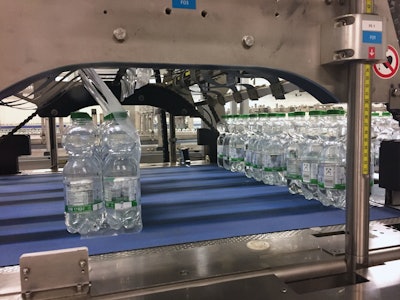
Germany’s Altmühltaler Mineralbrunnen GmbH produces bottled mineral water brands for large German retail chains, hotels, and restaurants. The company has several facilities in Treuchtlingen, Central Franconia, and Baruth, a small town near Berlin.
The newest line in its Treuchtlingen facility, dedicated to 500-mL PET bottles of still or carbonated water, replaces a line that topped out at 42,000 bottles/hr. “It just wasn’t enough throughput,” says Plant Manager Andreas Wiedemann. He adds that the new line, running since 2017, provides 56,000 bottles/hr.
Equipment from two large producers of beverage filling and packaging systems were carefully analyzed before the firm selected Krones as its turnkey provider. “Reliability of the equipment selected, of course, was a key consideration, as was overall value,” says Wiedemann. “But throughput was near the top of the list, and we selected the machinery suppliers we did because this line reliably provides just what we need.”
Anchoring the filling and capping portion of the line is a 168-valve Krones Modulfill and a capper. But the line really begins upstream with three Krones Contiform 324 stretch blow molding machines, each having 24 stations. Altmühltaler also injection molds its own PET preforms, though it’s done in a separate facility.
Overhead air conveyors leading from the blow molding area bring bottles to the Modulfill. Exiting the filler the bottles pass through a rinsing device since some of the flavored products might have a sugary residue on the exterior. Then a Krones Flowliner divides the bottles into two lanes. From two lanes the bottles gradually broaden out more until they are in a conveyor section that is about 4 ft wide.
Eventually, after a sizeable stretch of conveying that provides useful accumulation space should any of the downstream equipment go down, the bottles are single-filed by line pressure. Labeling is next, performed by a Krones Solomodul. A roll-fed glue-applied system, the labeler relies on a Nordson ProBlue4 hot melt unit for adhesive. The machine is equipped with a total of four label unwind stations. Two are in operation at any given time, each applying a label to every other bottle. The other two are loaded with fresh rolls of polypropylene labels so that downtime is minimized when rolls are depleted.
When bottles exit the labeler, they pass through a D-Series Solution laser coder from Domino. It puts lot and date code information on the shoulder of each bottle.
Next in the line is a Krones multipacker that collates bottles into groups of 18 bottles nine-across and 2-deep. In this orientation the bottles move through a station in which they are enclosed in shrink film. Immediately afterward, the 18 bottles emerge from a shrink tunnel transformed into tightly unitized 6-pack units.
Fork in the road
At this point the six packs can go one of two ways. If a customer wants shrink-wrapped six packs in a corrugated tray, the six packs go to the Krones Variopac Pro tray packer before moving to the Krones Modulpal palletizer. The Variopac puts four shrink-wrapped six-packs into a corrugated tray, which then is conveyed into the palletizer. But if the customer doesn’t request a corrugated tray, the shrink-wrapped six-packs bypass the tray packer and head for palletizing.
Preceding the Modulpal palletizer is a Krones Robobox grouping system. It uses two tripod robots with parallel kinematic design to take the film-wrapped six-packs from the single-file orientation in which they arrive and disperse them to the left or right—occasionally turning one 180 deg—until they’re in the pattern that’s required for palletizing.
As soon as 36 six-packs have been so manipulated, the entire group is squared up into a tight unit and pushed forward onto a reciprocating loading station. This loading station advances to a position just above the pallet. Then its shutter opens so that the layer can settle onto the layer that preceded it. The loading station then returns for its next pallet layer as an automated arm picks a paperboard slip sheet and places it on top of the layer of bottles that has just been placed on the pallet.
As soon as seven layers are in place on the pallet, it’s conveyed forward to a Krones stretch wrapper. It applies stretch film from two separate rolls simultaneously, which shortens the amount of time needed to get the desired amount of stretch wrap on a pallet. The final step in the process is application of a pallet label by a thermal-transfer print-and-apply unit from Logopak.
Small footprint
Though the new line operates at a considerably higher speed than the one it replaced, it occupies pretty much the same footprint as its predecessor. So Altmühltaler didn’t need to add onto its manufacturing facility to get the additional throughput it required.
As for operators required, just one is stationed at the wet end, one at the dry end, and two at the blow molders.
On the day of our visit to Altmühltaler, the 500-mL bottles in production were on their way to stores in the Aldi supermarket chain across Germany. Standing near the end-of-line palletizer and looking back at the steady flow of bottles moving smoothly through the line, Wiedemann offered this answer when asked what stood out about the line. “The schedule for removing the old line and replacing it with the new was just two months. And that included renovating the floor. Around 40 Krones service technicians were on the job to get it done.”
New collaboration platform
The new line at Altmühltaler is the first one on which the Krones Syskron collaboration platform known as Share2Act is operating. A mobile app, Share2Act is a network for all employees, machines, and IT systems included in production. It provides a platform where information is displayed on hand-held tablets so that all stakeholders can discuss and process that information together. Especially suitable on packaging lines run by multiple shifts, it’s a new way to streamline sequences, shorten communication channels, and reduce downtimes.
“Important information reaches not only me but the maintenance manager very quickly,” says Wiedemann. “So if a problem does occur, we can solve it much faster, which in turn saves time and money.”