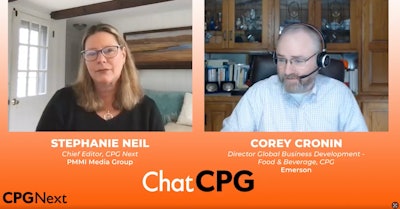
CPG Next’s ChatCPG is a 10 minute (or less) chat with a subject matter expert on all things related to CPGs on a digital transformation journey. Here, we catch up with Corey Cronin, Emerson's director of global business development for the food & beverage and CPG industries, to understand why having a lean manufacturing foundation can benefit a digital transformation project in the plant.
What follows is a transcript of the discussion. Or, simply scroll down to watch the video chat!
Neil: Corey, when we met at PACK EXPO Las Vegas in September, we had a good discussion around what you're doing in your role as director of global business development, food and beverage at Emerson. And I'm just curious as to what you're seeing with the customers that you're meeting with, where they are—the the CPGs in particular—where they are in their digital transformation journey. Are they just starting?
Cronin: Well, I think you see a little bit of everything. You've always got leaders and laggers in that space. But I think most of them are, you know, from a transition perspective, a lot of them are dealing with legacy systems, not only from a controls and automation perspective, but also from a business systems perspective. And then, of course, when you talk about digital transformation, it's about data and getting data places. So then you get into network infrastructure and so forth there's a lot of work to do there. And, and there's a lot of understanding to gain in that space to get them to start making that movement.
So I'm seeing a lot of that. I mean, really, the transition to digital technologies has those obstacles and it requires certain resources to be able to understand what's a good path to take, what do I need to go after and so forth. So that's been probably some of the things that I've been seeing, you know, from issues. And our CPG group really taking the move going forward. They've got resource challenges. I mean, like everybody, how am I going to get this done with the workforce that I've got? It's a lot of new technology and new things to understand, so there's a learning gap there. And then building out that infrastructure can be complex, so you really have got to take an overall view of where do I start, how do I get started, so those are the kind of things that I've been hearing and seeing that are kind of slowing things down, I guess, a little bit in the CPG space. And we're all coming out of COVID and with that, there was a lot of supply chain issues and why enter into another thing right now that's going to cause, you know, maybe disruption with my facilities. I've got to get product out the door. So sometimes with those obstacles in place, it's been kind of slowing things down a bit.
Neil: So maybe starting with the basics is an important part of the journey. And one of the things that you said to me when we were chatting at PACK EXPO is the need to have lean manufacturing principles in place before you even begin. Can you explain that a little bit more? First of all, I'm sure any of the [CPGs] here are going to understand what lean manufacturing principles are, but maybe at a high level, [explain] what you're talking about and why you think that is so important to digital transformation.
Cronin: Yeah, sure. I think when you look at lean manufacturing principles and digital transformation, they complement each other. Very much so. You are combining lean's focus on waste reduction and process optimization with data driven insights to what's going on in your facility. So they're locked at the hip. They work together very well. And when you look at the tool list of lean, you know, things like kanban and value stream, it’s all about information enablement. And if I could get that information faster to make decisions quicker, it's going to have greater impact on improving my product, my product quality, possibly. It makes me more competitive and more profitable as well through that process.
So I think it's important when you look at doing a digital transformation project that you look at it in that lens of lean and continuous improvement. We've all been in continuous improvement, we've got our CI teams and our kaizen events, and we go out of the plant and we we fix things, but think of digital transformation as an additional tool. Actually the best tool to really provide that information that you need in order to improve your process and make that big impact that you want to make.
Neil: So if we're talking about improving the process, which, you know, is important to any aspect of digital transformation, but if you've got these lean principles in place, is there an obvious place to start? Because I think that's kind of what I hear—nobody really knows where to begin.
Cronin: Yeah. I mean, I think really for me, what I would recommend is start small. Really assess what's going on in your facility and your processes. Where are your pain points at? It's just like everything else. All these projects have to have a return on investment. So where can I focus at? Build a list. I mean, every time you have a production review in a staff meeting in the morning, I'm sure there's a list of items that come up repetitively as issues within your facility. What are they? Let's get them on a list. Let's look to see if, hey, does this make sense to maybe be the first of many from a digital transformation point of entry? Looking at going into those parts of the process to make those improvements. Looking at those lean principles that are being applied to reduce waste, waste and time or in product or quality improvements. Can I take those and build that list out, then rank them and then go after them? I mean, I really think that's the best way to go about it. Digital transformation is just an extension of those lean principles that we've always applied in that continuous improvement mindset that all of our manufacturers have.
So, um, that, that's, that's my recommendation. Stay small, pick out those ones that are really impactful that are going to provide that return on investment. And as you get into that and you're doing your digital transformation first test, I mean, It gives you the ability to make adjustments as you go. And it's also kind of setting up a model that you're going to start getting a greater understanding of, you know, the people, the process, and the technology applied. Those are the three things that make digital transformation successful. Your people need to understand the why and the how's of what you're doing. You need to evaluate your process, which is making that list. Where does it make sense to get that ROI?
From a technology perspective, what devices can I put out there that's going to help me that have maybe that edge computing power that's going to give me insights on what's going on to provide me that information that I could make timely decisions on instead of waiting until the end of the shift to find out that I made a bunch of bad product, or maybe I made the wrong product or I set the machine up wrong, or anything like that. And also from an infrastructure perspective. A lot of these plants are older and mature in what they have for infrastructure. They weren't, they weren’t built for data like what we're trying to do with digital transformation. So, you're going to find that out as well in that first project or that pilot that you're going to do. What's it really going to take? So, it really gives you that, that good threshold or foundation to start your transformation journey throughout the rest of your facility.
Neil: Well, that's a really important point because a lot of these companies have legacy systems that have been in place for 30, 40 years, and like you said, they weren't designed to extract information out of them. It was more just to make the process move along. So are there things that we can easily layer on top to do that?
Cronin: I think it's a case by case basis of what they have for an installed infrastructure. I mean, I think the first thing that you need to do from an infrastructure—specifically networking—is if you don't know how to do it, get a professional in to do a network assessment. Figure out what your bottlenecks are going to be from an infrastructure perspective. From a hardware perspective,
do I have the right media? Do I have the right networking tools, routers and switches and software management there to do that? That pipeline of getting that information up to where you can make decisions on, you know, dashboards that are presenting to you is what the goal is. Um, you got to make sure all that stuff is in good shape and ready to handle a higher throughput of data, so to speak, than what they probably were originally designed for. It's going to be case by case.
Neil: Well, you know, as we wrap up here, I think one of the things I keep hearing from everybody is that you can't approach this as a technology or a data problem. It has to be approached as a business problem. And you talked earlier on about making sure you can get that ROI quickly. So do you agree? I mean, as you're talking to your customers, are they focusing on what technology can I put into place to get the return on investment? Or are they saying I need to solve this business problem?
Cronin: I think you see a little bit of both depending upon where you're coming from. If you're coming from an operations management perspective, it's probably not more of the technology, it's the problem. When it's the engineering side, when I'm talking to the engineers, it's about what technology can I apply? So you hear both. I really think that the root of it though, holistically for everyone is, you really have to have a commitment to that cultural change to go to digital transformation. And that goes across all facets of the facility. Everybody needs to embrace it, because you're going to have your naysayers. You're going to have operators where the world's going to completely change from what they're used to. In some cases, engineers are going to have more to support or more information than they ever had to [deal with] and sifting through that and making that information actionable. But really it has to be a top down, bottom up, meet in the middle cultural change, from the operator, from the plant management down to make it successful and to make that transition.