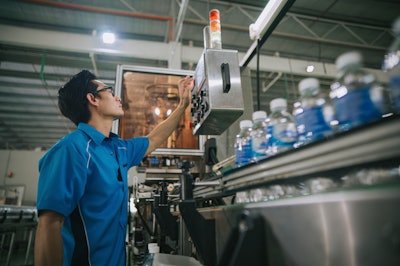
The packaging and processing industry’s rapid advancement has left it grappling with an issue common across technical industries, nonetheless formidable—a skills gap.
As facilities move toward automated machinery, the bar is raising for worker knowledge and competency on the plant floor. This technology is replacing the monotonous jobs of old, and today’s ideal worker is “not a person that stands and puts widgets together as much as it is somebody who can operate equipment that does that,” says Nancy Wilson, CEO at Morrison Container Handling Solutions.
These technology-based manufacturing jobs can make the workday more engaging and satisfying for workers, but it also requires a specialized skillset that comparatively few workers currently can claim. This can be a factory-constraining problem.
Companies are struggling to find and retain workers with this skillset to the tune of 696,000 open manufacturing jobs over a three-month moving average, according to PMMI Business Intelligence’s 2023 report, “Guidance in an Uncertain Economy: Gauging the Risks Going Forward 2023-2024.”
Conditions are improving alongside lowering overall unemployment, as manufacturing job openings are at their lowest point in 23 months. But the current figure still more than doubles the average 320,000 openings seen between 2010 and 2019.
The challenge for companies lies in “being able to reeducate or upskill” workers previously unfamiliar with advanced technology, “as well as trying to find new workers to recruit into the plants,” Wilson says.
Bridging the packaging skills gap at the company level
Morrison bridges the skills gap at its facility with a heavy focus on career development for both current and prospective employees.
The company brings young and aspiring engineers in-house through its internship program, allowing them to “feel what it’s like to work at a company like ours and actually have a real intern job and create real products,” Wilson says. In turn, it allows Morrison to see these students’ performance in a real-world setting before making a full job offer.
The company also attracts workers from all walks of life through its apprenticeship program, created in partnership with Purdue University Northwest (PNW) and Chicago-based non-profit Opportunity Advancement Innovation in Workforce Development (OAI, Inc.).Morrison's apprenticeship program with OAI allows workers from outside the industry to get industry training and experience.Morrison Container Handling Solutions
Apprentices can join from outside the industry and start without previous knowledge of manufacturing or assembly. They split time between basic electrical and mechanical training at PNW and getting hands-on experience working at Morrison.
The program is relatively new with only two graduating classes having matriculated, but apprentices have included younger folks interested in the industry, a military veteran, and one of the company’s own employees who “had been working with us in more of a stockroom position, and wanted to get into mechanical,” Wilson says.
“The more you can make an impact on the world, the better you feel about it,” Wilson says of Morrison’s programs. “Education matters, and it doesn’t have to be four-year, but any education that helps people move on and get better is important.”
Outsourcing career development
For companies without the resources to start programs like those at Morrison, training doesn’t need to be developed in-house.
The Institute of Packaging Professionals (IoPP) makes career development accessible for any motivated individual or company as an education and networking-focused organization.
The organization offers a Fundamentals of Packaging Technology course in person or online, “to get people up to speed on the terminology, on the lingo that packaging people speak,” says Jane Chase, IoPP executive director. “We’re seeing a lot of technical people coming in, doing that, and getting into the packaging industry. We can’t produce enough of them.”
The Fundamentals course blankets the industry, but IoPP couples it with courses focused on more specific topics like medical device packaging, packaging machinery, and starting this fall, project management.
“I think that’s the biggest gap that [companies] are seeing is really the project management,” Chase says. “[Packaging students] have the technical skills, but do they really know how to come into an organization, understand who does what, and figure out how the organization operates in order to get projects done?”
Those up for the challenge and eager to earn the pedigree can also apply to become a Certified Packaging Professional (CPP) through IoPP.
CPP candidates must meet qualifications like having at least six years of packaging or closely related experience, as well as IoPP membership. They then complete a 150-question exam that covers packaging machinery, materials, and technology. They must then choose one additional requirement between a narrative exam, a resume of activities, writing a paper on a technical or management topic, or submitting proof of having acquired a patent within five years prior, the IoPP site explains.
