other manufacturers did,” he notes. “Normally, on a central impression press the repeat is 28 inches at most. We haven’t had a job requiring that full length yet, but we have done some jobs that were 42 inches long.” Watts adds that the press provides versatility not only for printing PE film, but also for the materials used for textile bags.
Retains ‘Giant’ job
Had it not expanded its printing capabilities, Friedman Bag may have lost at least one significant account: Potandon Produce LLC. The Idaho Falls, ID-based private “spin-off” company from Pillsbury “bought the marketing rights to the Green Giant® Fresh name on potatoes and onions,” explains Mel Davenport, Potandon’s vice president of operations. He tells Packaging World, “We worked with Friedman Bag at Pillsbury before we took the company private.
“Potandon has been in business for more than five years,” Davenport continues. “And it was natural to continue using Friedman, if they had the right press capabilities. They used to have only six-color capabilities.” Newly designed graphics, however, required eight colors.
Davenport says, “We didn’t demand they [buy the new press], but we were honest with them in letting them know that beginning this year, we were going to require seven- or eight-color bag printing. They needed to have that capability.”
For Potandon, film is produced in thicknesses from 1.35 to 2 mils, depending on product weight. “Friedman supplies about 30 different bag types for our potatoes and onions,” explains Davenport.
“We specify the film characteristics, down to the punch holes,” he says. “The vent holes are added to the bag, and they’re critical because the potato is still breathing. The holes fit into the graphic pattern on the bag. All the bags we receive from Friedman are wicketed. They ship bags primarily to our contract packagers, though we also do some packaging. We began using bags from Friedman’s new press in February.”
Film extrusion first
The 52”-Wide press was added last July. It runs three shifts per 24-hour day, six days a week. While the press accommodates various flexible substrates, Friedman presently uses it for the low-density PE blown film it produces on four extruders. Resin is procured primarily from Eastman Chemical (Kingsport, TN) and Chevron (Houston, TX). The bagmaker sells bags mostly for produce applications.
Potandon supplies artwork via computer files to Friedman for making color separations. Once Potandon approves the materials, printing plates are made. Plates are mounted to plate cylinders and are automatically positioned and changed via W&H’s Portalift® robotic roll change system.
“Once we mount the photopolymer plate onto the cylinder, the cylinder is staged on a Portalift cart, then loaded onto the press,” explains Friedman’s Watts. “We’ve probably cut our setup time in half with the robotic system, and as we get more familiar with the machine we think that will improve even more,” Watts believes.
Clear the decks
The Astraflex CIP is equipped with eight printing decks, with four decks to each side of the cylinder. The cylinder and decks are located at the “front” of the approximately 85’-long machine. Each deck includes plate cylinder, anilox roll, between-color drying boxes and a patented W&H doctor blade chamber.
“Each of the decks has a reverse-angle doctor blade, which helps in our printing process by minimizing the ink laydown,” explains Watts. “That not only gives us a better ink laydown, but also [creates] ink savings,” he says. Friedman uses water-based inks for all printing jobs.
“Normally, we lay down white first,” says Watts. “Not only is it part of the design for Potandon, but it also creates a background for things like the UPC code and nutrition information.”
After each color, he says, “there’s a between-deck dryer that’s adequate enough to allow us to lay down the next color. Potandon bags are seven-color jobs.” After all colors are printed onto the film, the material passes through an overhead drying tunnel.
“With the improved dryer systems on this press, we’re able to attain speeds much faster than we could on the older equipment,” Watts notes.
After drying, the film continues through a web cutoff system to complete the process. Before rewinding, a traversing web scanning system is often used by press operators to visually inspect areas on the film for print quality. Film rolls are automatically removed with the Portalift system, which stores the printed roll on a cart and places a new rewind roll into place. Printed rolls are transferred to another area in the plant for converting operations.
“After printing we send the film to our converting department where we make it into wicketed bags for automated packaging machinery, and punch in ventilation holes,” explains Sway.
Speed, labor advantages
Listening to Sway, it’s understandable why Friedman is satisfied with the Astraflex. “It’s good for long runs because of its speed. We can create one million impressions in five or six hours, depending on the job. At a minimum, this press runs three times faster than our former equipment, so it’s doing at least the work of three former presses. The print speed and efficiency allows us to provide quicker turnaround time for delivering orders to our customers.”
The press, Watts says, “can run at about 1겨 feet per minute with solvent-based inks, but we use water-based inks and usually run it at about 850 to 900 feet per minute, though we’ve got it up to about 1ꯠ feet per minute at times.”
Because only two people are needed to run the Astraflex, Friedman was able to lower its labor costs. “Part of our justification in buying the press was lowering labor costs,” says Sway. “We needed two people, a pressman and a helper, for each of our three older presses. So in terms of production, we went from six to two people per shift.”
Another benefit is the training supplied by the press vendor. “W&H has provided considerable training and technical support,” says Watts. “We can’t say enough about how helpful they’ve been. I’m not so sure that we haven’t exceeded the amount of training time we were originally allocated.”
Quick changeovers
While Friedman praises the new press for its speed, the company is also enamored with Astraflex’s quick-changeover capability. “We operate the press with two people, and we do three or four changeovers a day,” Watts estimates. “Two people can perform changeovers in less than two hours. That’s important because more and more customers are going to shorter runs to cut down on their inventories and meet just-in-time orders.”
Sway and Watts also praise the press’s Turboclean® computer-controlled wash-up process that cleans the system from ink supply to decks, anilox rolls, doctor blade chambers, pump stations and connecting hoses. They also like the fact that despite being a larger press, the Astraflex saves about one-third of the space used by the three presses it replaces in Friedman’s 100ꯠ sq’ Los Angeles plant.
Adding up all of the press’s advantages, Sway and Watts say Friedman Bag is still on track to meet its original three-year payback estimate. “That’s probably a shorter payback period than most people would look at,” for such a press, Watts contends.
New markets
At the summit of these advantages, however, is the color quality the Astraflex delivers. “While this is an eight-color press, we can make printing plates and use screens so that it looks like we’re printing 11 or 12 colors,” Watts believes. The press’s improved color quality hasn’t gone unnoticed.
“Customers have said everything from ‘this is some of the best printing we’ve ever seen on this particular application,’ to ‘if you didn’t have [the press], you would have lost my business,’” Sway explains.
Potandon’s Davenport says, “The new press at Friedman Bag prints finer details, and the colors and print definition are much clearer than they were with their older presses.”
With the Astraflex, Friedman plans to move into new sales markets. “The press has already gotten us into bags for grass seeds, specialty home and garden fertilizers.”
With the press, Friedman Bag is also considering printing more complex barrier films from outside vendors. Sway says snack food pouches, prepackaged salad bags, citrus fruit bags and coffee bags are all possibilities.
“We’re evaluating many new markets, as well as working with our current customers to expand their bag graphics to further benefit their products,” Sway says. “Without this press, we couldn’t get into some of these areas. And we could have lost [Potandon’s] business had we not been able to print in eight colors.”
Friedman expects to add a new press in the future. And W&H’s support on this machine carries considerable weight in Friedman’s decision. “They know we’re going to buy another [press], so they want to be in line for that one,” says Watts. “And we’ll probably go with a wider press next time.”
That press may have 10- or 12-color print capability. “We used to think that eight colors was state-of-the-art when we could only print six colors,” Watts recalls. “And now other companies [printers] are introducing 10 or 11 colors. We don’t have print requirements for that yet, but to be ready for the future, we’ll certainly look at that possibility.”
In a hurry? Request more info via Web-based reader service by clicking on the reader service number.
Or you can jump right to their Web site.