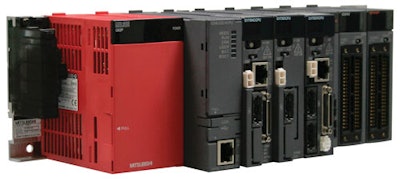
A recent switch to a controls platform based on a robust PLC rather than a PC is said to be bringing improved performance and a more reliable electrical control and motion solution to the thermoforming systems made by Lyle Industries. A key driver behind the switch to the Informer2 controls package, says Lyle’s Gary Sowden, is that with a PC-based system there are too many recurring obsolescence issues.
“Whether it’s components or the operating system, obsolescence is a problem with PC-based platforms,” says Sowden. “By contrast, a PLC-based system is all solid state componentry. There are no hard drives or spinning media.”
The PLC vendor in Lyle’s case is Mitsubishi. Its iQ PLC requires no Windows software. Operator interface terminal and servo drive system are also from Mitsubishi. This single-source supply, says Sowden, is another improvement.
“In the past we wound up acting as our own integrator,” says Sowden. “We were buying a variety of different components from different suppliers on the controls side and we were the ones taking responsibility for integrating them and making them all work together in our control scheme. So we were really excited about the idea of having a system that whether it was the operator interface, the PLC controller, or the servo drives and motors on the machine, they all come from a single source and are all meant to work together. We no longer have to play the role of integrator on our own machine.”
Sowden appreciates some of the “intangibles” that come with the new controls platform. “There’s a reduced panel space, which shrinks the footprint of the machine,” he observes. “But what it really comes down to in terms of improvement is the jump in precision and reliability that came with the new controls platform. For example, a key element in thermoforming is temperature control in the oven. We are now able to achieve plus or minus two-tenths of a degree F in our oven. That’s a huge advantage.”
According to Sowden, the Informer2 platform runs on a variety of Lyle equipment, including thermoformers, horizontal trim presses, and vertical trim presses. Axes of servo motion in such systems might number as many as eight or nine.
“We’ve also been doing a pretty robust business in terms of upgrading some of our already installed equipment with the Informer2 package,” says Sowden
When asked if the Informer2 comes at a premium compared to the controls platform it replaced, Sowden said no. “One of our goals was to improve the technology and stay cost neutral, and that goal, I’m happy to say, was achieved.”