“That certification is something that’s helping to close the skill gap, particularly internationally,” Chase says, as the certification acts as a de facto degree in countries that don’t have robust packaging school networks. “And in the U.S., it’s really bringing more individuals into the packaging industry by giving them that extra leg up.”
The organization collaborates with companies to help employees get that leg up, too. IoPP has licensed its training with both small companies and larger corporations including Mars Wrigley and PepsiCo.
PepsiCo sends 25 engineers through the program each year to earn the CPP badge, and after five years, “they have about 125 certified packaging professionals,” Chase says. “They’re not forcing everyone to do it. It’s seen as a ‘I got picked for this year’s class, I get to do it.’”
Working under these internationally recognized standards clears some confusion and adds accessibility to the industry, as "everyone has the same baseline of knowledge,” Chase explains. “A packaging engineer in Houston talking to someone in Southeast Asia has that same base level of knowledge, same vocabulary, same way of approaching packaging.”
Operator-friendly machines for easy training
Training opportunities like those offered at Morrison and through IoPP help to demystify the complicated machinery of today’s industry, but the steep learning curve for those new to packaging remains a major hurdle in sourcing qualified workers.
Amid today’s workforce challenges, OEMs have a responsibility to make the transition to and maintenance of these machines as seamless as possible for consumer packaged goods companies (CPGs).
Morrison makes the transition easier for CPGs with a “do no harm” principle during install.
“We don’t destruct anything that’s there, so it can always go back to the way it was, if need be,” Wilson says.
The company also considers daily operation and troubleshooting during development.
“It goes way back from the old stories about automobile companies, that you had to take the engine out to change the oil because of the tight design,” Wilson says. “We really try to make sure that we’re thinking about the what-if scenarios and do some failure testing as well.”
OEMs shouldn’t just drop equipment off and leave the CPG wondering how it works, either.
Morrison always provides training upon installation of a new machine, and offers a preventative maintenance plan for continued service, but Wilson says companies often turn down the extra assistance.Morrison offers preventative maintenance agreements to help keep the line running after the initial sale.Morrison Container Handling Solutions
Couple that with the high turnover in today’s labor market, and “the training that you did could’ve been last week, but it walks out the door,” Wilson says. That’s especially true for contract packagers, as they use often use temporary workers on the line.
“You really have to think about designing things that are intuitive for operators,” Wilson says, “so when a company does have turnover, if remaining operators weren’t trained on the equipment, it’s more intuitive or it has instructions that are embedded into it.”
Culture counts
As packaging and processing companies clamor for skilled workers, it’s a seller’s market for packaging professionals.
Workers with the skills and knowledge needed for the industry enjoy a variety of available opportunities, describes Asma Parveen Majeeth, associate application controls engineer at Signode Industrial Groups and recent PNW graduate.
“I had gotten several interviews within a month of searching for a job,” Majeeth says, noting that she had earned a job offer in the industry before completing her mechatronics, robotics, and automation engineering degree.
If these workers have such a variety of opportunities, companies will need to offer a work environment that stands out from the rest.
That can come down to a factor as simple as pay. For recent graduates in particular, companies need to offer salaries that compensate for the time and money spent in school, or that are at least higher than what’s available in non-technical jobs with no degree requirements, says Majeeth.
“Having gone through school and gotten a professional degree just for a bare minimum is not fair to us,” she says. “Employers should understand that even though we don’t have enough to offer right off the bat, we have a lot of potential and the background knowledge to contribute to the company’s growth sooner.”
A work environment amounts to much more than pay, though. A positive workplace culture can go a long way in attracting and retaining employees.
“It’s about having an environment where people want to stick,” says Wilson, whose team includes workers who have spent upwards of 30 years at Morrison.
“We spend way too many hours together to not be with people we want to be with, and so I think it’s really important that you have a really strong, solid company culture that is supportive of employees, that recognizes each other with respect,” Wilson says.
A sense of fulfillment and continued challenge can also motivate workers to stay.
“The biggest thing that companies can do for development is really challenging their employees, giving them new opportunities to do different things, not just bigger versions of the same thing,” says Chase.
Chase worked for 10 years at SC Johnson Wax but spent those years jumping between roles as a quality engineer, an operations manager, and a member of the packaging R&D team.
Taking on new challenges within the company equipped Chase with the “understanding of how you fit into the hierarchy and the culture and how you’re contributing to the bottom line. If a company can make you feel that, those are the companies that you’re going to want to stay with and grow with,” she says.
The younger generation is especially interested in a sense of fulfillment and contributing to the world through work, Chase says after interacting with students at events like Clemson University’s Packaging Jamboree. “Sustainability is the big vision of what they see now, where they feel like they can get out and contribute out of the chute,” Chase says.
These students and modern workers in general gravitate toward sustainability-driven or mission-oriented companies, Chase says, citing beauty brand Aveda and her old employer SC Johnson Wax as examples.
Providing this sense of fulfillment, along with a healthy work culture and growth opportunity, will be crucial as companies tap into the pool of emerging professionals.
Education to cultivate a skilled workforce
Higher education and its potential to develop tomorrow’s packaging workforce cannot be understated, but it is relatively challenging for companies to influence, being a third party outside the plant floor. That doesn’t mean it’s impossible.
Morrison promotes education as a skills gap solution through its partnership with PNW, where the company helped to open a mechatronics engineering lab in 2008. The university later opened the country’s first mechatronics engineering technology bachelor’s degree program.
“It’s a combination of a mechanical engineer and an electrical engineer in one that can understand automation,” Wilson says. “So that program combines those two curriculums into one degree.”
The relationship goes both ways, as PNW’s mechatronics program connects with the industry and integrates real-world applications as a major factor in its curriculum, describes Maged Mikhail, PNW professor of mechatronics engineering technology.
That includes internships and co-op opportunities with local companies, hands-on projects that integrate donated machinery from Rockwell Automation, LinMot, Inc., and Econocorp, scholarships supported by the PMMI Foundation, and sparking an interest in pre-college students through summer manufacturing camps and visits to PACK EXPO International, IMTS, and other events, Mikhail says.Purdue Northwest recently hosted a robotics summer camp for middle and high school aged girls, allowing them to work with end-of-arm tooling and grippers.Maged Mikhail
This multifaceted approach to industry exposure helps to “close this gap and get [students] ready and engaged in packaging and STEM education in general,” Mikhail says.
Majeeth’s early career success is just one example of PNW’s efforts in action, as she was able to impress interviewers with demonstrated knowledge from college projects to help secure a position. She applauds the program’s “excellent curriculum with lots of hands-on experience in the technologies used in the workforce.”
Evolving workforce for an evolving industry
Packaging and processing have evolved as fast as the world and technological advancements surrounding them, and the younger generation is no different. Generation Z is unique in its learning style and motivations, necessitating a new approach to teaching that emphasizes real-world exposure.
That not only includes the industry connections PNW offers, but also motivation through “salary after their graduation, and good stories of our students after they finished the mechatronics engineering technology degree, and how they are successful,” Mikhail says.
Mikhail and the mechatronics program emphasize this success-driven motivation by clearly laying out career paths and potential earnings sourced from the school’s alumni database, as well as connections with company human resources departments to explain starting pay and benefits packages.
These salary discussions help to “convince them that a four-year degree will be a big investment for them,” when there’s opportunity after high school to earn figures like $20 an hour without a degree, Mikhail says.
The school also gears its curriculum toward soft skills, or useful attributes that aren’t necessarily found in an engineering textbook like communication and leadership skills. It does this in part to maintain its accreditation of Engineering Technology programs with the internationally recognized ABET, Inc.
PNW also teaches these skills simply because “without soft skills a student will be like a machine,” Mikhail says.
In these soft skill-building exercises, instructors aim to “not give the problem directly, let students try to discuss what is the possible solution, write a technical report, have students sell their idea and make presentations, enhance their entrepreneurial mindset, let them think out of the box and find the problem, discuss with the customers, and find the possible solution,” Mikhail explains.
PNW and similar packaging and engineering schools are doing their part to build up a well-equipped future workforce. To truly minimize the packaging skills gap, though, it will take a continued collective commitment from the entire industry.
By embracing a holistic approach to the problem with education, industry training, intuitive machine design, and a company culture that values and retains talent, the packaging industry can pave the way toward a resilient, innovative future.